Have you ever used a common steel fastener or even stainless steel fastener in an aluminum part? Then galvanic corrosion is a topic that you should be concerned about.
This frequently overlooked type of corrosion can often appear like normal rust. Galvanic corrosion aka dissimilar metal or bimetallic corrosion, is a type of corrosion that can occur when two metals of different alloys are in contact, accelerating the rate at which one of those metals deteriorates. This corrosion actually endangered the Statue of Liberty, and caused a massive retrofit in the 1980s! The only components required for this process to occur are: two metals of a different alloy, and an electrolyte (most often via salt water, non-purified water, or even high humidity levels).
Below, this nuanced and often overlooked corrosion will be outlined, and steps necessary to avoid it will be explained. Before ordering metal parts to be fabricated, make sure those parts won’t be susceptible to this dangerous phenomenon.
What is Galvanic Corrosion?
The process of galvanic corrosion is similar to how batteries work. One metal has a higher electric potential than the other, and thus an electrical current is generated between them. While the process occurs with any dissimilar metals, it is most prevalent and problematic when there is a severe difference in electric potentials or nobility levels (see the table below).
Nobility in metals is simply how reactive a metal is, thus how susceptible it is to corrosion. For example, the corrosion on the Statue of Liberty occurred when the iron structure came into electrical contact with the copper skin of the statue. These metals are dissimilar enough to cause a significant galvanic corrosion risk, and drastically increase the rate of corrosion.
Another example that is more common is the use of galvanized steel fasteners in stainless steel as is shown in the image below. Even if the metals are coated, the coating can be damaged or scratched during installation or handling, allowing direct contact between the two metals, and rapid galvanic corrosion can then occur. Keep in mind, the contact only needs to be enough to allow electricity to pass between the two metals, so very little is needed, especially if the design is completely submerged in water. If a coating is to be used, it must be durable and very thorough in application.
The example below shows the galvanized steel fastener (anode) has severely corroded, to the point the notch in the fastener for the screwdriver is hardly recognizable. Conversely, the stainless steel part (cathode) is largely untouched by rust, with only a thin surface coat over a small area. This surface coat isn’t even enough to induce pitting, while the fastener would be very difficult to remove due to the level of corrosion. The integrity of the fastener is severely compromised in this example, potentially introducing additional hazards to the design.
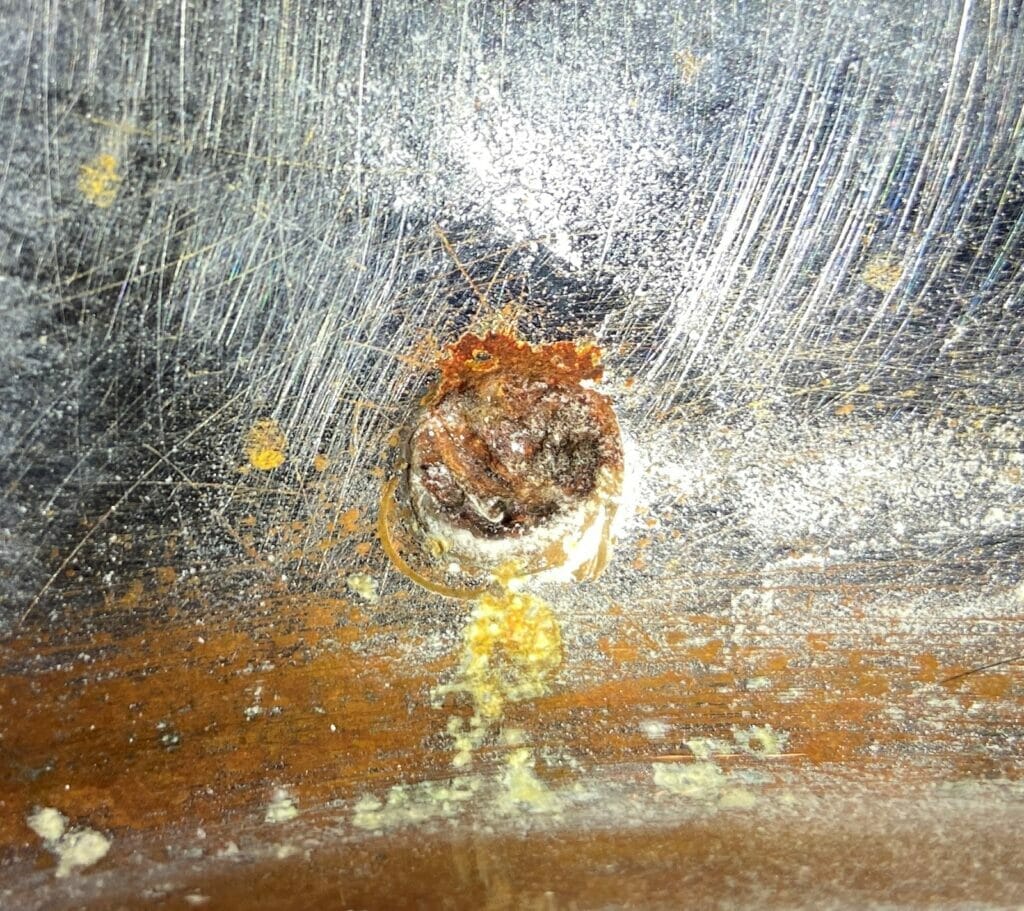
Below is a list of metals from most active to least active (most noble). The further apart the metals are, the more rapidly galvanic corrosion occurs.
Anode/Most Active Metals (the more active metal corrodes) |
Magnesium |
Zinc |
Galvanized Steel |
Aluminum |
Mild Steel |
Cast Iron |
Lead |
Brass |
Copper |
Bronze |
Monel |
Nickel |
Stainless Steel (304) |
Stainless Steel (316) |
Silver |
Titanium |
Gold |
Platinum |
Graphite/Carbon/Carbon Fiber |
Cathode/Most Noble Metals |
Ways to Avoid Galvanic Corrosion
There are three primary ways to avoid galvanic corrosion: choose compatible metals, electrically isolate different metals, or add a protective coating. Of the three, compatible metal choice is the best solution, as it is permanent. Electrically isolating the different metals can be accomplished by using non-conducting washers between fasteners, or having a non-conductive shim, gasket, etc. between the two metals. In effect, you are preventing any electricity from passing between the two pieces of dissimilar metal, electrically insulating them from each other.
There are many coatings to choose from that can mitigate galvanic corrosion risk, each with their own set of pros and cons. The only requirement is that the coating is non-conductive, with the exception of zinc coatings. All coatings have the risk of being damaged during assembly, maintenance, or use, at which point the metals could contact each other and start to rapidly corrode. A very common option with a unique property is coating a part with zinc via either zinc plating or galvanizing. At SendCutSend, we offer zinc plating in several colors for a few different materials.
Zinc is a very active metal, and does not electrically insulate as other coatings do, it acts as a sacrificial coating to protect the other two parts from corrosion. This sacrificial coating is known as a sacrificial anode and is described below.
Sacrificial Anodes: Taking Advantage of Galvanic Corrosion
Intentionally attaching a piece of metal that is more reactive will protect the less reactive metals from corrosion; this is known as a sacrificial anode. While galvanic corrosion is typically thought of as a negative, it can actually be used to a designer’s advantage.
A perfect example of this is the Howard Franklin Bridge in Tampa, Florida. Steel components were corroding rapidly in the saltwater, and a full replacement was an extremely costly endeavor. A sacrificial anode made of zinc, was used to protect the steel structure, and extended the life of the bridge by more than forty years! The boating industry has also been using this technique for decades to protect iron and steel ships.
While sacrificial anodes require maintenance to ensure the sacrificial part doesn’t completely corrode, it is a valid approach to protecting designs when a more permanent option isn’t available.
Composites And Galvanic Corrosion
While galvanic corrosion is most often associated with metallic structures, carbon fiber composites can also create a galvanic cell. This is especially problematic because carbon fiber is often paired with aluminum components or aluminum rivets in order to minimize weight. The carbon within carbon fiber is a conductive material, and is very cathodic. As an example, using aluminum rivets in carbon fiber can significantly weaken the rivets over a very short span of only a couple of years; even less if high moisture levels are present. This weakening can lead to structural failures. The solution for this problem is the same as for metals: to use compatible materials, or isolate the carbon fiber from anodic metals. For example, a single ply of fiberglass between two dissimilar components will work as an isolator to prevent carbon fiber from reacting with aluminum.
Avoid Galvanic Corrosion in Your SendCutSend Laser Cut Parts
Galvanic corrosion is an easy to overlook phenomenon that can have disastrous consequences. Conversely, when used to a designer’s advantage it can also save a lot of maintenance and/or design considerations.
When designing a part for fabrication, consider adding a non-conductive barrier such as anodizing to aluminum, powder coating steels, or using a black oxide coated fastener. If none of these are viable, consider a material change or even ordering an insulating layer such as one of the many plastic laser cut options available from us.
The most important concept to keep in mind is that this type of corrosion is typically only a concern when parts will be exposed to high levels of moisture, and when different metals are in direct contact. More extreme environments, like constant exposure to salt water, can accelerate the problem, so special care should be taken to ensure proper corrosion resistance in these cases.
If you have any questions, feel free to reach out to our support team. When you’re ready, upload your design and get instant pricing today!
If you are new to SendCutSend, here’s a handy step-by-step guide on how to order parts from us: How to Order Parts from SendCutSend (spoiler alert: it’s super simple and intuitive to order from us)