If you’re like us here at SendCutSend, you love science experiments. So before you click off to some other page in search of advice on laser-cut sheet metal parts, go find some aluminum—a frying pan, will do, or maybe an old MacBook Pro. Now grab a butter knife and drag it across the bottom.
See that scratch? It might not look like it, but that’s rust—sort of. The technical term is oxidation. In ferrous metals such as iron and steel, the red, flaky stuff that eventually forms on unprotected surfaces elements is called iron oxide, and given enough time, it will pull down the tallest building, and sink the mightiest ship.
Hats off to atomic number 13
Aluminum, on the other hand, forms aluminum oxide, a hard material that actually protects the underlying surface. Think of it as self-healing. Skip the paint, forget the plating, no need for WD-40—unlike steel, aluminum will last for years and years in even the harshest elements. That doesn’t mean, however, that it will remain pretty.
That’s because unprotected aluminum grows dull and weather-stained over time. This unpleasant situation is easily avoided via many of the same surface coatings used on aluminum’s rust-prone cousins, including electroless nickel, chrome, zinc, and paint. Most experts will tell you, though, that aluminum is more challenging to plate for the same reason it needs no protection—its self-healing nature.

As mentioned in an earlier SendCutSend post, aluminum is frequently powder coated. I won’t recount that glorious story except to say that it’s equivalent to dry paint. Crazy, right? Powder coating, however, is a great way to make laser cut parts beautiful, durable, and corrosion-resistant.
Taking the acid test
Powder coating is not the only way. There’s also anodizing. Simply put, the anodizing process thickens aluminum’s hard oxide layer. At the same time, the parts can be dyed in a rainbow of colors (hence the pretty part) or made even harder and more wear-resistant.
Anodizing is an electrochemical process. It’s been around a long time. Its first iteration was born in 1923 as the Bengough–Stuart process, used to protect seaplane parts against corrosion. A competing process was patented four years later. Since then, it has become the de facto standard for protecting and beautifying aluminum parts, especially machined and smaller sheet metal parts.
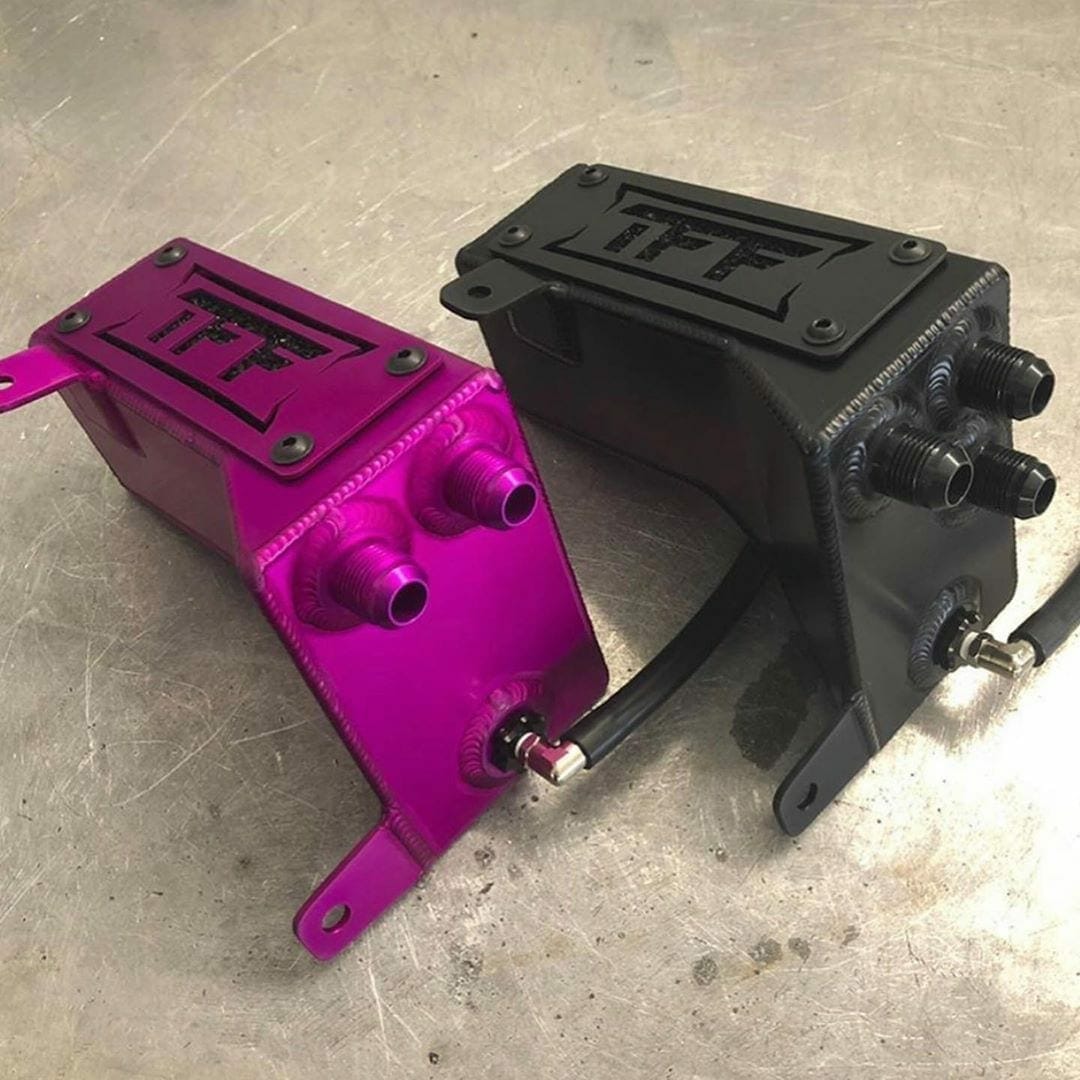
Three basic methods exist. All are covered under the US military standard MIL-A-8625, all use some form of acid as an electrolyte, all send an electric current through the workpiece (the anode) to a series of nearby aluminum bars (the cathode) via the aforementioned acid bath, and all are made colorful (if color is desired) via a post-anodize dying process.
At SendCutSend our in-house anodizing services are available in five colors; black, clear, blue, gold, and red. Currently we can only anodize aluminum. We do offer some tips for DIY anodizing if you choose that route.
Three anodizing options
Type I, or chromic acid anodizing, is the thinnest of all—only a ten-thousandth of an inch (0.0001″) or so in thickness. And even though it offers the fewest color options (mostly black), it is considered “decorative” anodizing. Sulfuric acid anodizing, or Type II, is up to ten times as thick (0.001″), can be dyed in a rainbow of colors, and is the most commonly used of all anodizing processes. Type III, so-called “hard anodize,” makes up the lion’s share, used widely in the aerospace industry for its exceptional wear characteristics.
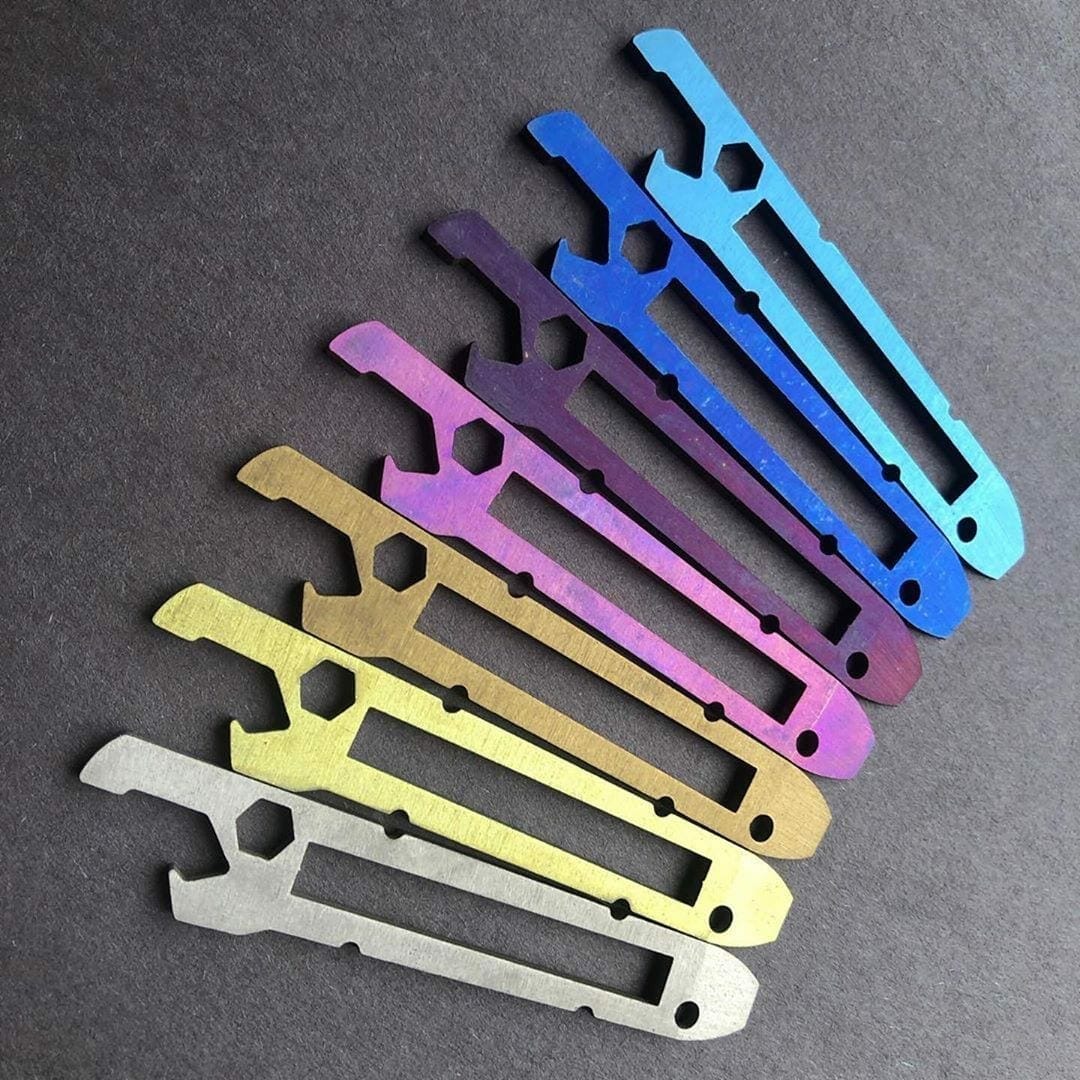
That’s the Reader’s Digest version of the Big Book of Anodizing. It is by no means complete. A handful of other types of anodizing are available, along with a whole truckload of technical, chemical, and metallurgical details that I neglected to mention. For example, anodizing can also be used as a “primer” before painting or plating, and can be “chem-filmed” afterward to increase corrosion resistance even further.
For those interested in the nitty-gritty of this popular finishing option, a host of anodizing books exist, all of which make for some awesome bedtime reading. If reading’s not your thing or you just want to chat a bit about your options for anodizing (or plating, powder coating, etc.) of your laser cut sheet metal parts, we stand ready to answer your questions.
If you’re ready to get started, head to our website to get instant pricing on anodizing aluminum parts.