With today’s high end laser cutters available at the fingertips of even the smallest machine shop, it’s never been easier to manufacture high quality laser cut parts.
But is purchasing and operating a laser cutter really worth it? Between the initial investment and additional costs of labor and maintenance, owning a laser cutter is no small undertaking. It’s for this reason that many businesses and individuals are outsourcing laser cut parts from online manufacturers. Let’s explore the values and true costs of owning a laser cutter, as compared to the reasons one might turn to outsourcing.
Costs of Owning a Laser Cutter
There are a number of costs associated with purchasing, operating, and maintaining a laser cutter of any size. We will examine a range of these costs pertaining specifically to industrial sized laser cutters as well as smaller CO2 lasers.
Initial investment
The initial investment for a high quality, high-power, precision laser cutter can be daunting. For most industrial-grade laser cutters, the cost can range from $250k for a small footprint, low power (1kW – 3kW) machine, to more than $1 million. High power fiber laser cutters with state of the art technology that can easily cut 1” thick steel can cost well over $2 million, before you even add on cool options like automation.
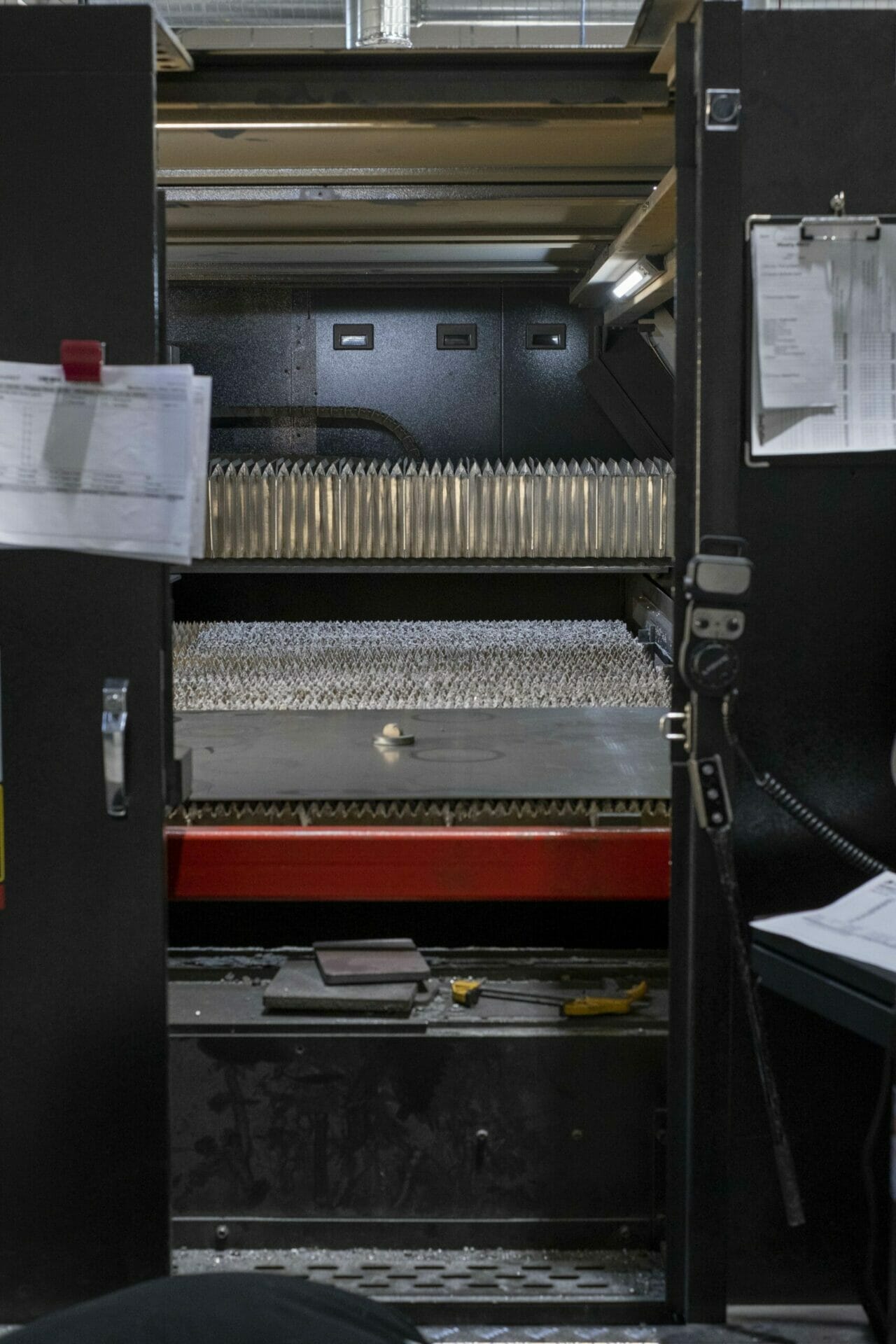
CO2 lasers that are powerful enough to cut plastics, wood and even thin metals start at about $15,000 and scale upwards based on a number of factors, including size and power.
The initial investment costs for any laser cutter depends on the laser technology and capabilities, as well as your machine shop’s needs regarding capacity, level of power, and degree of automation.
Cost of staff and reaching ROI
Small CO2 lasers, which are limited on both size and available materials, can easily be run by just one operator. A larger, high power fiber laser could potentially be run by one operator, but is ideally run by a team of 2-3 staff made up of one operator, one materials handler, and oftentimes one parts handler. Lasers are fast machines that need to be fed material constantly in order to achieve a positive ROI.
High powered fiber lasers should be run as close as possible to 24 hours a day to maximize its efficiency and ROI. Ideally, all the parts cut on this laser are eligible for automatic loading and unloading. However, since this can’t always be the case (job shops), your shop should be prepared to have 2-3 shifts of several people each working around the clock to load and unload the material.
Materials and storage costs
The cost of materials is as much a part of the cost of the laser cutter as it is the cost of the parts you’re cutting. Depending on the part geometry and how the parts are nested in programming, anywhere from 10% to 50% of the raw material is wasted and has to be recycled. This can be partially mitigated by efficient sheet utilization, but if you aren’t also running the laser often enough to utilize all of the raw material, the amount and cost of scrapped material will be high.
If you don’t have enough parts to utilize all the raw material when laser cutting, you will also probably face issues with price scaling as it’s often significantly cheaper to order material in large quantities. However, if you can order large quantities of material and can justify it with the near constant use of the laser cutter, you will eventually need to address a rather glaring storage problem. This can be expensive for smaller machine shops who may have to store the material for an extended period of time before it’s all used.
The most efficient material sizes may be sheets of 4’x4’, 4×10’, or even 5’x12’. Storing and handling materials of those sizes requires a lot of space, specialized equipment (forklifts, cranes, etc.), and unique training for laser operators. Since it may be difficult for shops to find the space for such storage and equipment, they will have to turn to renting additional space on top of ordering the larger sheets in large quantities. As you can see, materials costs are not as cut and dry as they may appear.
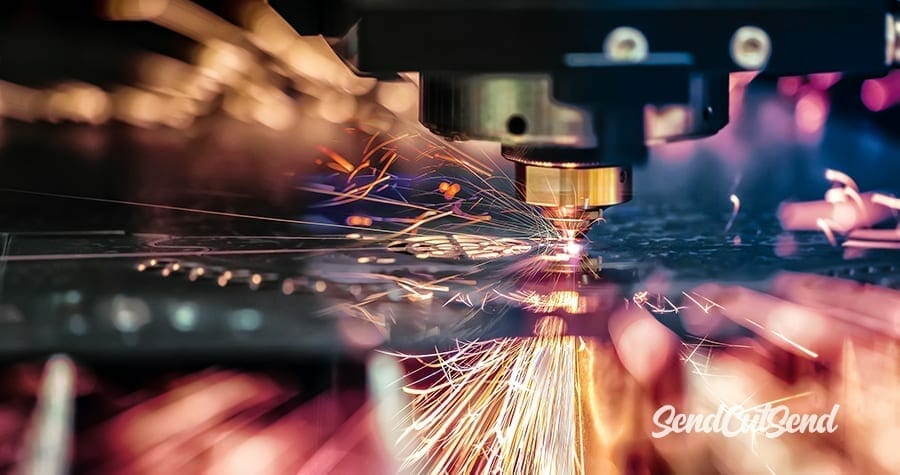
Maintenance Needs and Consumables
High power fiber lasers require a significant amount of maintenance which will play into the cost of daily operation.
- Lens and nozzle alignment (daily)
- Lens savers (protective lens cover): $10-$20 each, (daily)
- Emptying scrap bins/dust collection units (daily)
- Replacing sacrificial slats for work tables: $1-1.50 per pound, plus cutting time (every 2-3 days to once a month, depending on production levels)
- Lubrication (daily/weekly/monthly depending on machine and use)
- Replacing air/gas filters: $2,000 – $4,000, (semi-annually)
- Cleaning/replacing dust collector filters (depends on materials being cut and level of machine use): $800 – $2,000, (every 6 months)
- Large amounts of assist gas – typically liquid nitrogen or N2 generated from atmosphere using specialized equipment: $3,000 – $30,000 per month, depending on volume
CO2 lasers require less maintenance and consumables, but what they make up for in convenience, they lose in power, available materials, and capacity.
- Changing distilled water in the chiller every 100 hours of cutting
- Lubricating X/Y axis points
- Adjusting alignment (daily)
- Replacing laser tube: $700-$4,000 each, (every 2,000-5,000 hours, depending on power output)
Summary of Advantages and Disadvantages for an In House Laser Cutter
The rapid turnaround time in your laser cut parts is the biggest advantage to owning your own laser cutter. Depending on the part, you can go from a drawing to a finished product in mere minutes. Most outsourcing companies can take anywhere from two days to several weeks.
Iterating on existing designs or creating new prototypes is also a perfect application for an in house laser cutter for any size business or machine shop. With the right tuning and training, it takes no time at all to update your design, cut and assemble it, test, and do it all over again. This can work for anything from robotics designers to product testing, and is far faster and cheaper than repeatedly placing a large outsourced order when you only need a couple parts.
Owning and operating your own laser cutter also gives you complete control over production rate and quality control. It can be frustrating to relay tolerances and specific needs to a third party, but if you’re cutting your own parts in the first place, that additional communication is cut out entirely and gives you a better handle on the final quality of your parts. However it does mean you can’t “pass the buck” to your third party supplier, so keep that in mind when you make promises for the tolerances and look of your final parts!
The most glaring disadvantages for owning a laser cutter is the space needed to house one, the time needed to learn how to operate it, and the money needed for the initial investment, materials, and ongoing maintenance and operation. If you’re a large manufacturer with a full warehouse and a crew of people able to operate it, purchasing a laser cutter is viable and probably wise. However, if you’ve got a small to medium sized machine shop and your business output is too low for the demands of an industrial laser cutter, you should defer to outsourcing as it will save you time, space, and money.
Benefits of Outsourcing Laser Cut Parts
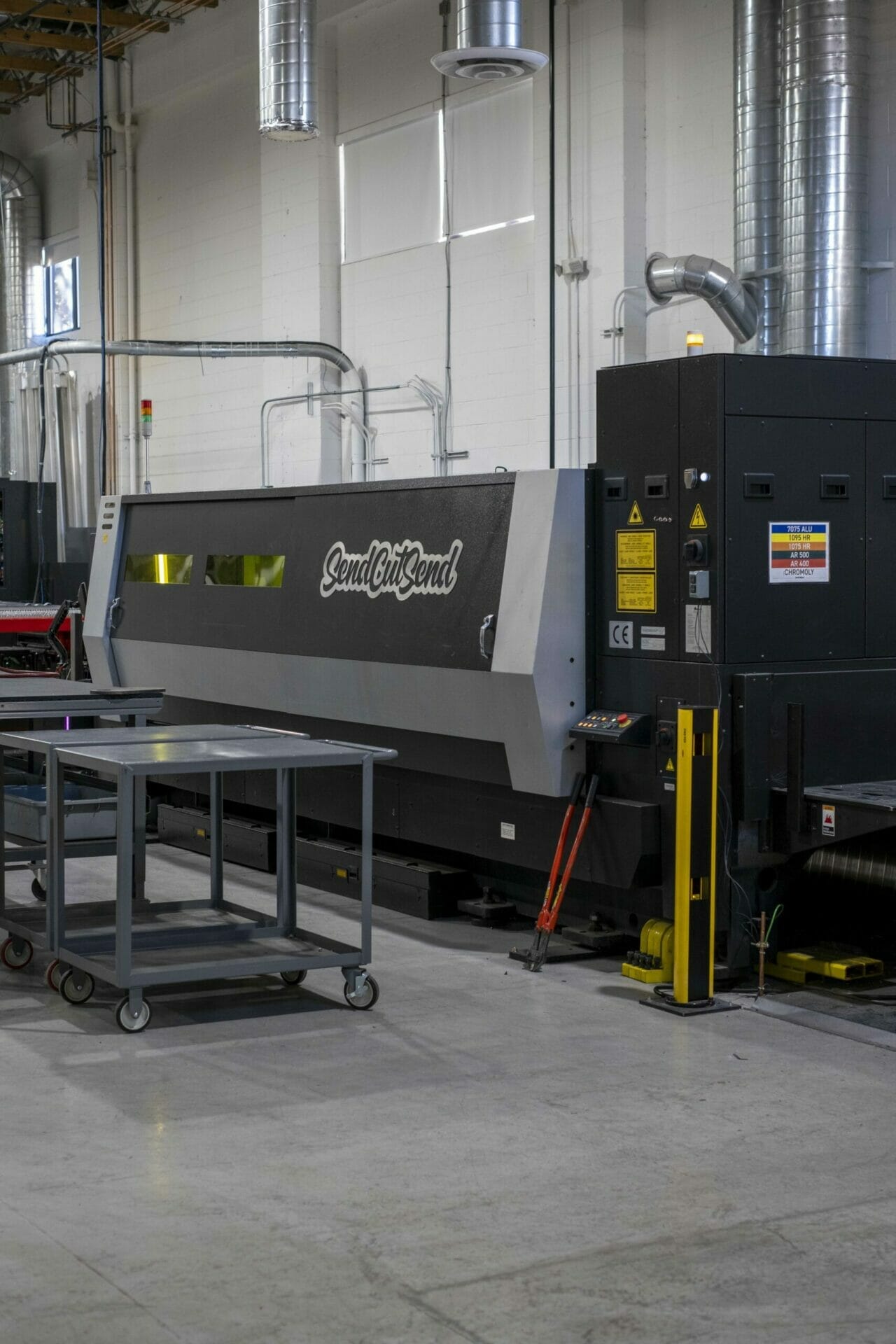
Outsourcing your laser cut parts would be an ideal alternative to the responsibility of purchasing and operating your own laser cutter. Obviously with outsourcing, there is no large initial investment like with purchasing a laser cutter. Additionally, due to economics of scale, large scale manufacturers can oftentimes machine parts cheaper than the cost of the materials you would order and then have to laser cut yourself. So you could potentially get your parts at or cheaper than the price of raw materials.
Outsourcing is in many ways more convenient than operating your own laser cutter. Laser cutters take up space in your machine shop, as does processing equipment and material storage, and outsourcing cuts that away entirely. In terms of maintenance, if you outsource laser cutting, you don’t need to hire labor, deal with equipment failures or replacements, or take on creation and storage of assist gasses. You also don’t have to worry about scrap metal storage or recycling.
As we mention the purchasing or creation and storage of assist gasses, it’s important to also note that laser cutter owners need to obtain special permits from the EPA, OSHA, fire marshal, and other local authorities due to the dangers of keeping a laser cutter and the tools needed to operate it. If you outsource, that is your vendor’s problem, you can relax!
Many large scale manufacturers are able to easily justify state of the art, high powered fiber lasers because they have the output necessary to reach ROI on one relatively quickly. This means that if you outsource, your parts will most likely be cut on a laser cutter that is better able to reach tight tolerances and high quality cuts than the mid-tier laser cutter many small manufacturers use. You’re better able to guarantee high quality parts because they’re cut on a high quality laser.
There are, of course, downsides to outsourcing as there is with anything. As we mentioned, outsourcing is a slower turnaround time from concept to finished part. Many manufacturers take weeks to machine your parts, but a few are ahead of the curve and will only take 2-4 days. Outsourcing is also more expensive if you have a high volume of needed parts over an extended period, but remember that if it’s high enough, you can justify purchasing a laser cutter. Outsourcing is still ideal (and cheaper) for businesses with a lower output on a laser cutter that prevents them from running it 24/7.
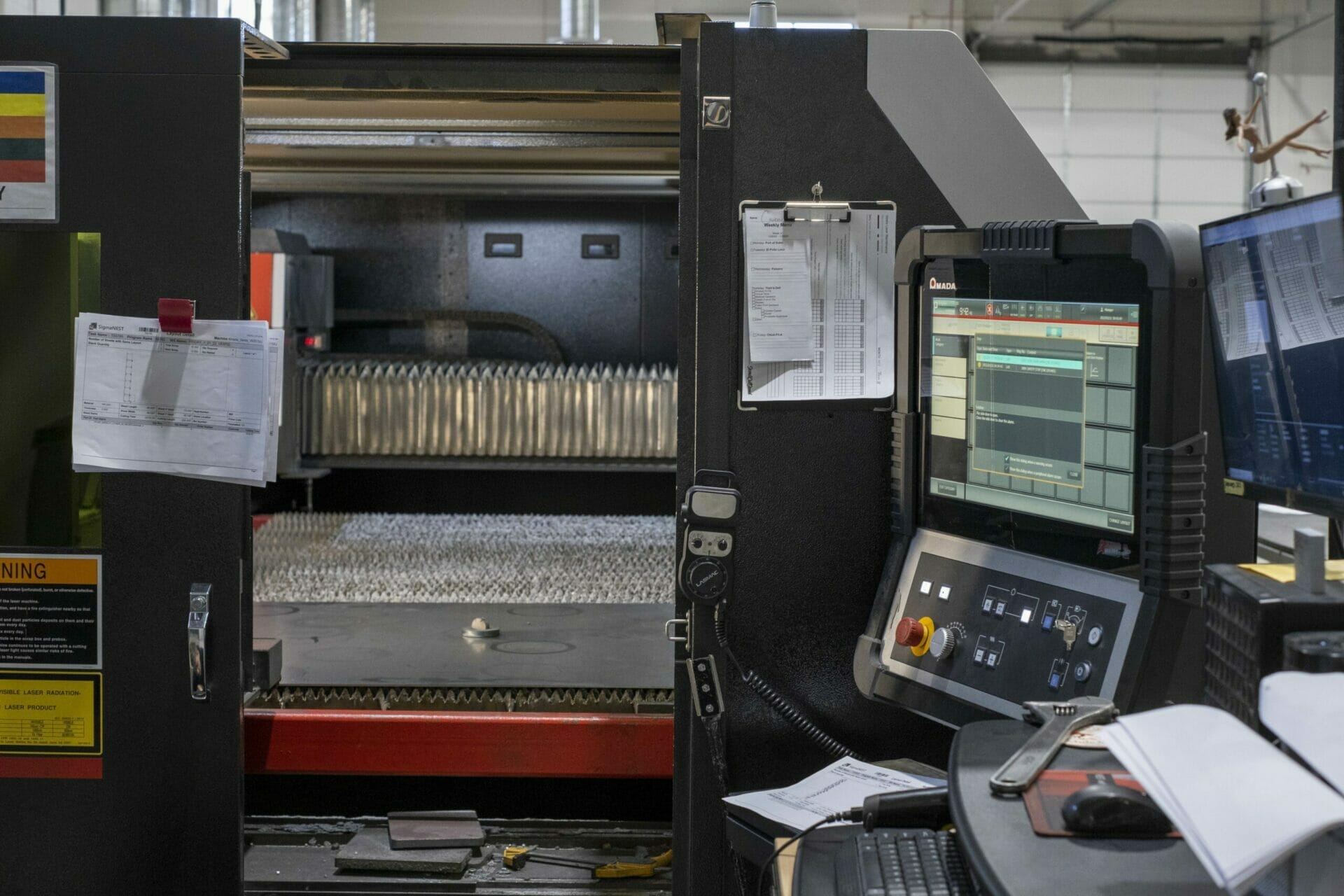
Laser Cutting In House or Outsourcing?
You will have to take your own needs into account when making this decision for your business or shop, but we see outsourcing as an elegant solution to many (if not all) of the problems that purchasing and maintaining a laser cutter in house presents.
Today’s manufacturers and fabricators are revolutionizing the world of machining, and with new advances and innovations appearing in laser cutters all the time, trusting a third party with your laser cut parts today feels like a sigh of relief.
Do you still have questions or concerns about outsourcing? Reach out to SendCutSend on our Instagram or contact our support team.