You have a project that needs laser-cut metal parts…but welding isn’t your thing. How should you assemble metal parts without welding?
Laser-cutting to the rescue
Laser-cutting is faster and more accurate than waterjet, so you upload your drawing to the SendCutSend website and sort through the available metals there.
There’s just one problem: You can’t weld worth a darn. We all have our gifts, and try as you might, this one isn’t part of your skillset. Besides, even if you were a good welder, you can’t afford the equipment. That’s okay. You’re nothing if not resourceful. You begin assessing available alternatives:
Two-part epoxy
Glue might sound like a silly choice for fastening metal parts, but good epoxy is amazing stuff. In fact, cosmonauts used a bit of glue and cloth to fix a hole in the Soyuz MS-09 spacecraft as it docked with the International Space station in 2018. Provided you clean the surfaces with acetone or mineral spirits, roughen them up a bit with some sandpaper, and then etch the aluminum with a little citric acid immediately before assembly, a good two-part epoxy is all you need.
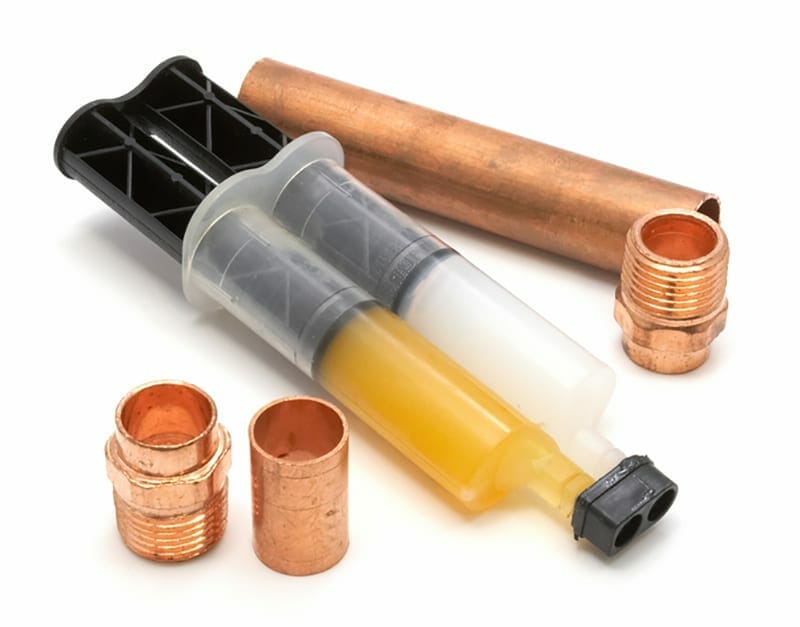
Rivets
Another great alternative is rivets. If they’re good enough for airplanes, they’re good enough for just about anything. They’re inexpensive, easy to install, and if you make a mistake or break a rivet, simply drill it out and install another. If you thought ahead, you would have drawn some rivet holes in your CAD file before uploading it to SendCutSend’s online instant quoting tool, but drilling them by hand is a simple task. You’ll need to order a rivet gun, however (about twenty bucks on Amazon), along with the correct type and length of rivet. A general guideline is one-and-a-half times the combined material thickness, and aluminum parts require aluminum rivets, steel needs steel, and so on. Again, no big deal.
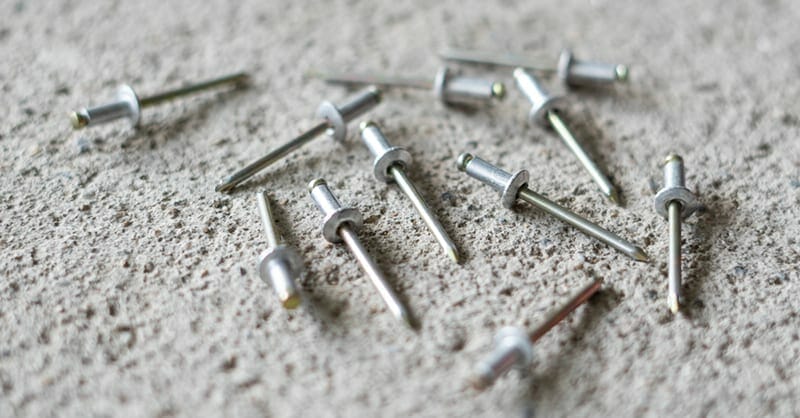
Brazing and soldering
Though similar to welding, neither of these joining methods call for expensive equipment, nor the skills needed to “lay down a bead” of molten metal. They do require a gas torch, some flux (a chemical compound), and the correct filler metal, but brazing or soldering two laser-cut parts together is no more difficult than installing a kitchen faucet.
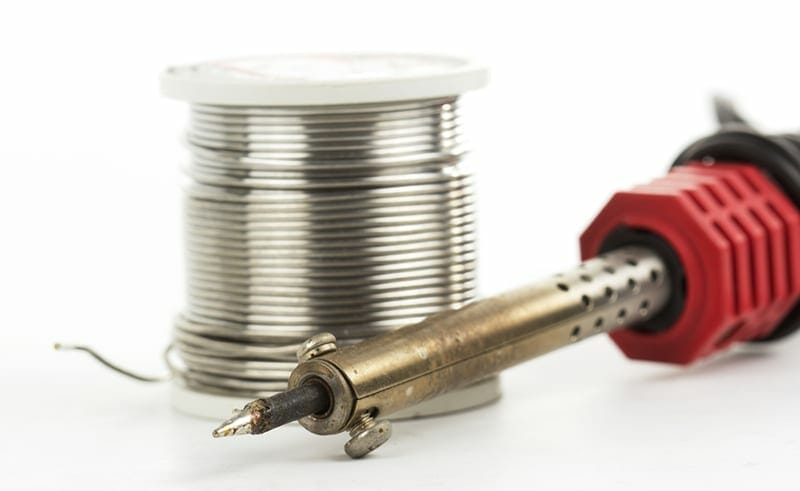
So what’s the difference? Soldering is performed with filler metals that melt at 450°C (842°F) or below, while those used with brazing melt above this temperature. That makes brazed joints more robust than soldered ones, but either is quite suitable most projects. As with epoxy, the parts must be thoroughly cleaned before joining, although the flux used in either process serves to remove any of the oxidization that occurs on bare aluminum surfaces.
Who needs welders?
Other joining methods exist. Nuts and bolts are one option, although a bit bulky for some applications. Sheet metal screws eliminate the need for a mating nut, but generally require that holes be threaded before assembly (thin-gage aluminum can be joined with self-tapping screws). There’s also spot welding. This is simple enough for the proverbial caveman, although it does need special welding equipment (you guessed it—a spot welder).
If you aren’t a welder, but still need to stick some metal together, a bit of epoxy or rivets will help you get the job done.