Rob & Stu Automotive Concepts leverages SendCutSend’s precision laser cutting services for their custom automotive fabrication and vehicle restoration projects. From their 1965 Mustang build to various other ambitious projects, this father-son duo uses SendCutSend’s online tools and resources to enhance their design process, saving time and ensuring high-quality results. By utilizing digital templates and outsourcing complex parts, Rob & Stu can focus on their craft while overcoming tool and space limitations in their shop.
Company: Rob & Stu Automotive Concepts
Product: Automotive Fabrication & Vehicle Restoration
Industries: Automotive
SendCutSend Services: Custom Brackets & Parts
Social media: Instagram | Facebook
Laser Cut Parts for Classic Car Restoration
Rob & Stu have leaned on SendCutSend for a handful of parts for their 1965 Mustang build – all beginning in the “origami phase,” creating paper templates that Will hands off to his wife for digital design, “She handles our photography, social, and all things digital. I’ll stick to the cars,” he jokes.
Without previous experience in CAD design, the duo have taken advantage of SendCutSend’s online literature and videos to shorten the design process and maximize their time – and when the design file has a hiccup, SendCutSend has been there to walk them through required adjustments.
“We’ve never claimed to be experts,” Will says, “we’re still experimenting with when it makes the most sense to send a file out and when we should fabricate in-house.”
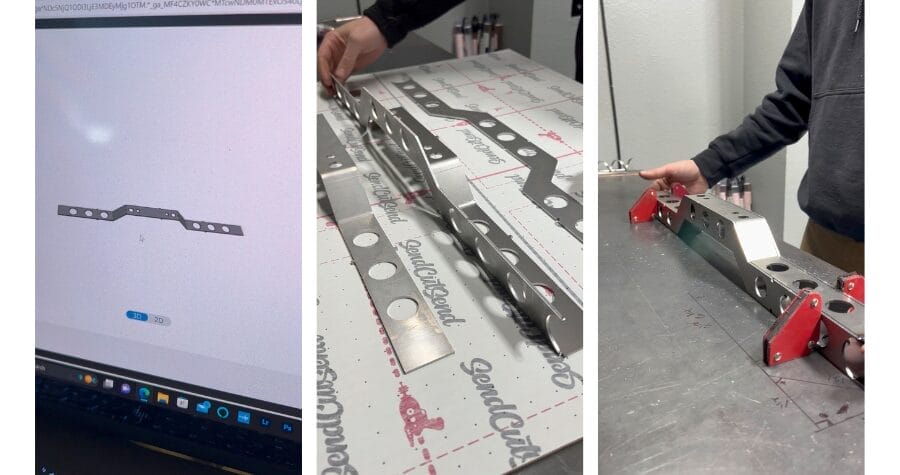
Custom Automotive Fabrication: Learning and Growing
Will is a fabricator turned automotive technician for a Ferrari racing team who always dreamed of opening his own automotive shop. In 2022, Will and his father founded Rob & Stu, named after Will and his father’s middle names.
Will’s focus has always been on building something of quality that looks (and sounds) cool – but in the age of viral videos, and thanks to a growing digital following and some unexpected partnerships, they were able to prioritize their custom builds sooner than expected.
Their humble single-bay shop is already bursting at the seams with projects in the queue. A 1965 Mustang restomod sits on the lift, with a 1969 Mustang in the planning stages for a ground-up custom build. There’s even a 1980s speed boat parked outside the shop they spotted on Marketplace and couldn’t turn down.
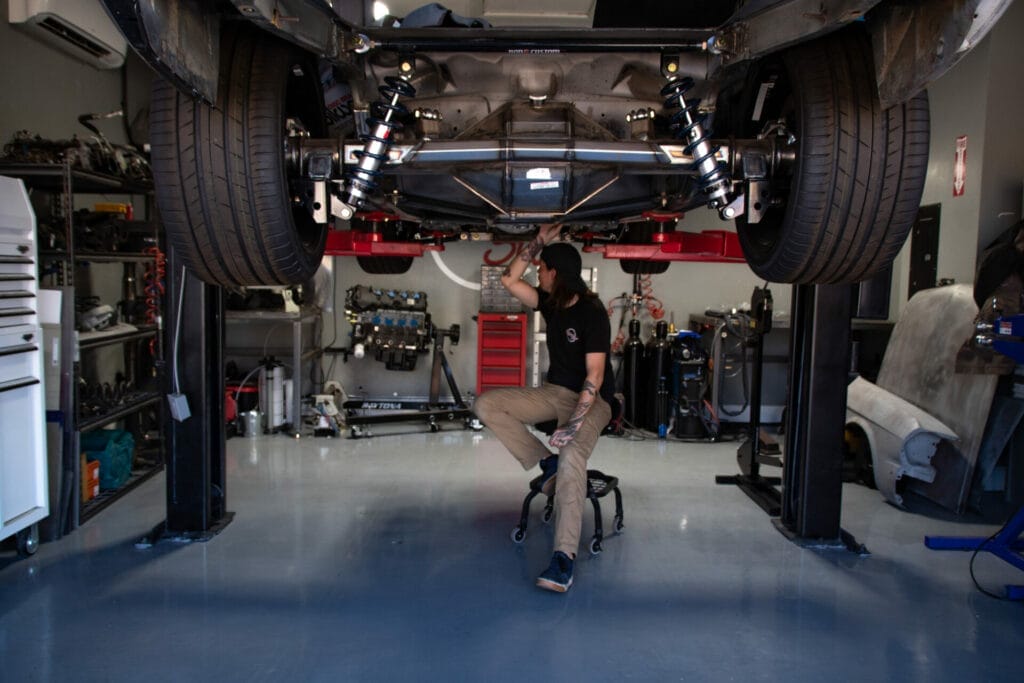
Utilizing Sheet Metal Manufacturing for Precision Automotive Builds
The current build, the ‘65 Mustang, is a restomod utilizing minimal aftermarket parts. Almost anything Will could design and build in-house he’s done so far, from simple brackets to the bulkhead. But the duo’s “Director of Spark” ran into some roadblocks as the build progressed.
“There are parts that we don’t have the tools or expertise to fabricate by hand. Pieces that were simple enough to design on paper but would have been too time-consuming or costly to develop in the shop.”
Will admits he’s still figuring things out and learning a lot as he goes. Not having to rely on only his own two hands to finish the ‘65 Mustang means “having to get out of my own way and knowing when to ask for help,” he shares.
As the sole fabricator in the shop, finishing this build on schedule and on budget is where SendCutSend’s online laser cutting services come in.
Speed and Accuracy with Laser Cutting in Auto Restoration
Engine and transmission mounts require a great deal of precision. Rob & Stu have translated their paper templates digitally and had SendCutSend produce them while they continue to make progress on other parts of the build.
“Something that would have taken us out of pocket for days to fabricate with that level of precision, we can kick to SendCutSend and just keep working. It’s a huge time saver and just makes sense.”
While their online following may be growing, their current shop space isn’t. Many of the specialty tools needed to produce and fabricate parts for a custom build, their floor space simply can’t accommodate – and they’ve realized it doesn’t need to.
“Being able to virtually design the high-quality parts we want to integrate into this build and have SendCutSend do the heavy lifting means we don’t have to compromise on quality of materials or design due to tool or space limitations.”
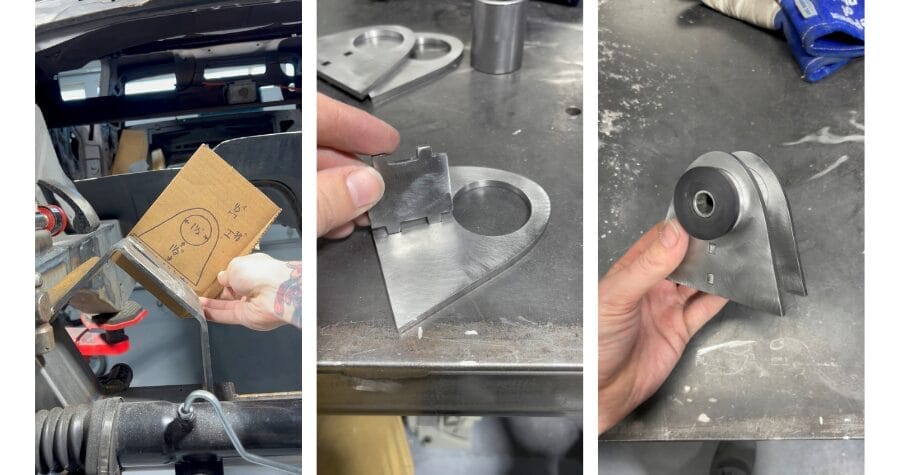
Maximizing Efficiency with Laser Cutting for Custom Car Parts
Following advice from SendCutSend’s video library, the duo have used the built-in bend calculator, incorporated interior cuts to save weight, and added tabs and slots to assist with assembly on their transmission mount.
For their brake and clutch reservoir cage, they used SendCutSend’s hardware installation services with the PEM fasteners for a streamlined finished look. They even used standoffs for a “just for fun” project when they designed a dual-layer metal sign with the shop logo – which he admits may have been for the visual draw in their social content.
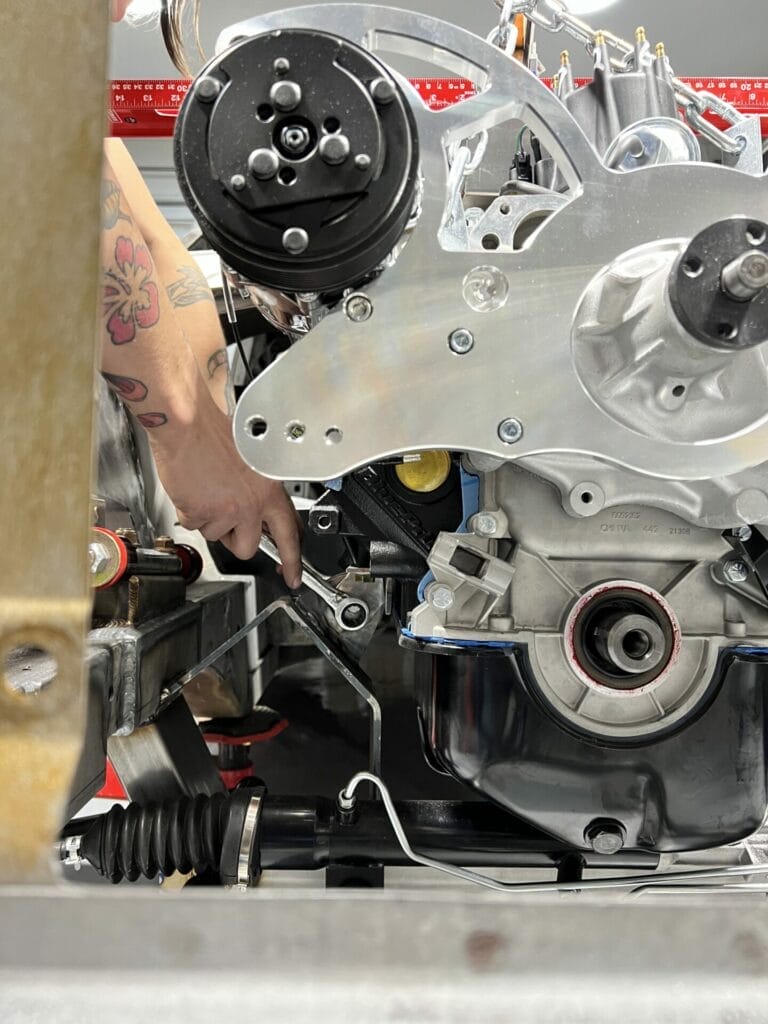
“SendCutSend has already saved us a ton of time, but now knowing the full extent of what we can design with them opens up so many options for our next build,” says Will. “I can either spend a whole day designing, cutting, bending, and deburring a single bracket to install an oil cooler, or I can send it off to Send Cut Send. The level of quality in their short turnaround time is unmatched”.
Pro Tips for Custom Automotive Fabrication with SendCutSend
At home, Will’s working on a school bus conversion for the family. Next up is cutting off and lifting the roof ten inches. SendCutSend provided the new sections of hat channels for the frame – of which over 20 identical parts are needed for this raising feat.
His advice? “Before you order a large quantity of parts, order one, check the fit, or order it in a cheaper material for a prototype. Save yourself and your wallet the heartache.”
We had to ask if he’d followed his own advice – thankfully, he did.
Setting Up for Success in Sheet Metal Automotive Projects
The ‘65 Mustang is the first of many for Rob & Stu. They’re working with renowned digital artists on their next build, the ‘69 Mustang, and will be reaching out to sponsors soon to help bring that project to life – hoping for an opportunity to showcase at SEMA and PRI.
Having (almost) gone through it once now, they’ve learned where and when to reach out to SendCutSend for help. We can’t wait to see what Rob & Stu pull off next and are looking forward to being a part of it.
Whether you’re in the automotive industry or just looking for inspiration on your next build, follow them on Instagram, @RobAndStu, to keep up with their progress.
Do you have a project build, or have you already shown off your designs with SendCutSend parts? We want to hear about it! Fill out our Partner with Us form and we’ll be in touch!