In the world of manufacturing, small details make a big impact. For sheet metal parts, surface finishing and deburring are key steps that go beyond appearances – they ensure safe handling, precision, and functionality.
No matter your project, understanding the available surface finishing processes and their limitations can help you select the best method for your application.
This article will highlight the finishing procedures offered here at SendCutSend, as well as various other methods you can use to refine your part if needed.
Surface Finish and Deburring Deep Dive
Raw material often comes with minor scratches, identification markings, and cosmetic blemishes from the mill. Additionally, surface and edge imperfections are inherent to almost all manufacturing processes including laser and waterjet cutting, and CNC routing.
Common Finish Imperfections Include:
- Raw material markings, oxidation, scratches, and other cosmetic defects from the material supplier.
- Burrs, dross, and slight discoloration from laser cutting.
- Bend or witness marks from forming operations.
- Discoloration and surface blemishes from welding (not currently offered).
- Fingerprints and smudges from handling.
So how do we address these issues?
The Finishing Methods Used
SendCutSend currently offers two of the most reliable and effective deburring processes in the industry. These methods are cost-effective, gentle, and maintain the dimensional integrity and material properties of your parts, while also improving edge and surface quality.
Linear Deburring
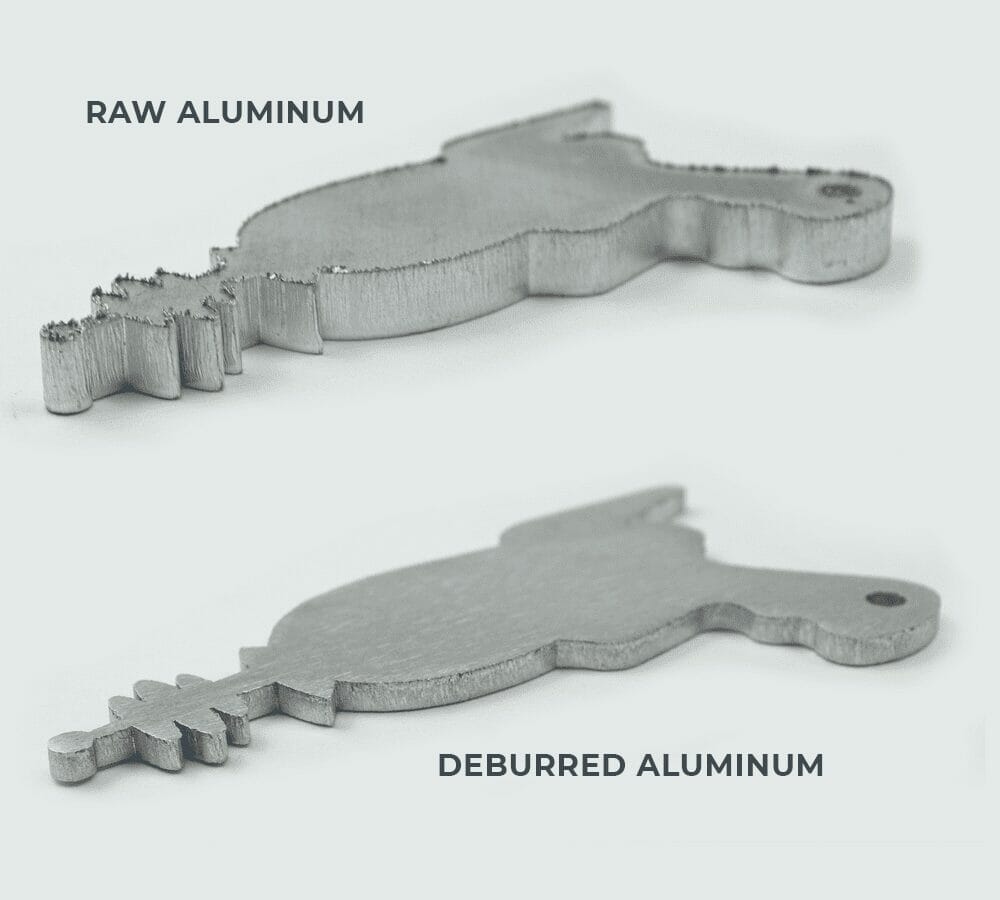
- Process: Flat parts are conveyed through abrasive belts to remove top and bottom surface burrs.
- Finish: Results in a smooth, deburred part. Removes raw material identification markings and reduces imperfections. Softer materials such as aluminum and brass will result in a more uniform finish (not a true cosmetic straight-grain finish).
- Applications: Optimal for large flat parts, providing improved visual appearance over raw stock material. Cost-effective and fast (does not increase cost or lead time).
- Limitations: Suitable for flat parts only, material and size constraints apply. Burrs may remain along the boundary profile as edges are not fully rolled in the process. Slight flaws and handling marks, smudges, etc. may remain. Witness or bend marks may be visible on the part exterior if forming operations are included after deburring.
* Please note, if you do not wish your eligible parts to be deburred be sure to uncheck the deburring operation during part configuration.
Tumbling
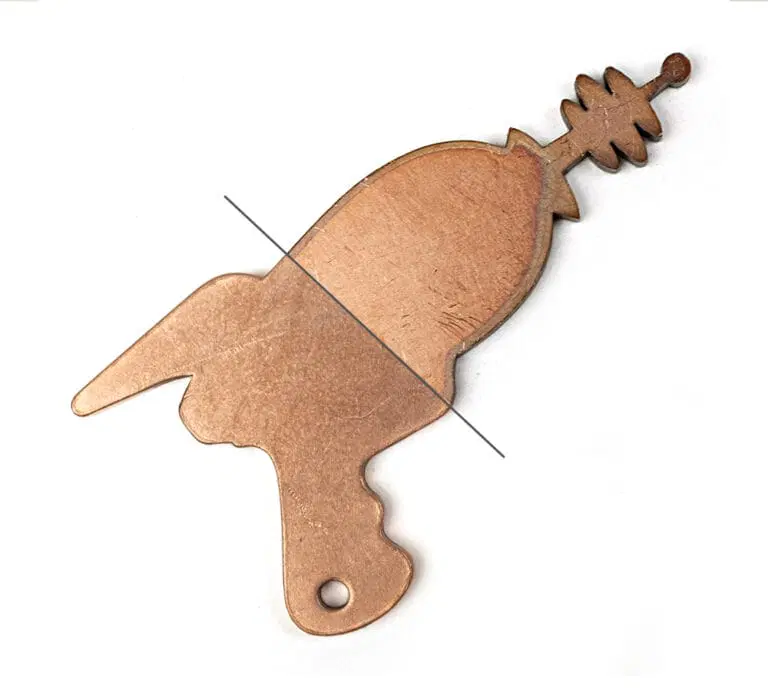
- Process: Parts are placed into a vibrating or rotating mixture of ceramic tumbling media and liquid finishing compound. The media continuously moves against the parts, abrading all edges and surfaces.
- Finish: Slightly softened edges, more uniform appearance and reduced burrs.
- Applications: Smaller parts requiring lightly rolled edges and improved surfaces. Enhances surface quality more so than linear deburring – gets parts ready for further processing or plating and allows for safe handling and assembly. Tumbling is a fantastic low-cost mass-finishing solution.
- Limitations: Part edges may not be fully rounded per your requirements, and minor imperfections may remain. Parts must fall within a select range of materials and dimensions. Tumbling is not ideal for large pieces or those containing delicate geometries. Small cutouts (<.030”) may not be fully deburred due to the size of the media
*Please note that tumbling must be selected manually during part configuration; additional lead time will apply.
Secondary Finishing Processes For Your Shop
If you have highly cosmetic parts requiring a level of finish not currently offered at SendCutSend, or are performing welding, coating, or assembly yourself, stay tuned for tried-and-true finishing methods.
Media Blasting
Abrasive media (such as glass bead or aluminum oxide) is accelerated by compressed air to clean, smooth, and blend the surfaces of your part. Effective in providing a uniform and textured finish, with a high degree of flexibility. Various finishes are possible depending on media selection and blasting pressure.
- Commonly used to prep for and enhance paint and powder coat adhesion.
- Bead blasting before anodizing results in a matte finish.
Limitations of media blasting
Manual and time-consuming, results are dependent on operator proficiency. Large and thin geometries should be avoided due to the potential for warping. Requires expensive equipment including a blast cabinet and high-output air compressor.
Sanding
Dual-action (DA), orbital, or hand sanding can create uniform, durable surfaces on large, flat parts. Sanding and scuff pads are available with a wide range of grits, allowing a variety of finishes to be achieved.
- Best for large, flat surfaces.
- Can easily repair or “touch up” surfaces if minor damage occurs.
Limitations of sanding
Requires careful control to avoid inconsistencies or swirl marks in the final product. Sanding is a manual and time-consuming operation.
Straight Graining
Straight graining is a cosmetic finish with a linear, consistent, unidirectional grain pattern. Similar to the finish found on stainless appliances or commercial fixtures. A belt or sanding wheel is used to apply the grain pattern to one or both sides of the part. Common equipment used in industrial settings are stroke sanders and Timesavers.
Limitations of straight graining
Straight graining sheet metal surfaces is a laborious and skilled endeavor. Straight-grain finishes are not easily achieved in the home shop.
Polishing
Polishing compounds create high-gloss, reflective polished sheet metal surfaces. Polishing is usually the final step after progressively finer sanding operations.
Limitations of polishing
Time-consuming, especially for large components or high quantities. Results may vary.
Manual Deburring
Manual deburring methods include swivel deburring tools, files, wire wheels, countersinks, etc. We recommend choosing one of our offered deburring solutions and then performing any necessary touch-ups to meet your specific requirements.
The Benefits of Deburring with SendCutSend
At SendCutSend, after manufacturing, your order is carefully secured between a durable cardboard backing and protective film before boxing. The tightly wrapped plastic film ensures parts remain stationary during transit, preventing damage. Our attention to detail ensures that your parts maintain the same level of quality and finish as when they left our shop.
We hope this overview of surface finish and deburring processes has been helpful. For more detailed articles and useful resources, explore the comprehensive content available on our website. If you have any questions or need assistance with your project we are here to help.