Fabrication Station:
From bikes to bouffants, Sean Hogan thinks outside the box.
There’s a hair salon on 10th Avenue in Portland, one of many such small businesses in a town known for its microbreweries and coffeehouses. It sits in a nondescript brick building on a nondescript street, a ten-minute walk due east from Old Town. The logo on the window proclaims the name of this five-year-old company—de stijl—in lowercase white letters. A horizontal bar serves to dot the i and j.
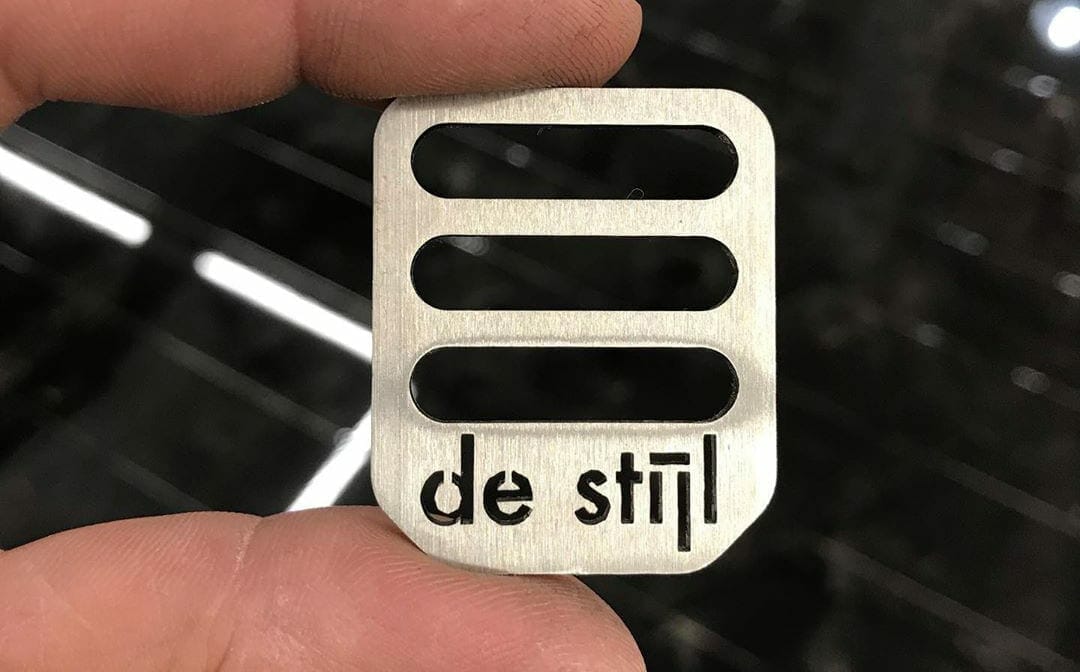
You might see a motorcycle out front—a Ducati SS, perhaps, or a Yamaha Virago—although it could be practically anything with two wheels. Owner Sean Hogan has “around fifteen motorcycles” in all, most of them customized via laser cutting with details like unique plate carriers and radiator covers. There’s even a Ducati in the back, one of many unique things about an admittedly unique space. As his website notes, Hogan and his coworkers are like toddlers with finger paints and butcher paper, working furiously to fill a blank canvas. His salon reflects that passion.
Gaining traction
Though Hogan has been in the hairdressing business since 2001, he only recently embarked on a new vocation, one that you might have guessed by now. He builds motorcycles.
“I’ve had bikes for much of my life, and then one day in 2017, I decided to try something new, something I’ve never done before,” Hogan said. “I bought a 90-amp welding machine from Harbor Freight, a $100 tube bender from Amazon, and started playing around with different CAD packages. Pretty soon I was making subframes and other tubular components, and then expanded from there.”
His first bike was a café racer. If you’ve never heard of them, Wikipedia defines café racers as “His first bike was a café racer. If you’ve never heard of them, Wikipedia defines café racers as “lightweight, powerful motorcycles optimized for speed and handling rather than comfort, and quick rides over short distances.” Whatever you call it, the bike was a success. Hogan began gaining traction via social media and knew he was on the right path. He soon took a CAD class at an area vocational-technical school and began designing parts for sheet metal.
The only problem was, he didn’t have the laser cutting equipment to manufacture them. That’s when he heard about SendCutSend, an online laser cutting service in Reno, Nevada. “I’d designed a custom exhaust flange for a bike I was working on but had no way to cut it,” he said. “I’d never worked with them before, but their automated quote seemed quite reasonable, so I uploaded the file to their website. I figured, ‘Why not? If it fails, I’m only out 29 bucks, their minimum charge.’”
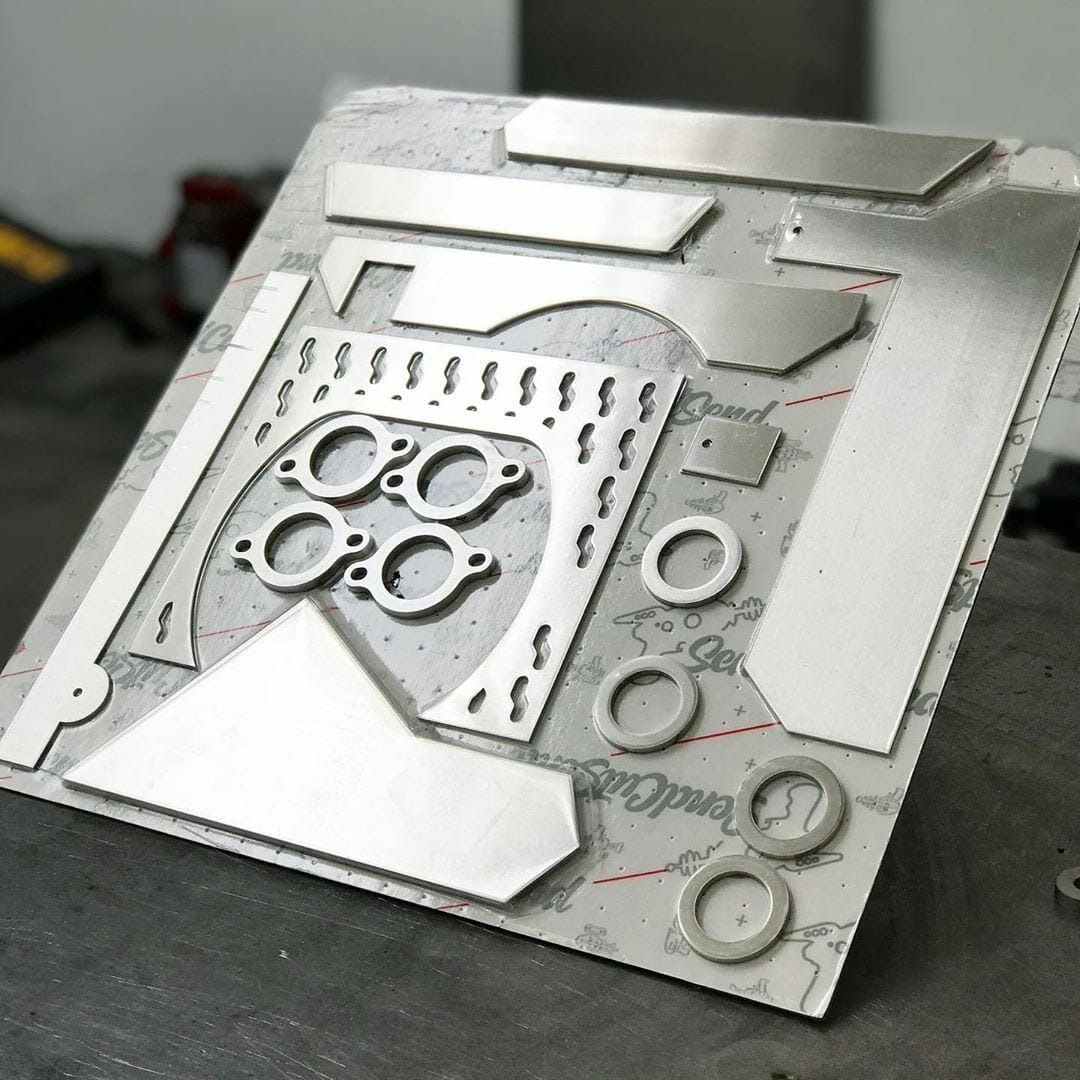
There was no failure, however. The part fit perfectly, and Hogan began sending more work to SendCutSend. He soon found himself launching destijlmoto.com, an E-commerce website offering a range of laser-cut and CNC-machined motorcycle parts. He also started designing his next bike, as well as some custom parts for “Unimogs and other weird stuff.”
No fear of failure
IIronically, this is all new territory for Hogan. He explained that he’s always been interested in making things and has long hung around with people in the industrial design world, but his newfound design and fabrication expertise is all self-taught. One look at his Instagram page and you might question this statement—the parts there are beautiful and his welding work excellent, a skill he attributes to “sitting down and running endless weld beads.”

He’s also started working with a friend of his—Thomas Patterson—from Sacramento, California, Hogan’s home state. Patterson owns a marketing firm there named Weekend Digital. Between the two of them, Hogan plans to expand the E-commerce business into lifestyle products carrying the de stijl brand. He also plans to continue his relationship with SendCutSend for laser cutting metal, who he says has been “insanely helpful” throughout his steep learning curve, and are “a super friendly, amazing group of people willing to go above and beyond” in terms of customer service and support.
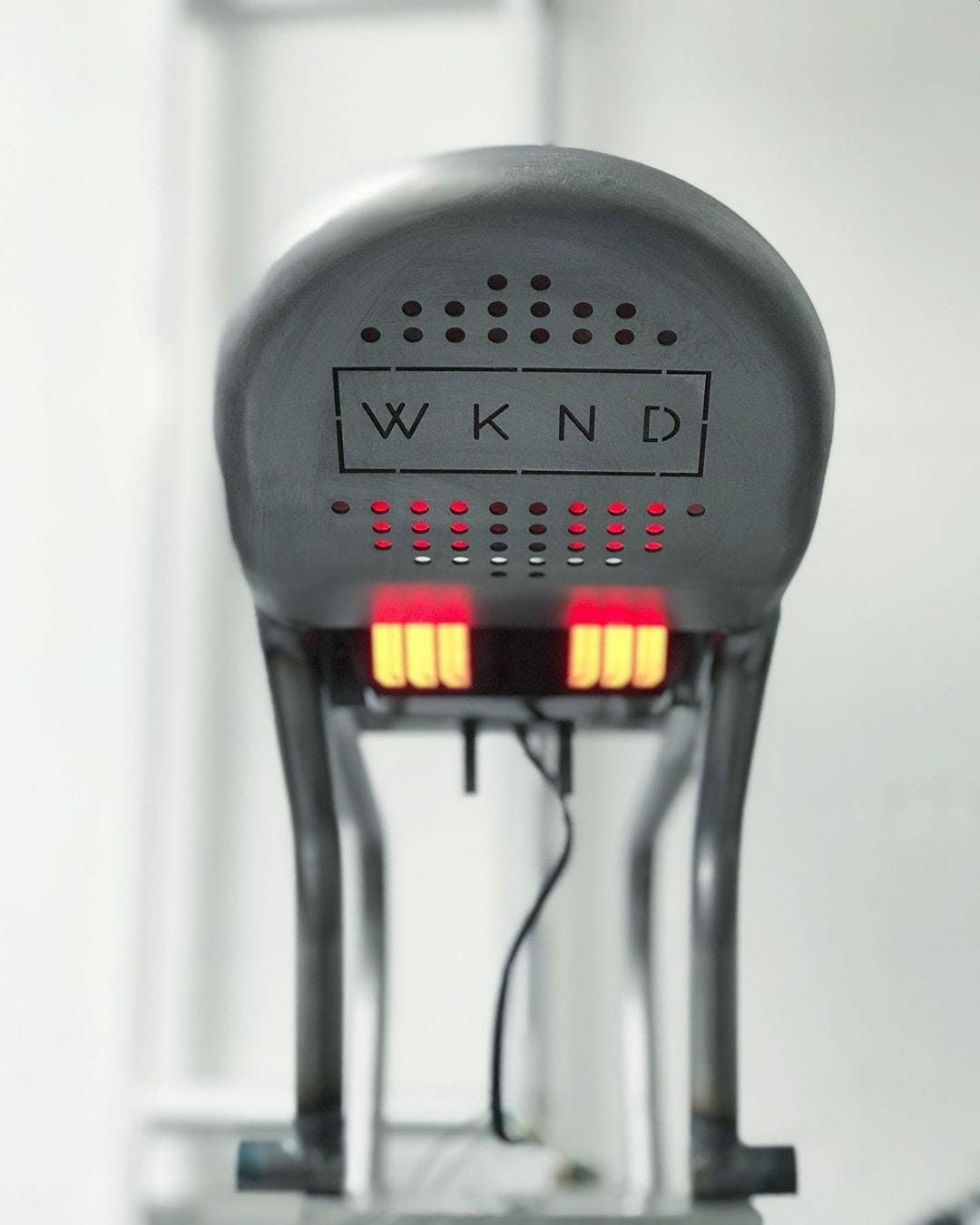
“My perspective is that you should try to do things the best you can, always,” said Hogan. “It has helped that I now have easy access to a supplier that allows me to experiment without risking a bunch of money. I think there are a lot of people out there like me who want to try things but don’t really know where to start. A quick-turn online laser cutting service like SendCutSend facilitates this sort of ‘figure-things-out-as-you-go’ kind of learning. Ideas become more attainable and barriers are removed, especially for regular people like me who might not have a lot of manufacturing experience but have the persistence and drive to push through and do amazing things. SendCutSend has helped me to do exactly that.”