When it comes to protecting your parts, SendCutSend has a variety of options to choose from. Powder coating, anodizing and zinc plating are all available services for your parts. In this article we’ll discuss plating and the benefits it can offer.
What is Zinc Plating?
Because plating is a general term that can describe a lot of different processes, let’s start with a little more details on exactly what we’re discussing here. In this case, we’re specifically talking about electrodeposition of a layer of zinc onto steel parts, followed by a chromate conversion coating to further protect the part. Still with me?
Basically, the process involves using electricity to deposit a very thin layer of zinc onto your steel parts. Technically, that part is now zinc plated, but an additional step of soaking the part in a chromate solution is used to give the zinc even more protection from corrosion.
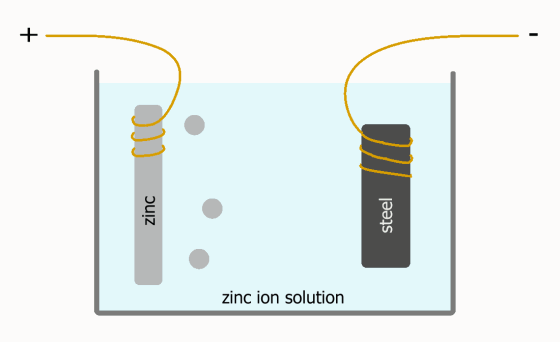
Why Bother Plating Parts?
Plating is a multistep process, so would you want to do that? There are multiple benefits to zinc plating, but by far the biggest reason for zinc plating is for corrosion protection. Steel parts that are left uncoated will corrode/rust over time, even from a small amount of humidity in the air. Zinc plating isn’t the only option for extending the life of steel parts, painting and powder coating are also great options. Zinc plating does have some distinct advantages we’ll cover here.
Colors Available
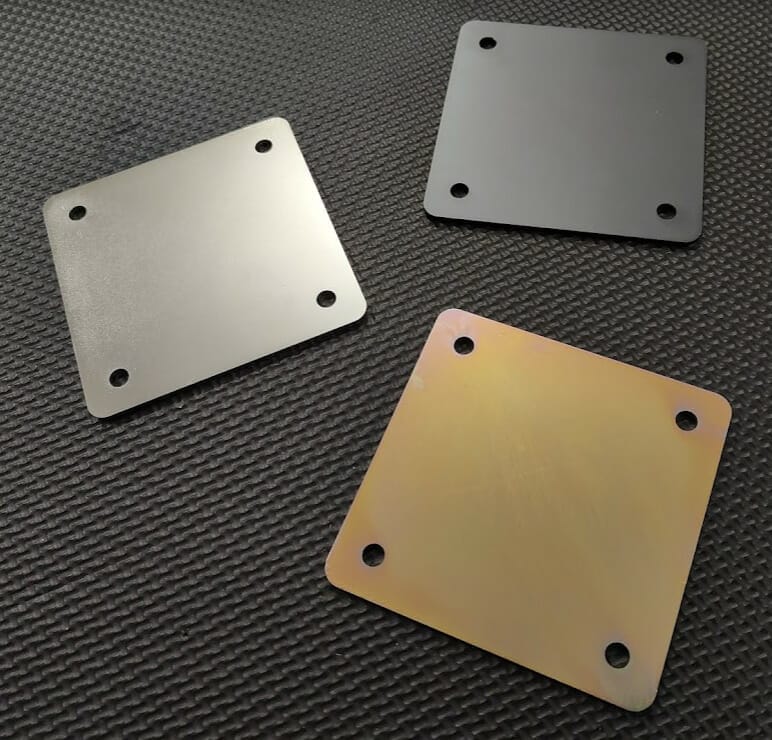
Here at SendCutSend we offer 3 different colors of zinc electroplating. You can choose from clear, black and yellow. In each case the zinc is the same, but the post treatment with chromate is slightly different. The color differences aren’t purely cosmetic, we’ll discuss the benefits of each later in this article.
Benefits
Protection from Corrosion
As we mentioned above, protection from corrosion is the single biggest reason zinc plating exists. When exposed to oxygen in the air, the iron in the steel will start to react forming iron oxide, also known as rust. Where painting and powder coating can also be used to protect steel from corrosion by sealing it off from moisture/oxygen in the environment, zinc plating goes even further. A zinc layer will also seal the steel base material from moisture and oxygen, preventing it from reaching the steel in the first place, but what about when that protective layer is broken?
When a steel part is painted or powder coated, and that layer is scratched or chipped exposing the steel to moisture, the exposed steel will begin to rust. That corrosion will continue underneath the protective paint/powder layer, destroying the steel and causing the paint or powder to flake off. Zinc on the other hand behaves slightly differently. Zinc has the benefit of behaving in a sacrificial manner. The nearby zinc, next to the exposed steel, will react with the elements instead of the steel. This reduces the speed that the steel will rust, effectively extending the life of the part.
Because the zinc is so “willing” to react with the environment, if left as is, it would quickly sacrifice itself completely and leave the steel exposed. For this reason an additional step in the plating process is commonly performed. This is the chromate conversion we’ve mentioned previously. The chromate basically makes the exposed surface of the zinc significantly less reactive. Giving the zinc its own protective shell. So, the steel is protected and the outer surface of the zinc is protected.
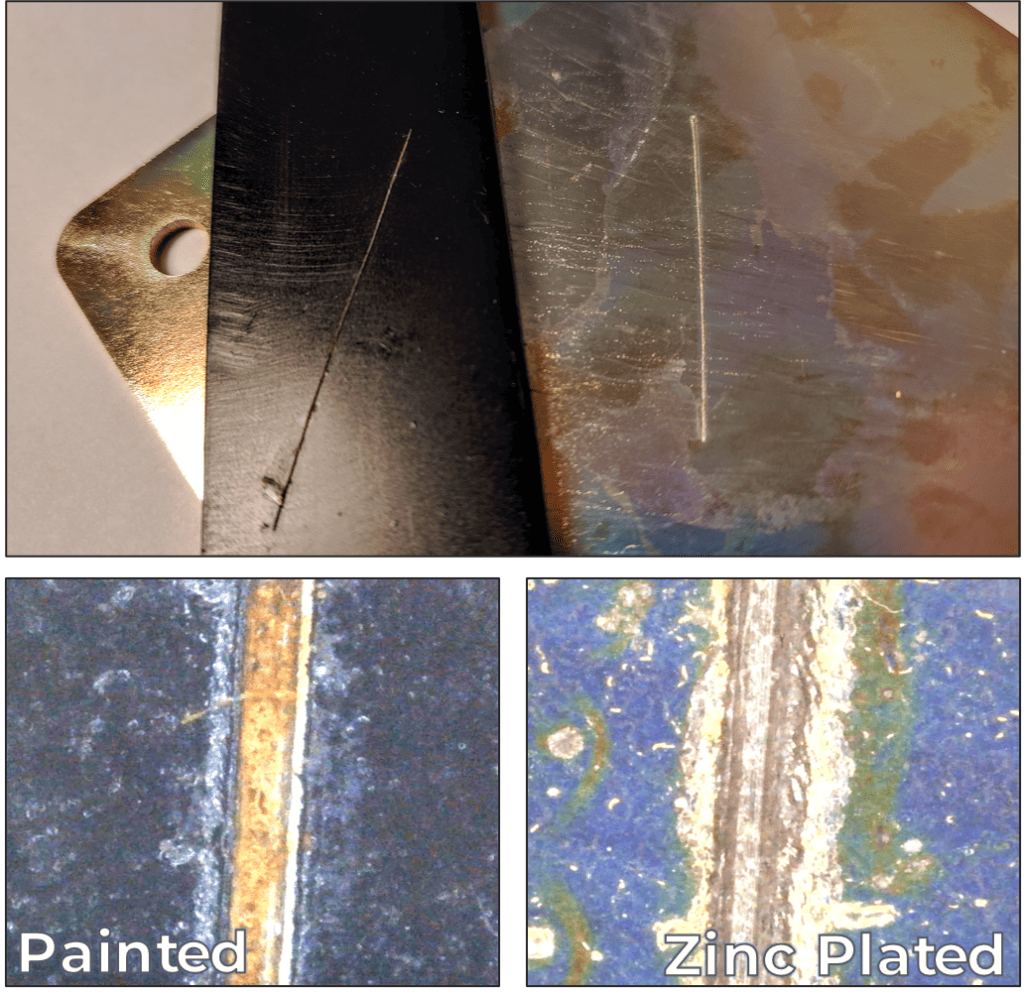
In the image above you can see an example of two steel parts, one painted and one zinc plated, both with a deep scratch. Both parts were exposed to identical environmental conditions (humid air) for the same amount of time. A close look at the scratch shows the painted part has rust forming on the exposed steel after only a short time. The exposed steel on the zinc plated part however is still relatively clean and rust free.
If left this way for a longer period of time, the rust on the painted part would eventually work its way along the surface of the steel underneath the paint, causing the paint to flake off.
Zinc Plating as a Base for Paint
If you want to take the level of protection on your parts even further, zinc plating makes an excellent surface for paint. Painting over a zinc plated part provides one more layer to prevent your steel parts from corrosion. With the zinc underneath, even if the paint is scratched, the zinc can still do its job protecting nearby exposed steel, buying your part more time before corrosion becomes a bigger issue.
This is one of the reasons cars are able to resist rusting better than they used to. Automakers have recently started applying zinc to the steel body panels before painting to extend the life of the thin sheet metal.
SendCutSend doesn’t currently offer both zinc plating and powder coating on the same part, but you can order your parts zinc plated from us and paint them on your own for that extra layer of protection.
Clean Parts
While we’re still on the topic of corrosion protection, it’s worth noting that part of the electroplating process involves a thorough cleaning of the parts. We’re not talking a soap and water scrub, but typically the parts are degreased and often soaked in acid to etch the base material. This has the benefit of providing an excellent surface for the zinc to hold onto, but also makes sure there isn’t any rust underneath the coating.
Zinc Plating is an Inexpensive Option
Compared to some other options, zinc plating is relatively inexpensive. Zinc itself is typically not a very expensive material, and the process of electroplating can often be done on large batches of parts at once. As opposed to painting or powder coating which commonly require individual parts and surfaces to be sprayed.
Environmentally Friendly
Prior to using zinc it was common to use cadmium for plating. While it had some advantages over zinc, unfortunately, cadmium is highly toxic and not environmentally friendly. Cadmium plating is still used, but it’s much less common as more organizations switch over to alternatives. Zinc plating is one of those alternatives.
Thin Surface Layer
Because zinc is a sacrificial layer, giving itself up to corrosion to protect the base material, it can last much longer when it’s a thicker layer. The problem with having too thick a layer is that parts won’t fit together correctly. This is one reason zinc plating is so widely used on fasteners. Typical thicknesses for zinc plating are around .0002” vs something like powder coat which is significantly thicker. You won’t find any powder coated bolts.
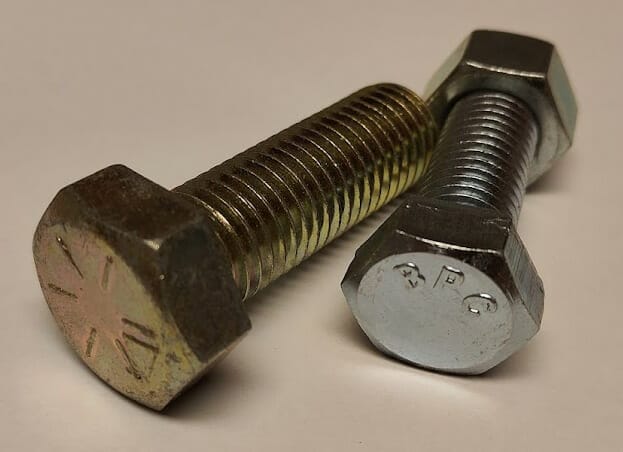
You may have seen parts with thicker layers of zinc, like chain link fences for example. Those are typically hot dip galvanized, a different process than plating. Galvanized coatings can last longer than plated against corrosion due to their thickness.
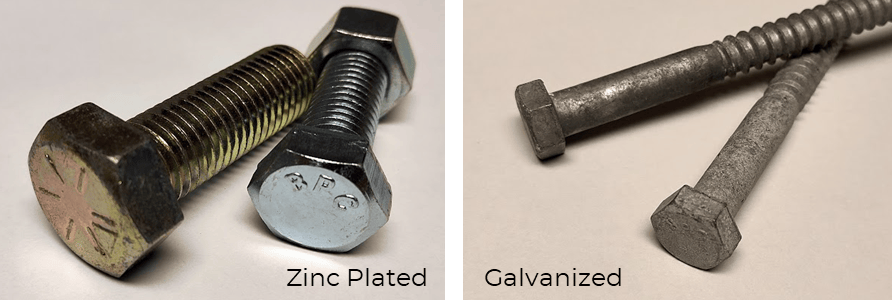
Color Differences
So, what’s the difference between the different colors of electroplated zinc? While there are other colors available, we’ll cover the functional differences between the three options available from SendCutSend.
Clear
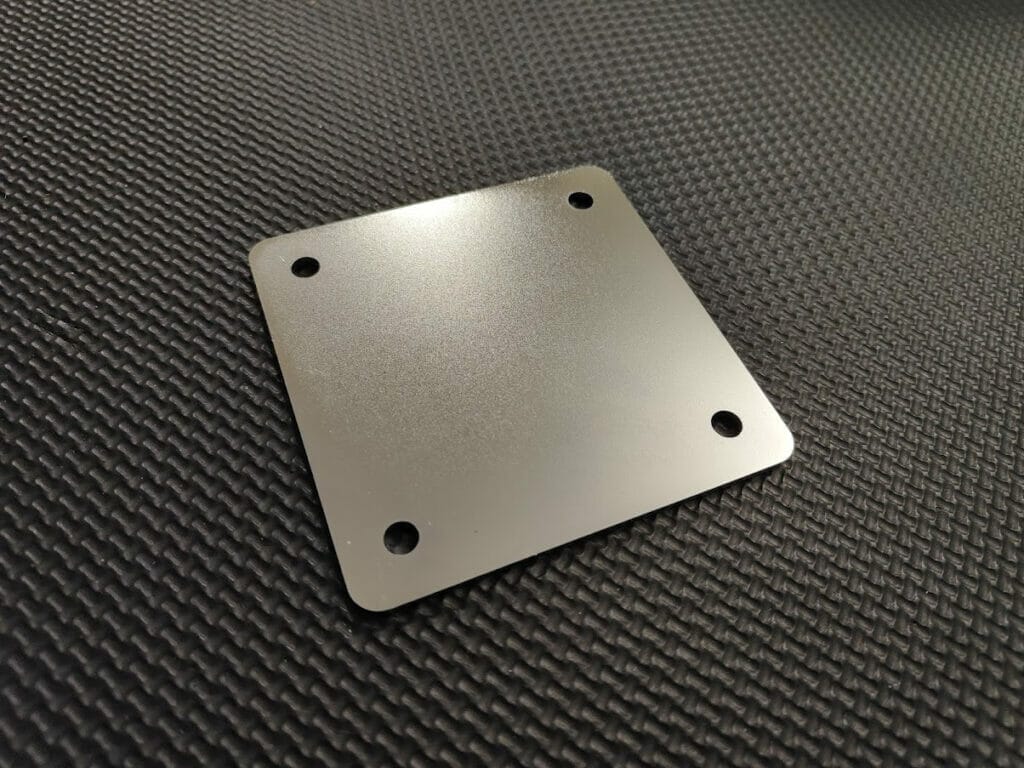
Clear zinc plating uses a chromate conversion coating that is mostly colorless. Like the other colors, it still converts the surface of the zinc to be much less reactive. Of the three options, clear will offer the least protection. It is also slightly more environmentally friendly than the other options.
Black
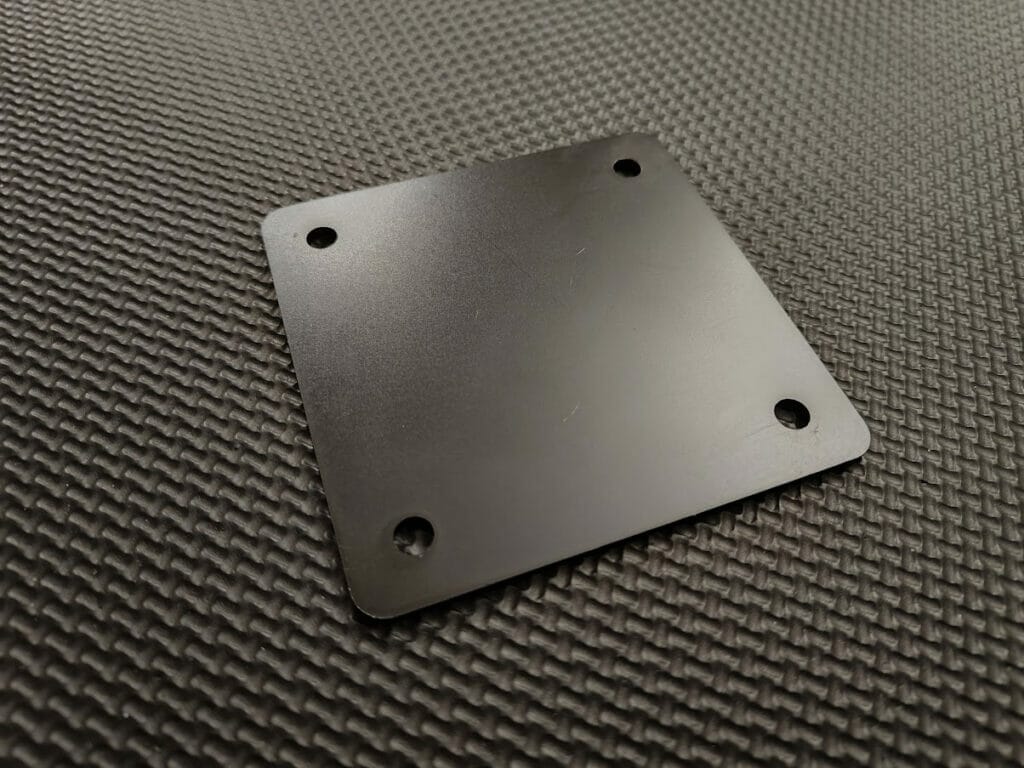
Black zinc plating uses a black chromate coating after plating. The final product is black, but may also have streaks of other colors. It’s not something you’d want to use if you’re looking for a solid black color or expecting a paint-like finish. The black zinc plating does offer greater protection over the clear, so your parts should last slightly longer before corrosion is an issue.
Yellow
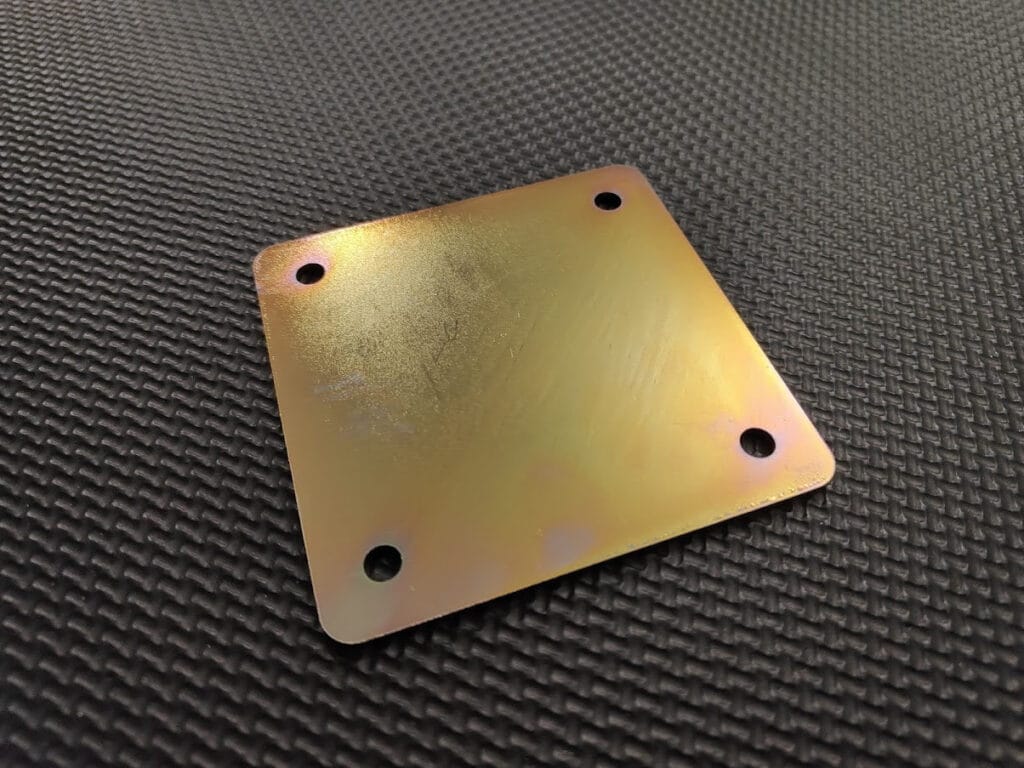
Yellow zinc plating is often an iridescent golden-yellow color. It offers the most protection, although black is not far behind.
When To Avoid Zinc Plating
Zinc electroplating has lots of benefits, but there are some things to be aware of when ordering plated parts.
Increases corrosion resistance, but not forever
Nothing lasts forever. There’s no finish you can apply to a part that will make it resistant to corrosion forever without needing some sort of periodic maintenance. That said, zinc plating can last for years outside with no issues, decades in less harsh environments. Because of the way zinc protects, it may eventually need some kind of maintenance. Painting your plated parts will extend their life beyond what either paint or plating could do alone.
Welding
Zinc plated parts shouldn’t be welded. Welding over zinc can create toxic fumes. If a plated part needs to be welded, the plating should be removed from the areas being welded. It can be removed relatively easily with abrasives or even certain chemicals can strip it clean.
High Temps
Zinc plating can handle temperatures up to about 400-500 °F (204-260 °C), although it will be slightly less resistant to corrosion at temperatures below that (around 200 °F/93 °C). It should be able to handle most powder coat oven temps if you’re planning to powder coat over top of your zinc plated parts.
Marine/Seawater Environments
While zinc plating will definitely extend the life of a steel part in and around salt water, like all metals that suffer corrosion issues, it won’t last as long in a harsh environment like that. Again, painting over plated parts offers another layer of protection to extend service life. In many cases a better choice for marine parts may be certain grades of stainless steel.
Moving Components
Since zinc is a relatively soft material, it can be scraped off in areas where components slide against each other. Even just tightening a screw can scrape away some of the plating under the head. As mentioned previously, however, a damaged zinc layer still provides much better protection against corrosion than paint alone.
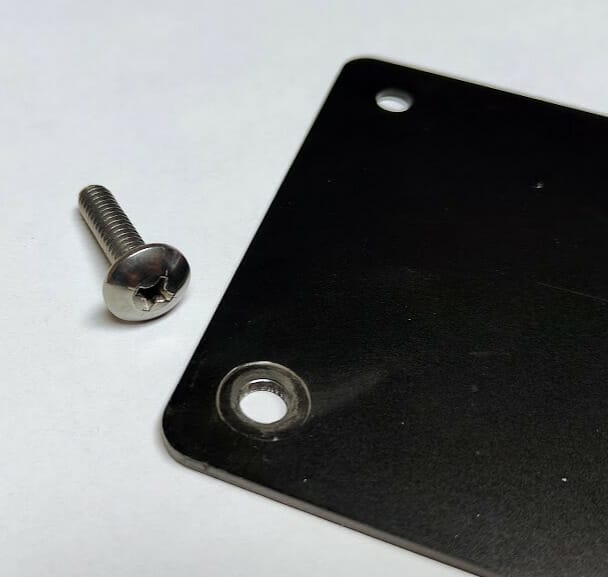
Summary
Zinc plating is an excellent way to protect steel parts from corrosion, especially when used as a base for paint or powder coat. It even provides a level of protection when it’s scratched and the bare steel is exposed. Something you won’t get with paint or powder alone. And because it’s an electroplating process, the zinc is bonded to the steel extremely well and won’t peel or flake off. Another trait that’s unfortunately common with poorly painted parts.
Zinc plating is one more option for protecting your laser cut steel parts. If your next project could benefit from zinc or any of the other finishing services we offer, SendCutSend is here to help! Check out our plating page for more details.