There are roughly twelve bajillion different ways of fastening your parts together so it’s not uncommon when two similar fasteners get confused with each other. Self-drilling screws and self-tapping screws, sometimes generally referred to by the brand name Tek screws, fall into that category. The terms often get used interchangeably, even though they are different fasteners.
Keep reading and we’ll dive into why these two screws are different and the best ways to use them in your projects.
Self-Drilling vs. Self-Tapping: What Are the Differences?
Self-drilling screws and self-tapping screws have a lot in common. They both come in multiple materials and finishes like stainless steel and galvanized steel. They can both create their own threads. They both come in a variety of heads and drive types. It’s no wonder they get confused for each other. So, what makes them different? The simple difference between them is that self-drilling screws can drill their own pilot hole and cut their own threads. Self-tapping screws can only cut their own threads. That’s it.
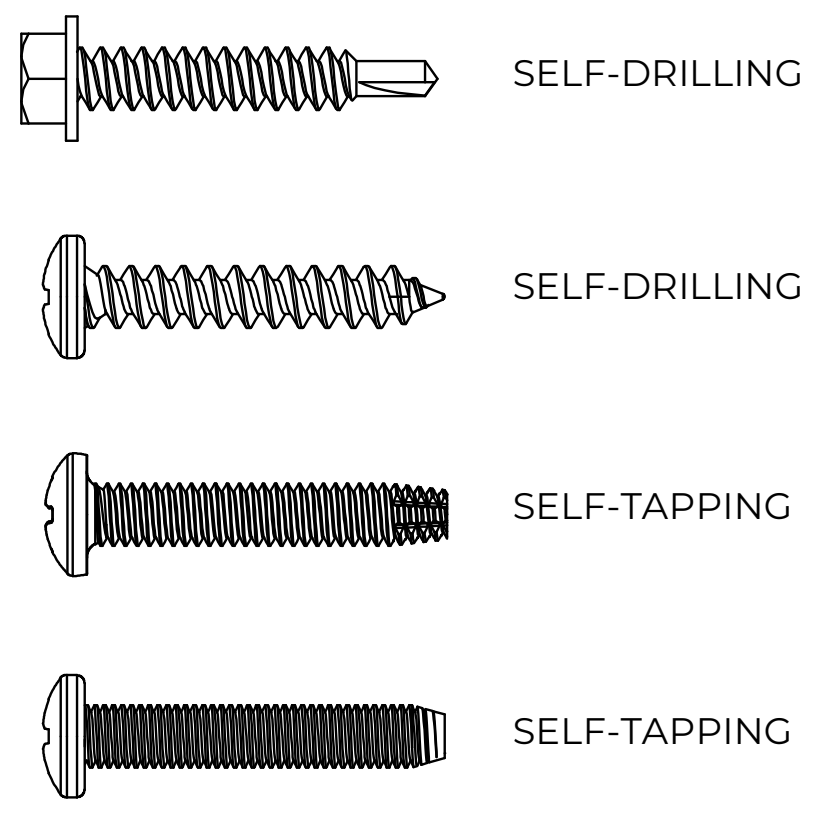
Why don’t we take a closer look at each.
Self-Tapping Screws
You can think of a self-tapping screw as a combination of a tap and a screw. The top shares all the features of a standard screw and the tip works like a tap. Some self-tapping screws will cut threads, they typically have flutes at the tip for clearing chips. There are also thread forming self-tapping screws which will create threads by deforming the material rather than cutting.
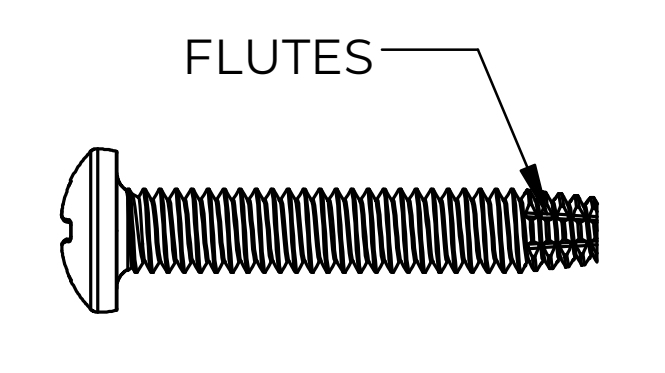
While a self-tapping screw can cut its own threads it does require a pilot hole. Similar to using a thread tap, an appropriately sized hole needs to be cut into the base material for the screw to start cutting threads. If your particular screw doesn’t include a pilot hole dimension you can usually look it up online. If your pilot hole is too small, you can actually damage or even break the screw trying to install it. If your pilot hole is too big the threads could be weak and strip easily.
Like most common fasteners, you can find a standard that governs the details. ANSI/ASME B18.6.4 for inch threads and B18.6.5 for metric threads are two standards for self-tapping screws. The specs you can find details on thread and point types, along with pilot hole sizes for different screw sizes.
How Should You Use Self-Tapping Screws?
Self-tapping screws can be a big time saver over standard machine screws. There’s no need to tap the hole before installing the screw. In a production environment where time is money, those savings can add up.
They can be used in nearly any material, soft and hard woods, plastics, even metals like aluminum and steel. With harder materials like steel, self-tapping screws work better in thinner materials, but they can still be used in thicker applications.
While self-tapping screws do cut threads, they should be reserved for applications that don’t get disassembled often. If you need a fastener that can be disassembled and reassembled, a traditionally tapped hole will provide higher quality results. Because a self-tapping screw is designed to cut or form threads it’s easy to damage existing threads when installing.
Self-Drilling Screws
A self-drilling screw is nearly identical in every way to a self-tapping screw with the addition of a tip that’s more like a drill than a tap. The tip of a self-drilling screw is designed to drill the right sized pilot hole for the rest of the screw to cut threads. That means they don’t require a pilot hole at all.
In harder materials the drilling portion of the screw needs to be fully through the material before the threads start to engage, so there are some limitations to using them. They shouldn’t be used in blind holes, but can be purchased with different tips for different thicknesses of material. For thicker materials, tips with a numbered drill point can allow them to be used in steels up to ½” thick.
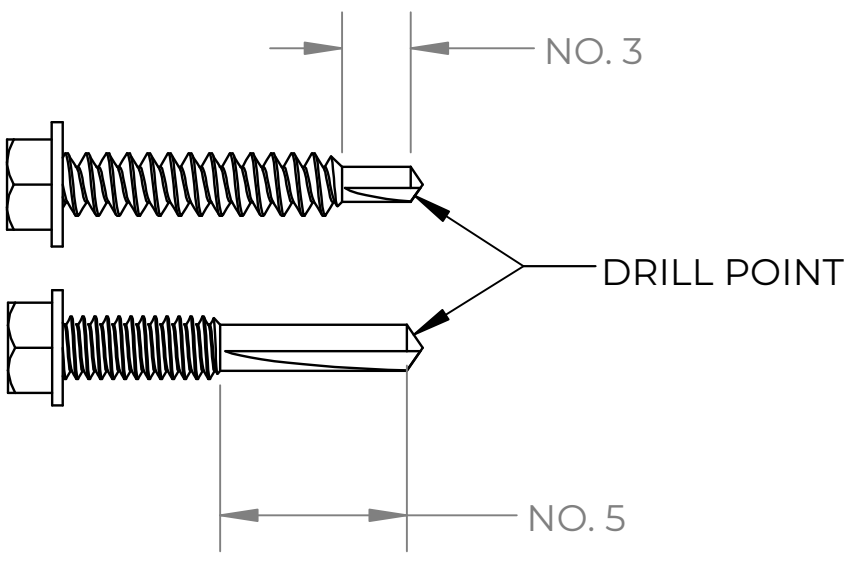
How Should You Use Self-Drilling Screws?
Self-drilling screws share a lot of the same applications as self-tappers. Similar to self-tapping screws, self-drilling screws are a big time saver. In the right applications, they’ll save even more time than self-tappers because no pilot hole is required.
Again, just like their self-tapping cousins, they work well in a variety of materials. The biggest limitation is material thickness, but that typically only applies to harder materials like metals. In plastics and woods, there are types of self-drilling screws that can be used in any thickness. The material just needs to be soft enough that the screw can drill through it as quickly as the thread pitch drives it. Too hard and the screw can’t drill quickly enough and the threads can be stripped.
Self-drilling screws are often used in general construction to secure sheet metal to other materials. They’re also a great option when drilling a pilot hole is difficult or inconvenient as they don’t require hole alignment. Sheet metal HVAC ducts are a great example.
Self-drilling screws with sealing washers are common. They make installing roofing panels (fiberglass, plastic, sheet metal) quick and efficient.
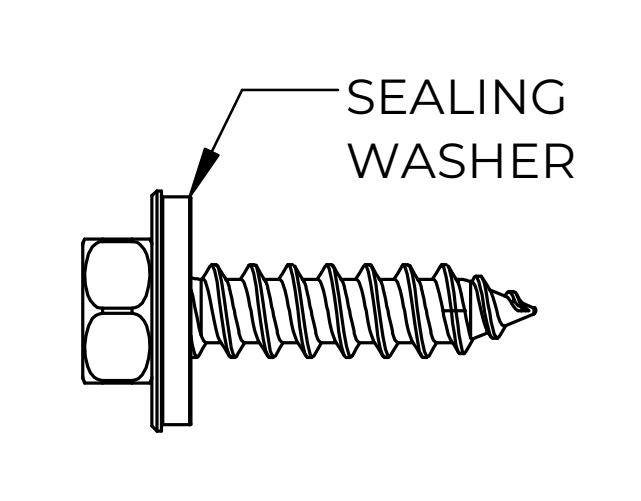
Yet again, similar precautions should be taken with self-drilling screws, maybe even more so than with self-tappers. Not only are they designed to cut or form threads, but some styles with a drill point tip also drill through material. Disassembling and reinstalling can damage existing threads if you’re not careful.
Mastering Metal Screwing: SendCutSend’s Expert Countersinking Solutions
Both self-drilling and self-tapping screws come in a range of head styles, including flat heads for countersunk holes. Using countersunk screws has the benefit of a flush finished appearance. You can order your parts from SendCutSend with countersunk holes, saving you an additional step. Combine that with the time savings you get from self-tapping screws and you can cut your assembly time dramatically.
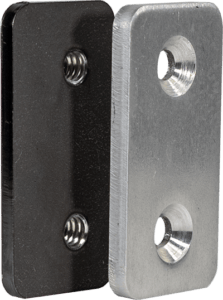
Alternatively, if you’re after the highest quality parts, you may want to use a standard tapped hole and screw in place of a self-tapping screw. Once again, SendCutSend has you covered. We can both tap holes or install hardware for you.
Whether you need quick and efficient parts or top quality parts, SendCutSend has all the services to support your project.
FAQs about Self-Drilling and Self-Tapping Screws
Can you use self-tapping screws in wood?
Yep. While specific taps for wood do exist to allow you to use a standard machine screw, they work best in hardwoods. Most wood screws are self-tapping. Self-drilling also, but sometimes pre-drilling a pilot hole is a good idea especially near the edge where splitting the wood is more likely to occur.
What is the advantage of self-drilling screws over self-tapping screws?
Self-drilling screws don’t require a pilot hole, saving you time and tools. You don’t need to know the right size for the pilot hole, so the threads should be sufficiently strong every time.
Are there different tip styles for self-tapping and self-drilling screws?
There are a ton of them actually. Here are just a few:
- Type A has a pointed tip and coarse threads
- Type AB has a pointed tip and fine threads
- Type B has a blunt tip
- Type F has flutes and a tapered tip
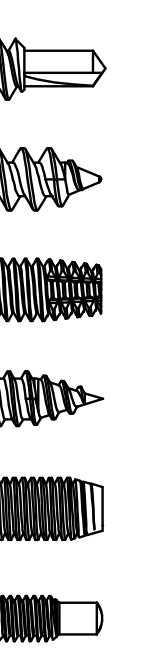
There are cone shaped tips, cylindrical shaped tips, pointed tips to help with alignment between panels, sharp points for piercing thin materials. There are drill point tips in different sizes for different thicknesses. Way more than we can cover here.
How can I keep a self-drilling screw from slipping instead of drilling?
While self-drilling screws don’t require a pilot hole, it can be helpful to use a center punch to create a small divot to start the screw. The same as you would a standard drill bit to keep it from walking off center.
Can I disassemble parts that use self-tapping screws?
You can, but we wouldn’t recommend it repeatedly. Even though some self-tapping screws use standard machine screw thread sizes, they don’t always cut or form threads well. The more you remove and install them, the more likely the threads are to wear out.
Where can I find self-tapping and self-drilling screws?
They’re very common. Almost anywhere that sells fasteners will carry them. They may be called by different names like Tek screws, sheet metal screws, thread-cutting or simply tapping or drilling screws.