SendCutSend is the premier supplier for laser cutting, CNC routing, and waterjet cutting. No matter your need, we have the means to get the job done. But not every job is the same. Material selection, size, tolerance, post processing needs, and more are all considered when choosing the best fabrication method to make a given part.
Each cutting process has its own advantages and challenges. Where one cutting method falls short, another offers a solution. At SendCutSend, we choose the ideal method for cutting each of our available materials so your parts will be produced using the best process at the most affordable price. This means that your material choice should factor in while you’re designing your parts.
This article will explore our full arsenal of 2D manufacturing methods and take a deep dive into each one.
CNC vs. Laser vs. Waterjet Cutting
CNC, laser, and waterjet cutting are distinct manufacturing processes with differences in cutting method, materials, precision, heat effects, and cost.
CNC cutting utilizes computer control for cutting tasks, suitable for metals, plastics, and wood. Designs programmed into the CNC machine direct the router to cut or carve material with exact velocity and positioning. It is very precise but may generate heat.
Laser cutting employs a high-powered laser for precise cuts across a range of materials, with minimal heat-affected zones, making it ideal for intricate designs. It excels in precision and minimizes heat effects especially in detailed designs with small features.
Waterjet cutting utilizes a high-pressure stream of water mixed with abrasives, offering versatility in cutting materials without heat, suitable for metals, glass, and composites. The choice among these methods depends on factors like material type, desired precision, and budget considerations, catering to diverse applications in manufacturing and fabrication industries.
Laser Cutting
As the name suggests, laser cutting is the process of using a laser to make two-dimensional cuts into stock material. A laser is a very fine amplified light beam that melts, burns, and even vaporizes through work material along a preprogrammed path, making a highly accurate cut.
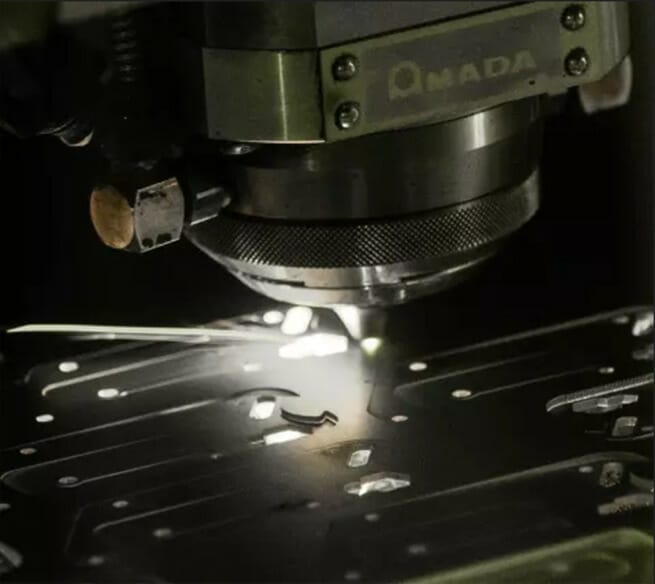
Capable of cutting upwards of 2,500 inches per minute, laser cutting is the fastest method available, and often the most economical. Our high-powered fiber lasers range from 4kW to 12kW and are accompanied by a fleet of low-powered CO2 lasers. Highly accurate cuts with tight tolerances are the norm with laser cutting, and you can find the specific cut method and tolerance on the individual information pages in our materials directory
Kerf and HAZ in Laser Cutting
During cutting, some additional material is burned away. The width of the laser beam + the amount of material burned away is called the “kerf”. There is no need to compensate for the kerf because we take care of that for you. But do note, small and intricate details will get lost in the kerf, so it is best to keep designs simple. Here are some tips on setting up your design for single line etching or single line “no kerf” through cuts.
Keep in mind, all holes and cutouts must be approximately 30% (or greater) of the material thickness. The exact hole and bridge/webbing minimums for each stock thickness are listed on the material spec pages here.
Because laser cutting is a thermal process, the adjacent area next to a cut that is not burned away can have its material properties altered slightly. This is known as the heat-affected zone, or HAZ, and is generally undesirable. Since it is not our friend, here’s how to avoid HAZ. Fortunately, due to the incredibly fast cutting speed, advanced, proprietary software, and small beam diameter of our lasers, the heat transferred to the work material is drastically minimized. For simple geometries, HAZ is virtually nonexistent.
Best Materials for Online Laser Cutting
Metals like aluminum, mild steel, stainless steel, copper, brass, and more can be laser cut. Most metals up to ½”. Don’t forget to check out our material thickness maximum and minimum chart, as well as our processing size limitations.
We’ll cut just about anything but we don’t laser cut materials that create hazardous gasses when burned, such as PVC plastic. Flammable materials are also not well suited, such as thick plywood.
What to Expect with Laser Cutting
Laser cutting causes small striations and slightly abrasive edges on materials over 0.187” in thickness. In addition, dross (resolidified molten material that is not fully ejected from the kerf during a cut) can leave blobs near the cut edge. However, our deburring process is included for applicable materials at no cost, because we want you to have good looking parts when they arrive at your door.
Laser cutting is often the quickest and most affordable option for a large variety of materials. When laser cutting isn’t the ideal cutting solution for a given material or project, we have our CNC router and waterjet cutting services.
CNC Routing
Our CNC routers move the same way that our lasers do: they follow a path created by your designs/CAD files.
A cutter is rotated in a spindle that lowers to plunge into the work material. The cutter is then moved along preprogrammed paths to make simple two-dimensional cuts. Imagine a much more industrial hand router that is mounted and moved around with computer-like precision.
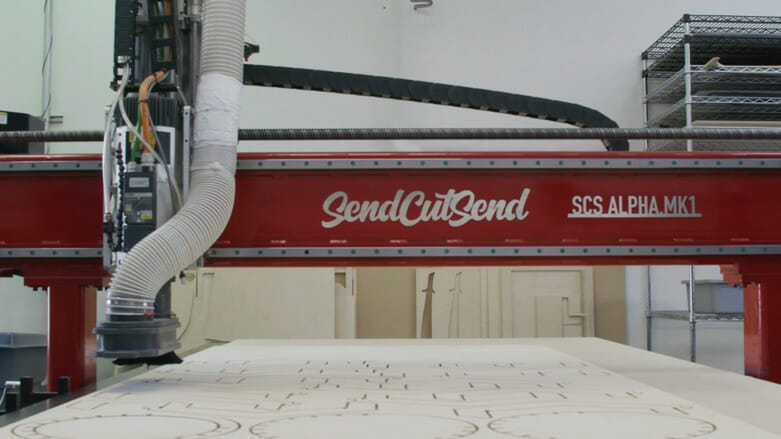
CNC routing has an advantage over laser cutting for many composites, plastics, and woods. Routing will leave a superior surface finish while maintaining a tolerance of +/- 0.005”.
The “speeds and feeds” for a CNC router are adjusted for different materials and thicknesses. The feed rate is the speed the cutter moves through the material, measured in inches per minute (IPM). The surface speed is the speed the cutting edge of the cutter sees, measured in surface feet per minute (SFM). The surface speed determines the spindle speed, measured in revolutions per minute (RPM), or the other way around. We’ve dialed in our speeds and feeds for each one of our materials to get the best surface finish while taking the fastest possible cut.
What to Expect with CNC Routing
Like laser cutting, the router’s cutter displaces material as it cuts, also known as kerf. Our software compensates for the kerf along every path, so you don’t have to worry about it.
Unlike laser cutting, there is a load on the parts during machining. Small fixture tabs are added onto parts to keep them from moving around during cutting. This ensures part quality but might leave a small bump on the edge of the part. (This is also the case with laser cut parts, but the tabs are smaller).
Tabs are about 0.1875” wide, with a depth that is half of the material thickness. Placement is dependent upon the part’s geometry. We remove most of the tab before shipping, but a hand finishing may still be needed.

Parts with large amounts of material removal have a high risk of moving during cutting. For example, grill, grates, and perforated patterns are not ideal for CNC routing, and can be rejected. We recommend no more than 50% material removal.
Because the inner corners of a CNC routed part cannot be sharper than the diameter of our cutter (we only use ⅛” bits), all interior edges must have a radius of 0.063” or larger. Also note, only two-dimensional cuts are possible. No threading, countersinks, 3D contour, V grooves, partial depth cuts, or double-sided cuts.
Additional Services Available for CNC Routed Parts
At SendCutSend we offer tapping and countersinking for some CNC cut materials like ABS and HDPE after they are cut. Check out our tapping and countersinking guidelines pages to see which materials are eligible for these services.

Note, that when assembling CNC routed parts, an additional radius on a corner can cause interference. A square part will not fit into a mating hole if there are radii on the corners. A dogbone filet can be used to ensure a high tolerance and snug fit. Our CNC guidelines have more details and tips on CNC routing.
Whether for one part or thousands of parts, CNC routing offers a robust solution for materials that are not suitable for a laser. However, some composite materials still present challenges. For these, we look to waterjet cutting.
Waterjet Cutting
Waterjet cutting is the process of using extremely high-pressure water, concentrated into a small jet, to cut through stock material. Finely crushed garnet is mixed into the water flow to act as an abrasive. A nozzle travels along a preprogrammed path to make high-quality cuts.

The water pressure, cutting speed, and abrasive garnet produce an incredibly high-quality surface finish along the cut edge. The waterjet and garnet abrade the working material. Unlike CNC routing and laser cutting, dross and burrs are eliminated. Our water jet cutting has a tolerance of +/- 0.009”.
The Best Materials for Waterjet Cutting
Difficult-to-process composite materials, such as carbon fiber, G10, and phenolic, are ideal material candidates for waterjet cutting. Other cutting processes can lead to excessively rough edges and/or delamination with these materials. Additionally, any potential HAZ is eliminated with waterjet cutting.
Like CNC routing, interior corners must have a radius to accommodate the size of the waterjet stream. Interior corners must have a radius of 0.032” or larger. Therefore, no holes can be smaller than 0.070” in diameter.
Waterjet cutting has historically only been available to large manufacturers. Aerospace suppliers often use waterjets to cut down large billets of aluminum, steel, and even titanium to save machine time on other CNC machines. Waterjet in particular is attractive to aerospace due to high regulations eliminating any and all heat affected zones on aircraft parts.
So which is better, waterjet cut or laser cut? Waterjet cutting is significantly slower than laser cutting and CNC routing but is the best choice for difficult to process composite materials. Check out our waterjet guidelines for more information.
Choosing the Cutting Edge
Custom CNC, laser, and waterjet cutting are only the beginning. Other services offered by SendCutSend include countersinking, hardware insertion, tapping, bending, and finishing.
You can also get quick and instant pricing by taking advantage of the parts builder, SendCutSend design services, or custom quotes for projects with unique needs or requirements.