Electroplating has been a critical surface finishing process since the 1800s, and it’s still widely used today to enhance and protect sheet metal parts across industries. By depositing a thin layer of metal onto a substrate through electrodeposition, electroplating can boost strength, improve corrosion resistance, modify conductivity, and refine appearance—all without compromising the base material’s mechanical properties. In this article, we’ll cover:
- How electroplating compares to powder coating and anodizing
- The science behind electroplating
- Practical benefits for sheet metal applications
- Tank vs. brush plating methods
- Material options like zinc, nickel, and chrome
The Science Behind Electroplating
Electroplating offers users a plethora of benefits, so it is important to understand the process. As mentioned, a layer of metal is deposited on a material. This electrodeposition is fueled through applying an electrical current. The material that is to be plated is negatively charged, becoming the cathode, and is dipped into a tank of conductive liquid referred to as the electrolyte solution. The metal used for plating is also put into the tanks and positively charged, becoming the anode. This completes the circuit and allows metal atoms to move from the anode to the cathode, thus creating a metal layer.
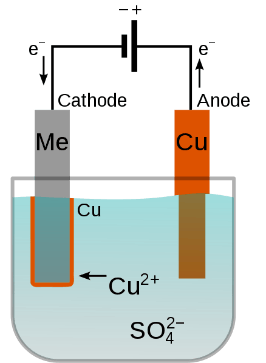
Figure 1: Electroplating Process: Image Source
For electroplating, there are many variables that can be adjusted to ensure a successful plate. These can include the current density, surface preparation of your specimen, solution concentration and presence of impurities, and other conditions. For both plating projects done by individuals and suppliers, it is important to have a prepared setup.
The benefits of electroplating in sheet metal?
For many industries, electroplating provides a wide range of benefits:
Increased Strength
By depositing a layer of metal with high tensile strength like nickel or chromium onto a weaker material, the overall structural integrity of the component is enhanced. This added layer can increase resistance to mechanical wear and tear, making the plated item more robust and less susceptible to damage.
Increased product lifespan
The plated metal layer acts as a protective barrier, shielding the underlying material from environmental factors that can cause degradation. Electroplating with a metal like zinc can prevent oxidation, while coatings like nickel or chromium can protect against physical abrasion as previously mentioned. This protective layer reduces the need for frequent replacements, prolonging the life of the component.
Altered Surface Appearance
Electroplating significantly enhances the aesthetic appeal of products, creating a smooth, shiny, and attractive finish through a thin layer of metal plating. This process allows for a high degree of customization, offering various colors and textures to meet specific design preferences. Additionally, metals used in electroplating are often resistant to tarnishing and staining, ensuring that items like jewelry and watches retain their luster over time. By improving the appearance of underlying materials, electroplating enables the use of cost-effective base metals while producing visually appealing and durable final products.
Corrosion Resistance
Electroplating creates a corrosion-resistant barrier on the surface of the substrate. Metals like zinc, nickel, and chromium are commonly used for their excellent anti-corrosive properties. Zinc electroplating is widely used to protect steel parts from rusting, for example. This protective layer prevents corrosive elements such as moisture and oxygen from reaching the base material, thereby preventing rust and corrosion and ensuring the component remains functional in harsh environments. Additionally, zinc is an excellent material to paint over, allowing for further protection.
Modifying Conductivity
High electrical conductivity is crucial for many industries, such as the electronics industry. Electroplating with metals like gold, silver, and copper can significantly enhance the conductivity of a component. Gold and silver are known for their excellent electrical properties and are often used in plating connectors, switches, and circuit boards. This improved conductivity ensures efficient electrical flow, reducing energy losses and enhancing the performance of electronic devices.
While each product’s need is different, electroplating can be a method to achieve desired targets. The iconic chrome of the automotive industry or the plated fasteners of aviation have electroplating being utilized. To achieve this, the two most common methods of electroplating are tank plating and brush plating.
Electroplating Techniques
Tank and brush plating make up the most popular methods of electroplating, each with their own respective use-cases. Tank plating utilizes large containers of electrolyte solution to plate larger surface areas. Brush plating is more selective – a brush, such as a steel body that is covered in a protective barrier, is dipped in electrolyte solution and is used in select areas. Brush plating does require the use of a skilled operator but has the benefit of more precise plating. Both techniques follow a similar approach of having a surface prepared and then plated.
In both instances, electroplating requires careful handling, storage, and use of chemicals. Inadequate ventilation and mishandling of electroplating chemicals can cause severe injuries, leading to long-term effects. In addition to health concerns, electroplating utilizing poor surface preparation, inaccurate electrical parameters, and materials mismatch can lead to poor quality plating. Uneven plating thickness, flaking, and discoloration are just a few of many results from poor electroplating. As a result, electroplating is commonly performed by suppliers who are experts in the process and can produce high-quality surfaces.
SendCutSend provides both zinc and nickel plating to make the process stream-lined and remove any complications from attempting the plating. Guidelines and instant pricing are available to ease the process!
Material Selection
Electroplating can be overwhelming at first with the sheer number of choices it provides. Below is a table that offers some reasoning for common plating materials.
Material | Reason for Selection |
Zinc | Corrosion resistance, prevention of rust, enhanced paint adhesion, cost-effective. |
Nickel | Hardness, wear resistance, improved appearance, corrosion resistance. |
Chrome | High durability, aesthetic appeal, corrosion and tarnish resistance, ease of cleaning. |
Gold | Excellent electrical conductivity, corrosion resistance, tarnish resistance, decorative finish. |
Silver | High electrical conductivity, thermal conductivity, antimicrobial properties, decorative finish. |
Copper | Excellent electrical conductivity, foundation layer for other plating processes, improved adhesion. |
Electroplating Versus Other Finishing Processes
To best understand if electroplating is the right decision for a part, a comparison to other methods is made. Powder coating involves applying a dry powder to a surface using an electrostatic charge and then curing it under heat to form a solid layer. Powder coating can provide for a wide range of finishing colors in a smooth appearance, while also providing corrosion resistance. However, the finish is much thicker than plating, and can prevent certain parts from fitting together. In general, power coating may be a more suitable approach when a thick coating that can withstand heavy wear and tear is needed, or if a non-metal object requires coating.
Another method is anodizing that produces an oxide finish on the surface of a sample. The sample is submerged in an electrolyte bath and current is run through the medium. Anodizing is most commonly used for aluminum and yields a durable, corrosion resistance surface. Anodizing should be avoided if there is additional processing still waiting the part, such as machining or welding which can damage the surface. Additionally, anodizing greatly decreases the conductivity of the sample. Electroplating thus comes into the fold in these situations.
Electroplating for Sheet Metal in a Nutshell
As discussed, electroplating can be a versatile process to greatly enhance designs. It is consistently used in industry, with certain products not being able to function without electroplating. While understanding if electroplating is the correct decision for a design can be daunting, SendCutSend makes it easy with a series of guidelines for designs. To get instant pricing on your design, upload your STEP or DXF file to sendcutsend.com.