Carbon fiber is a material renowned for its unique combination of strength, durability, and incredibly low weight. Being a composite, meaning made up from various components, carbon fiber has two main materials: a fabric like weave made from (yup, you guessed it) carbon fibers, and resin. Variations in the weave and resin can further tailor its characteristics. These two components come together to make a single material that is stronger than steel while being lighter than aluminum. Hence its high demand in such industries as aerospace and automotive where weight and strength are critical.
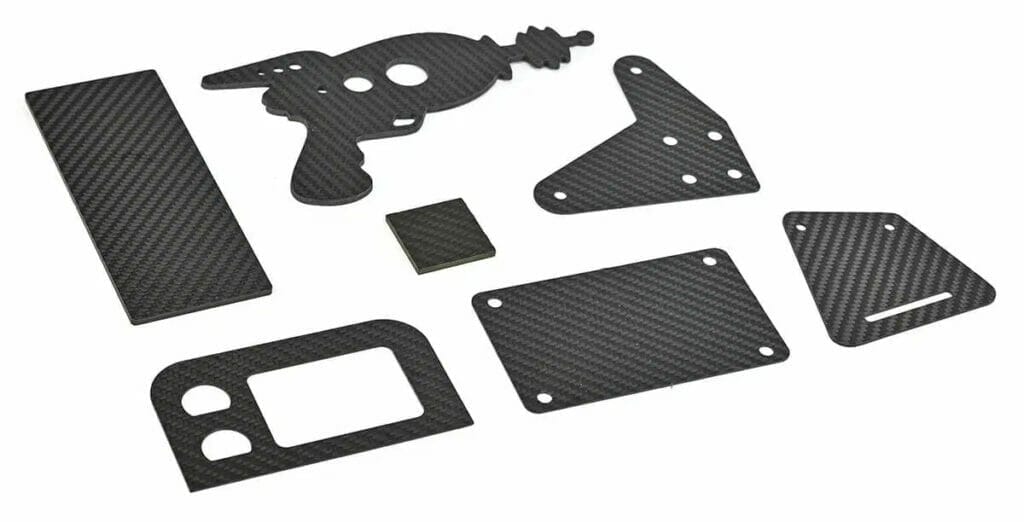
To get in the weeds (or weave in this case)…
Precursor fibers, such as rayon or polyacrylonitrile (PAN), undergo chemical and mechanical treatments to become high strength carbon fibers, or filaments. Several filaments are bundled together to make a thin band, known as a tow. Tows are rated by the amount of carbon fibers they contain. The more fibers, the stronger the tow. Standard ratings for tow include 3K, 6K, 9K, and 12K, with the “K” referring to thousands of filaments. Several thousands of super strong carbon fibers bundled together still only make up a fraction of an inch in width.
Individual tows are weaved together, similar to fabrics. A plain weave uses a straightforward over and under pattern to interlace tows, making a checkerboard like appearance. Although this is the simplest pattern, the short distance between the weaves can cause the tows to crimp. These crimps create stress concentrations and compromise the strength of the material over time.
A twill weave is the most common carbon fiber weave. Yes, the same twill weave used for clothing and furniture! Tows are interlaced to the right or left, passing over multiple tows, forming a distinct pattern of diagonal lines. A 2×2 twill weave will pass over two tows and then under two tows. As well as being aesthetically pleasing, this weave puts less stress on the individual tows and creates a stronger and more rigid final material.
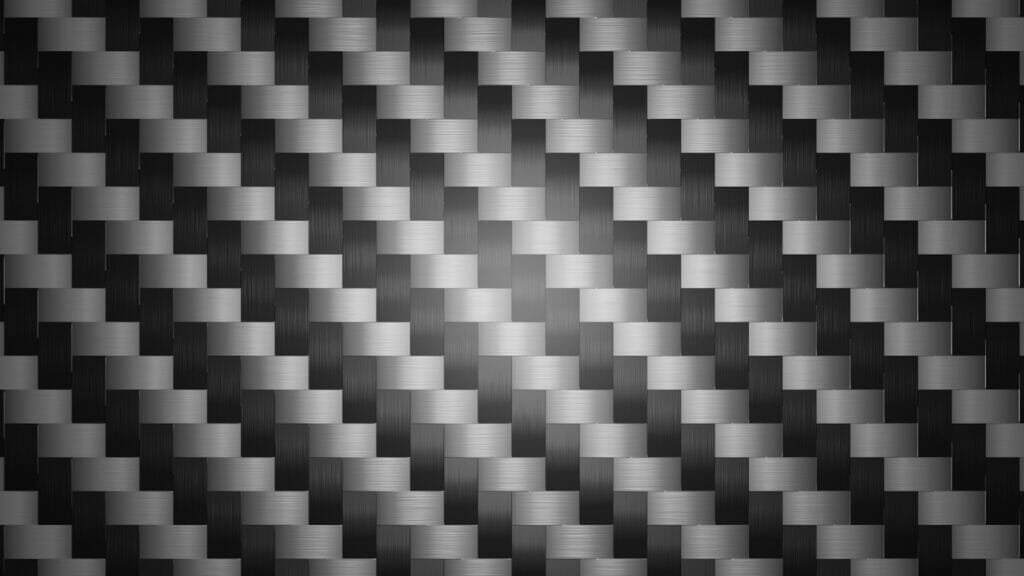
Being a staple in the aerospace and automotive industry, we choose to offer standard 2×2 twill weave carbon fiber for the marriage of tensile strength and rigidity which other weaves can’t provide.
A single sheet of woven carbon fiber is not very thick. Therefore, several sheets are stacked together. The more sheets, the thicker (and stronger) the final material. Sheets alternate between 0 and 90 degree rotations to give the final material the same strength in both directions.
To give the carbon fiber weave stiffness, resin is infused. The resin (like epoxy) chemically bonds and locks the carbon fiber into place. The resin transfers loads to the carbon fiber and secures the fibers while under pressure. The chemical bond made from the resin is stronger than most metals.
The carbon fiber weave and resin together is what deems this material as a composite. The benefit of the two components together is what gives this material its incredible strength to weight ratio. That’s how carbon fiber can be stronger than steel while being lighter than aluminum.
Carbon Fiber Specifications
Carbon fiber has some peculiar specifications that are not seen in metals and polymers due to its unique manufacturing process. Specifications can vary from different manufacturers and intended application, but below are some commonly considered attributes:
- Fiber Orientation and Weave Pattern: The arrangement of the carbon fiber within a sheet, such as the unidirectional, plain weave, twill weave, etc., affects the final strength and rigidity.
- Resin Content: Both the type and amount of resin can vary. For example, UV exposure, resistance to water, or temperature can determine the resin.
- Thickness: Carbon fiber is available in predefined thicknesses, with thicker sheets providing additional strength. We offer thicknesses of 0.40″, 0.63″, 0.70″, .118.” Check out our guide to choosing the best material thickness for your laser cut project.
- Surface Finish: Carbon fiber sheet can have a glossy or a matte finish. Ours has the same matte finish on the front and back sides.
- Modulus of Elasticity: A measurement of rigidity, determined by the ratio of stress to strain. A high modulus meaning a stiffer material, a low modulus meaning the material can easily be bent.
- Density: The weight of the material divided by its volume. Measured in grams per cubic centimeter (g/cm3) or pounds per cubic inch (lb/in3)
- Tensile Strength: The maximum amount of tensile (pulling) stress that a material can take before breaking. Measured in pounds per square inch (PSI) or megapascals (MPa).
We recommend reading the details and specifications on our carbon fiber material before starting your laser cutting project.
Making the Cut
Carbon fiber can be challenging to cut due to its high rigidity and low thermal conductivity. The fibers are naturally abrasive and can quickly wear out a typical cutter. High heats are generated while cutting and the material does not have the thermal conductivity to dissipate it. This too can prematurely wear the cutter, degrade the material, or even catch fire in some cases. The high stiffness makes the material brittle while machining, resulting in splinters, fractures, and chipping. Coupled with the tendency of fibers to fray, a machined surface is coarse and rough to the touch. Not to mention that carbon fiber dust is incredibly toxic.
Where CNC routing and laser cutting fall short, waterjet cutting provides a solution!
Waterjet cutting does not generate the high heat, which eliminates the possibility of thermal damage to the part. Because waterjet cutting uses a precise high-pressure stream of water, there are no costly cutters to frequently replace. Furthermore, the waterjet stream abrades away the material, resulting in a much better surface finish. No toxic dust is produced, which makes it safer for everyone.
For the reasons described above, we do not offer additional services for this material, such as countersinking, tapping, and deburring. However, waterjet cutting delivers superior edge quality, with no need for deburring. The incredibly high stiffness does not make it a candidate for bending or forming. Because the anodizing process requires a material to be an electrically conductive metal, carbon fiber cannot be anodized. Furthermore, plating and powder coating is not offered.
The Pros
Carbon fiber has some serious advantages that are unrivaled by other materials. Here are just a few to mention:
- Lightweight: Carbon fiber is a fraction of the weight compared to traditional materials, such as steels and aluminum. This makes it exceedingly desirable for industries where weight is critical, such as aerospace and motorsports.
- High Strength: The high modulus of elasticity and tensile strength of this material make it able to withstand high loads and impacts without permanently deforming.
- Stiffness: Carbon fiber has spectacular stiffness, making it a great choice for a structural component that cannot bend.
- Durability: Carbon fiber is corrosion and wear resistant, making it long lasting.
- Aesthetic: This materials has a truly unique and sleek look to it. The diagonal black and gray pattern is iconic with high grade engineering and manufacturing. Often associated with high-speed race cars and fighter jets.
The Cons
Despite all the advantages, there are some drawbacks to consider when choosing if carbon fiber is the right material for your project.
- Cost: If weight and strength are not of the utmost importance, chances are that a cheaper material will suffice.
- Will Not Yield: Under heavy forces, this material bends a little but does not permanently deform. Unlike most metals that will permanently deform before breaking. Once the ultimate strength of carbon fiber is reached, the material will break abruptly and catastrophically. In some cases, this can pose safety concerns.
- Poor UV Resistance: UV radiation from the sun can weaken carbon fiber over time. Therefore, may not be appropriate for long-term outdoor uses.
Common Uses for Carbon Fiber
Carbon fiber is a popular choice for engineers and hobbyists alike. High end sports cars, motorcycles, aircrafts, and more rely on high-grade carbon fiber. Likewise, hobbyists increasingly depend on it to make challenging passion projects possible. Ideally for applications where durability, strength, and low weight are top priorities. Additionally, the look can add a distinctive visual ascent.
Low weight is one of the top priorities for remote controlled cars and drones. Any unnecessary weight can severely impact overall performance. The frame for a quadcopter or drone must be stiff enough to resist wind gusts, durable enough to absorb impact of landing, and light enough to get off the ground. This material checks all the boxes.

Similarly, RC cars need to stand up to the forces from tight turns, accelerations, and the impacts from the occasional crash. Whether replacing or upgrading a component on an RC vehicle, or starting your laser cut project from scratch, carbon fiber is an ideal material.
The same benefits can be achieved for larger vehicles as well. Dashboards and switch panels for cars, go karts, and motorcycles are an excellent application for carbon fiber. Along with the lightweight and strength, it provides a sleek and cutting edge look.
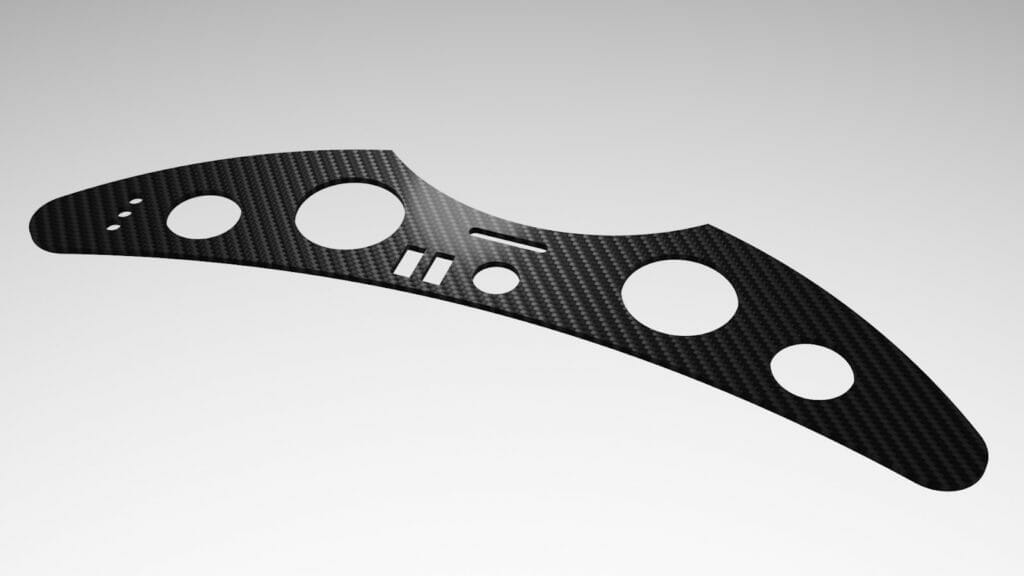
The cosmetic appearance of carbon fiber alone can justify its use. The gray and black diagonal pattern can give a design an industrial and modern look. A carbon fiber piece can act as an accent to a larger design. For example, a carbon fiber pickguard for an electric guitar acts as an excellent shielding material while also giving a completely different look.
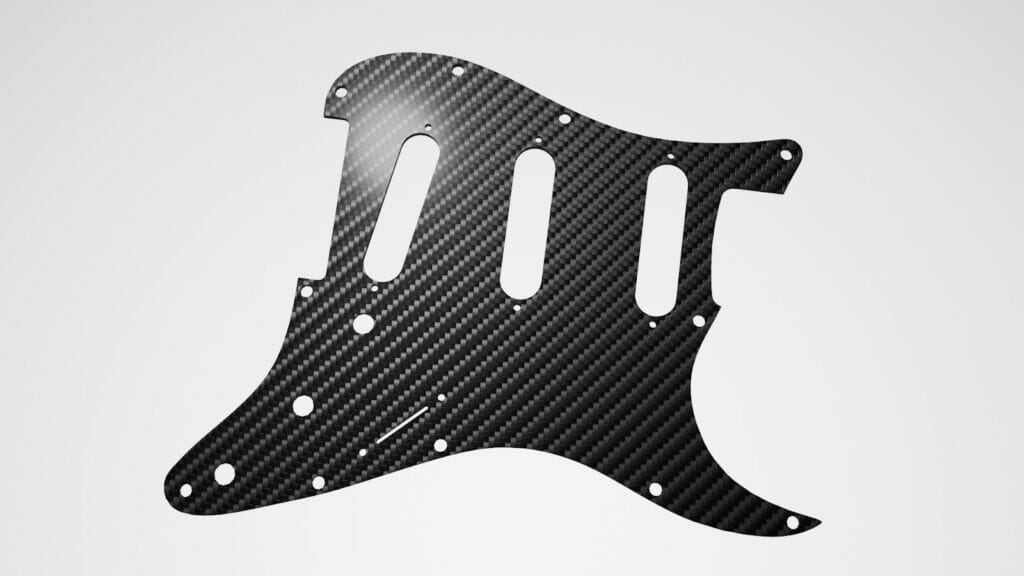
In Summary
Our 2×2 twill weave carbon fiber can be a game changer for your designs. Where strength, rigidity, durability, and lightweight is needed, carbon fiber delivers. We have the equipment and skill to make high quality carbon fiber parts at an affordable price.
Just upload your files to our website once your designs are ready. As always, reach out to our support team with any questions!