Stress concentrations are an important phenomenon to be mindful of when you are designing custom parts for a service like SendCutSend, especially ones that are load-bearing and high-performance. Ignoring them could result in your design being as much as three times weaker, perhaps even more!
Even if you aren’t performing a thorough engineering analysis of your part, mindfulness of stress concentrations and strategies for mitigating them can reduce the likelihood that your designs will fail.
What is Stress?
Stress is a measure of how much force is being carried by a particular cross-section of a part. If a 1-inch (about 25mm) square bar was being pulled on with 1000 pounds of force (about 4500N), we would say it carried 1000 pounds / (1 inch x 1 inch) 1000 pounds per square inch (psi) of stress, or 4500 Newtons / (25 mm x 25 mm) 7.2 Megapascals (MPa).
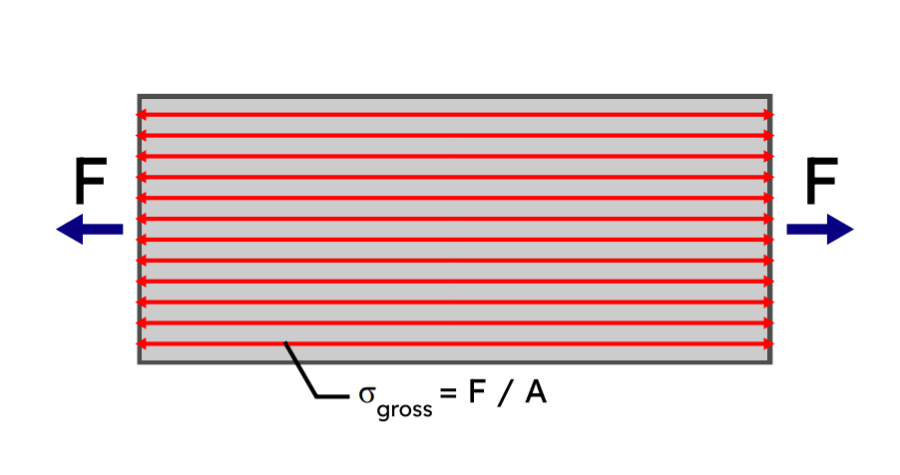
All materials have stress limits such as yield or fatigue – if you exceed them, the material will bend or break – so care must be taken to keep stress to a minimum.
Real parts are hardly ever simple bars being pulled in tension, though. They often bend, have compound loading, and very importantly, have complicated geometry such as holes.
What is a Stress Concentration?
A stress concentration is a location in a part where the stress is much higher than the surroundings. These occur where there are irregularities, discontinuities, or interruptions in the geometry or material, causing the flow of stress to be diverted.
Take for example this hole in the center of a plate which is being pulled apart. We can visualize the flow of stress by drawing lines. Where these lines bunch up together, there is a higher amount of stress.
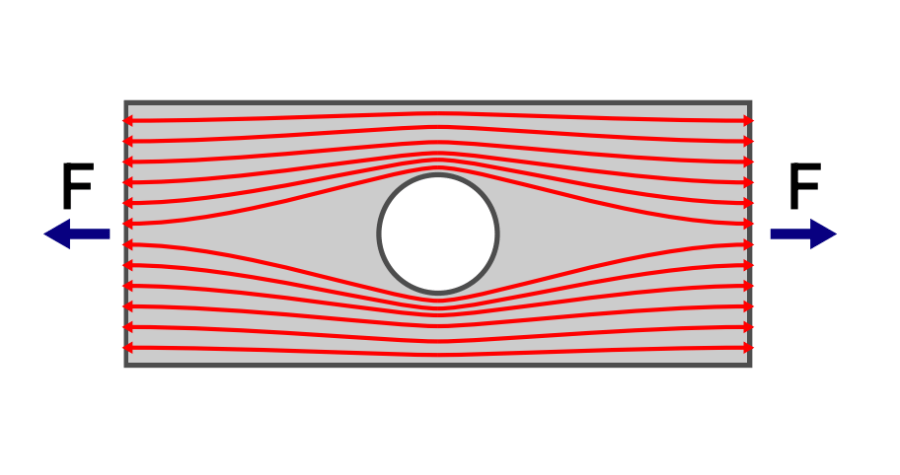
Calculating / Estimating Stress Concentrations
Engineering analysis can help in determining just how much higher the stress is at a concentration.
This can be done with the use of various formula and tables, such Roarke’s Formulas for Stress and Strain, or those at websites like eFatigue.com.
Take the “Rectangular Bar with Opposite Edge Notches”. Using Gross Section Stress, if it is 12mm wide, with a radius of 2mm, then the stress concentration factor Kt 3.05. This means that the maximum stress (seen around the notches) will be 3.05 times higher than the stress the the rest of the cross section.
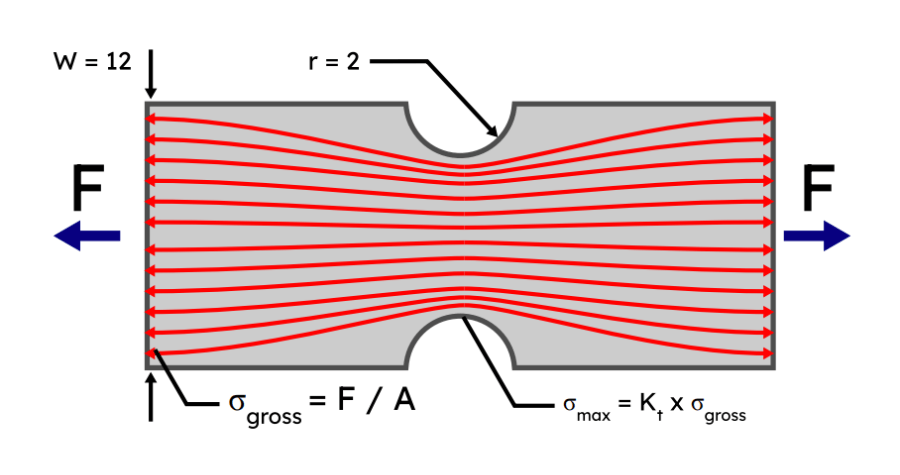
A more advanced method is to use Finite Element Analysis (FEA), which is found in many CAD packages today or available as standalone software. FEA tools can be difficult to learn, and the results cannot always be trusted, but they can be used to understand very complicated loads or geometry.
In this example, a gear is being analyzed – note the high tensile stress in red at the base of the gear tooth, and the high compressive stress in blue where the gear’s contact with another gear has been simulated. Note also that this stress is tremendously higher than in the rest of the part!
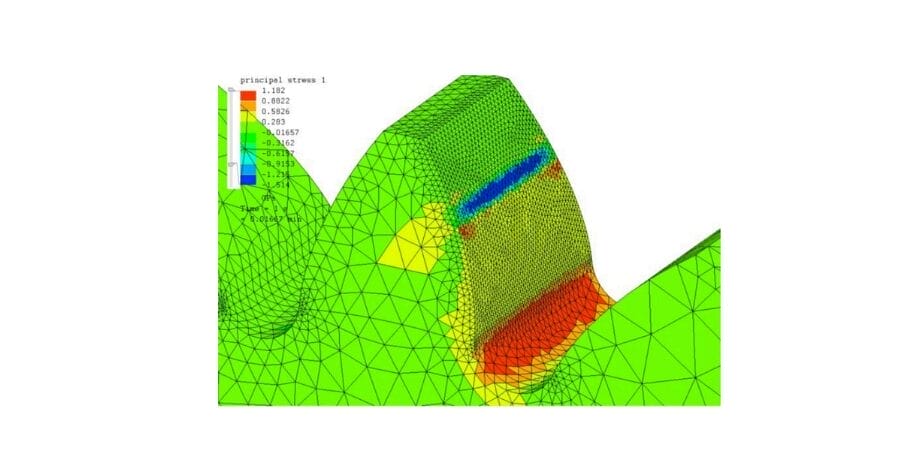
Strategies for Mitigation
Ultimately, a designer wants to mitigate the effects of stress concentrations. You can employ these strategies even if you haven’t undertaken engineering analysis:
- Use large fillet radii, especially for inside corners, where two segments of a part meet.
- If designing two pieces that must slip past one another, use reliefs. Infinitely sharp inside corners cannot be laser cut anyways (limited by the width of the laser beam), so this is a good practice!
- For interfacing with shafts or other components that should have a hole in them, a countersunk hole can be used to provide space for a fillet.
- Though counterintuitive, adding additional stress relief holes in front and behind a larger hole can help to reduce stress concentrations. Without analysis, this is a risky strategy. Elongating holes can also accomplish the same result.
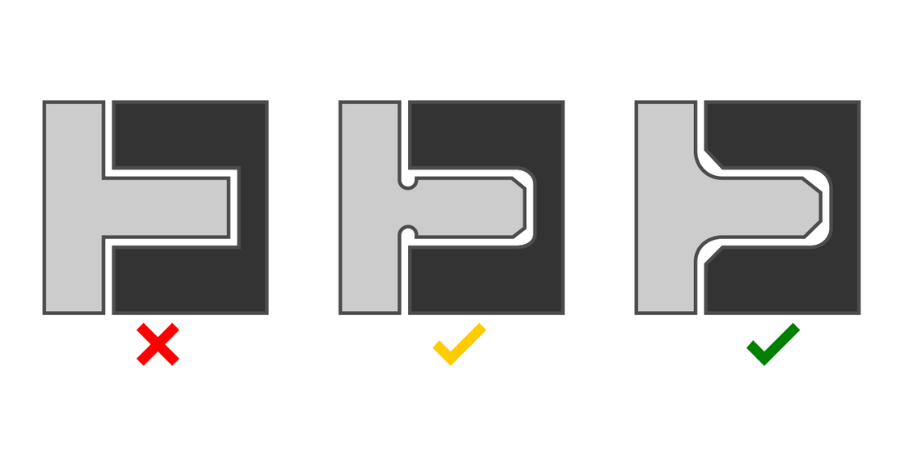
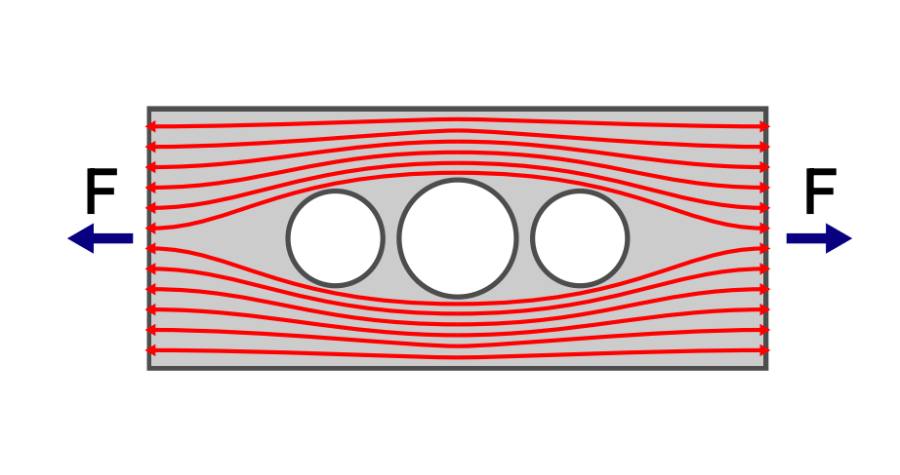
Cases where Stress Concentrations are Desirable
Sometimes, a designer might want to induce a stress concentration, to make the component intentionally break. Some examples include:
- A ‘mechanical fuse’, an inexpensive component that breaks in a controlled fashion instead of more expensive ones, such as a shear bolt.
- A segment of a part which is field removable without a cutting tool – think of perforations on a bag, or knock-out holes in an electrical junction box.
Being Mindful of Stress Concentrations in Your Design
Designers should be mindful of stress concentrations, especially on load-bearing and high-performance parts. There are various tools to estimate stress concentrations, ranging from simple calculations to complex FEA. Even if not performing analysis, there are still strategies designers can employ to minimize the impact of stress concentrations.
This article was contributed by Thaddeus Hughes