Understanding the different behaviors of materials is vital to a well executed design. The set of descriptions that outline how a material behaves are referred to as material properties. It’s astonishing how much difference there can be in materials that are so similar! As an example, 5052 aluminum and 7075 aluminum, two specific alloys of aluminum, share at least 87% of the same material, yet 7075 aluminum is nearly three times stronger!
In the article below, material properties will be explained for the layman or beginner designer, and the practical implications of each will be outlined. We list out the material properties for each of our materials on their respective pages. You can jump to the material details by adding #details to the end of the URL. For example: https://sendcutsend.com/materials/ar400/#details
Material Density
Density is a fairly straightforward property, it is weight per unit volume. What this means is how much an object made of the material in question and of a standard size weighs. This is often expressed in pounds per cubic inch (lb/in3) or pounds per cubic foot (lb/ft3). A cubic inch is the amount of space (aka volume) taken up by a cube that measures exactly one inch per side, similarly cubic feet is a cube measuring one foot per side.
Most have heard the riddle “which one weighs more, 1 lb of feathers or 1 lb of bricks”. Density is the relation being played off of in that riddle since feathers are much less dense than bricks, and thus take up much more volume (space).
From a practicality standpoint, density and its relationship to weight make it critical when weight is important. Any design that is flying, floating, moving, or otherwise weight sensitive should have density included as part of the material decision process.
As an example of this, consider mild steel and 6061 aluminum. 6061 aluminum is similar in yield and ultimate strength, yet is much less dense by nearly a factor of 3, making 6061 aluminum have a much higher strength to weight ratio.
Material | Mild Steel | 6061 T6 Aluminum |
Density [lb/ft3] | 490 | 170 |
Yield Strength [ksi] | 45 | 39 |

Density determines if an object floats or sinks. If an object is more dense than water, it sinks like the steel in the glass above. If an object is less dense than water, it will float, like the pine wood. Both objects are the same size, yet the density changes how they interact with water.
Material Strength
In the next sections we will be defining different material strength limits. However it is important to generically define what material strength is as a foundation for understanding the following sections. Material strength refers to the capacity of a structure to resist loads. Essentially it is the stress level that will cause a certain failure to occur in a material. Stress is simply defined as force over area (force/area), it is analogous to pressure.
As an example of stress, consider a balloon. If 20 pounds of force were applied to a balloon by a bare hand, nothing would happen. However, if even a fraction of that were applied to the point of a knife on that same balloon, it would pop. The hand distributes the force over a larger area, thus reducing the pressure. Conversely, the knife concentrates all the force into a sharp point, making the pressure much higher as the force is only applied over a very small area. This is a perfect demonstration of the impact that stress has on the world.
Fatigue Strength
Material fatigue is a fairly complex topic. Material fatigue is the failure of a part due to repeated cycles of loading and unloading a part, in other words, adding force to and taking force off of a part many times. Each cycle damages the part, and eventually the part fails.
The classic example of this is a paperclip. If a paperclip is bent straight then folded back repeatedly, eventually it fails where it was being repeatedly bent. This failure mode is fatigue. When it comes to material properties, fatigue strength is a stress level that can be endured for a particular number of cycles. The higher the cycles, the lower the fatigue strength will be, until an infinite life fatigue stress value is reached. The fatigue strength listed on our materials page is for infinite life cycles. Here’s an example from the material details on 2024 aluminum.

When taking fatigue strength into account, consider the following: How many cycles does the design need to endure? Is the load consistent or does it fluctuate to higher or lower load levels? Does the load reverse direction or is it always in the same direction? All of these factors contribute to determining the fatigue life of a design.
Practically speaking, if a design is expected to experience fewer than 1,000 loading cycles, fatigue isn’t much of a concern.
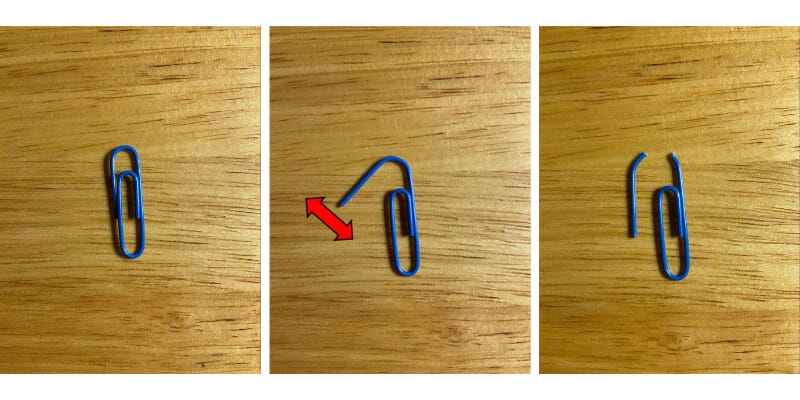
In the example above, the paper clip is bent repeatedly at the same spot until it fails. This type of failure due to multiple load cycles is fatigue failure.
Tensile Strength (Yield)
Yield strength is defined as elongation of a piece with no increase in force. Practically speaking, this is when plastic deformation starts to occur, or when a permanent change in shape happens to a part. Consider the same paper clip as previously outlined. If it is gently bent out of shape and put around paper, it snaps back into the same shape it started as; this is elastic deformation, and yield has not been reached.
Think of elastic deformation as rubber bands and how they stretch then return to their original shape. However, if the paper clip is bent too far, it will take the new shape permanently, and not return to the original shape. This permanent deformation is plastic deformation, or yielding, and is the opposite of elastic deformation.
From a practical perspective, yield is often considered as the part failing. Most designers seek to avoid yielding as it tends to weaken a part, and will design parts such that they never experience yield stress levels.
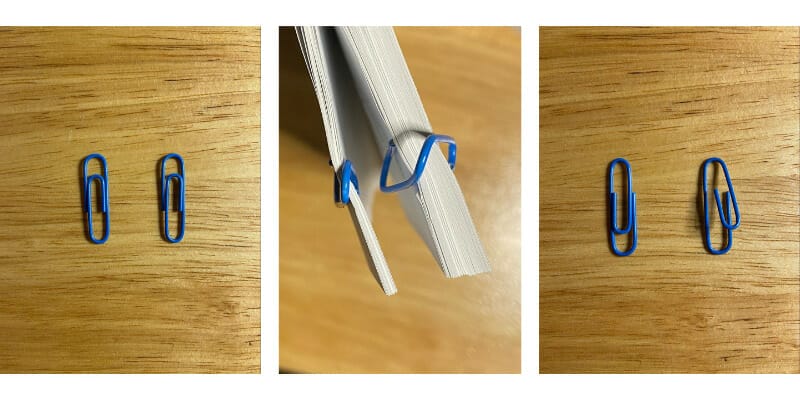
In the example above, the left paper clip is bent around 10 pieces of paper, and elastically returns to its original shape. The right paper clip is bent around 100 pieces of paper and plastically deforms, or yields, into a new shape permanently.
Tensile Strength (Ultimate)
Ultimate strength is the highest stress level a material can withstand without breaking, in other words, this is the load level that the part will completely fail at. While yield strength can theoretically be exceeded without failure, ultimate strength cannot be exceeded. Everyone has had the misfortune of having a rubber band snap. This occurs when it is stretched beyond its ultimate strength limit, and it completely breaks.
From a practicality standpoint, the ultimate strength limit is an absolute upper bound that should never be exceeded, and good practice should also include a safety factor as well.
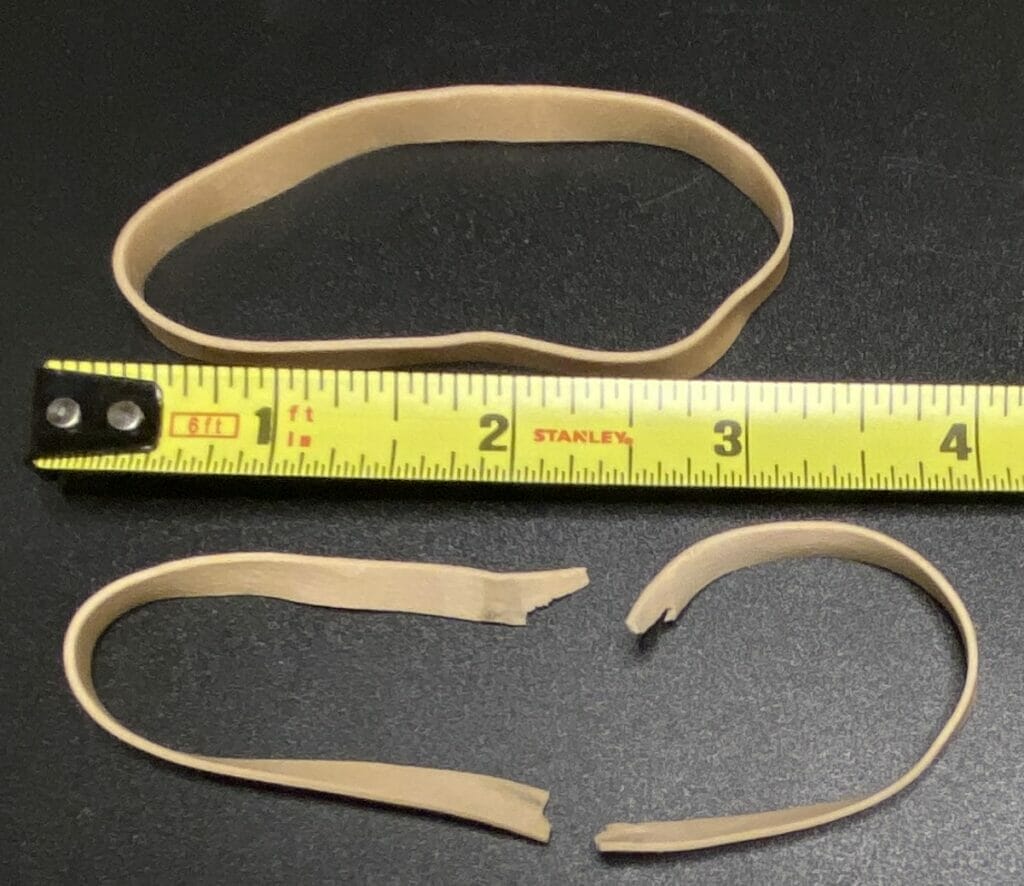
A rubber band, when stretched too far, will snap due to the ultimate tensile strength being exceeded.
Shear Strength
Shear is a failure due to opposing loads trying to slide past each other. For example, scissors cut paper by forcing the two arms past each other, trapping the paper between them. Shear strength is always lower than yield or ultimate strength, and thus it must be taken into account to make sure the proper strength is used based on loading direction. Shear can also be applied in torsion or twisting applications.
For example, when tightening a bolt, if it is overtightened enough, the bolt will break. This failure of the bolt is almost always due to shear loads, unless a defect is present.
For practical application of this, a design’s load direction must be taken into account. Shear strength has a similar behavior to ultimate strength in that it can’t be exceeded or the part will fail, thus designs should never exceed shear strength.

Above the three main types of simple loadings are outlined. The difference between compressive and shear stress is that the shear stress forces are offset from each other, in contrast to directly opposing each other. The dotted line in the shear stress diagram indicates the shear plane, or the center between the two opposing forces.
Elastic Modulus
Elastic modulus is also known as Modulus of elasticity or Young’s Modulus, and adheres to Hooke’s Law. In simple terms, this is a material’s resistance to deformation, or its stiffness. When looking at how materials behave when they have a force applied to them, all materials act like a spring unless some failure has occurred such as yielding*. When you stretch them, they return to their original shape, and the same is true when you compress them. The elastic modulus is the stiffness of that spring.
Practically speaking, elastic modulus is used to determine how flexible a material is, and how much stress will be imparted on that material for a particular change in length. Higher values indicate stiffer materials (like metals) while lower values indicate softer materials (like plastics).
*Note: With metals, it is harder to visualize them acting as a spring because the deformations are typically very small, and not visible. However the spring-like behavior is the same with metals as it is with rubber bands, and all materials.
Shear Modulus
Shear modulus, also known as modulus of rigidity, is the same as the elastic modulus, but for shear loads. So the shear modulus is the stiffness of the material relative to resisting shear. Shear modulus is the division of shear stress over shear strain G = shear stress/shear strain. This is similarly the resistance of a material to deform under shear loads, or spring stiffness when a material is loaded in shear.
In practice, this property is used to find the more useful elastic modulus through its relationship with Poisson’s Ratio, which is described below.
Poisson’s Ratio
Poisson’s ratio, pronounced (pois·son·s), is the relationship between axial deformation and lateral deformation. In practical terms, this is how much a material will shrink in one direction as it elongates in the other direction*.
For most practical applications, this won’t impact a design much, but it is a vital number to know for some engineering calculations and analysis.
*Fun fact: while it is rare, there are some materials that actually grow in both directions at the same time. These materials simply decrease in density as they stretch to achieve this phenomenon, and are not useful for structural applications.
Elongation at Break
Elongation at break is exactly what it sounds like, how far a piece elongates (stretches) before it breaks. On our materials page it is represented as a percentage. This percentage is a percent length change. If a sample of 6061 aluminum is 1” long, then it will break when it has reached 1.10” in length since it has a 10% elongation at break. Elongation at break is a measure of a material’s ductility, or a material’s tendency to stretch before it breaks. Being ductile is the opposite of being brittle. Glass is very brittle, it does not bend much before it breaks. Conversely, a rubber band is very ductile and it stretches a great deal before it breaks.
In practice, a material’s ability to stretch can be an asset or a hindrance. For example, sometimes it is critical to hold a dimension absolutely exact, even at the expense of a part breaking instead of that dimension changing. Alternatively, the ability to stretch and have give might allow a more sensitive part to take less load and reduce risk of it breaking.
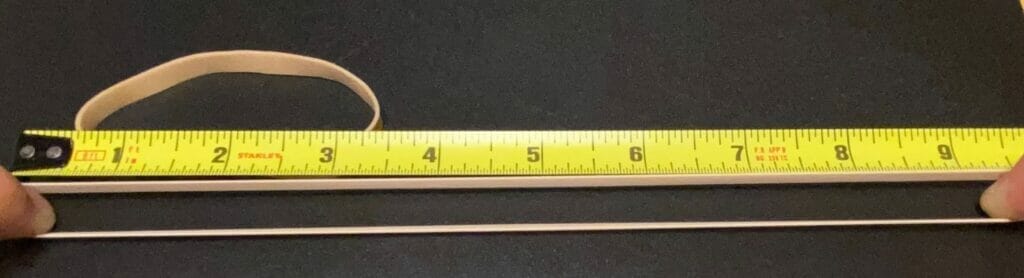
While aluminum can only elongate 10% of initial length before breaking, a rubber band can stretch to more than 200% of initial length before breaking.
Brinell Hardness
Brinell hardness is one of many possible tests for how hard a material is. Hardness is a material’s resistance to local deformation. Hardness is closely related to elastic modulus, and the two tend to increase and decrease together. As an example of two extremes, consider foam and steel. As you push an object into foam, it easily accepts the shape of that object and bends around it; this indicates a very low hardness. Towards the opposite end of the spectrum is steel. Steel is a relatively hard material, and it takes quite a bit of force to indent the surface of steel.
Practically speaking, hardness can be very beneficial in a design, but typically, if a material is very hard, it is also very brittle and it is an all or nothing type of trade off. A brittle material breaks very suddenly, and has all of its strength or none of its strength. Hardness is especially important to consider for designs that withstand impacts or high levels of abrasion.
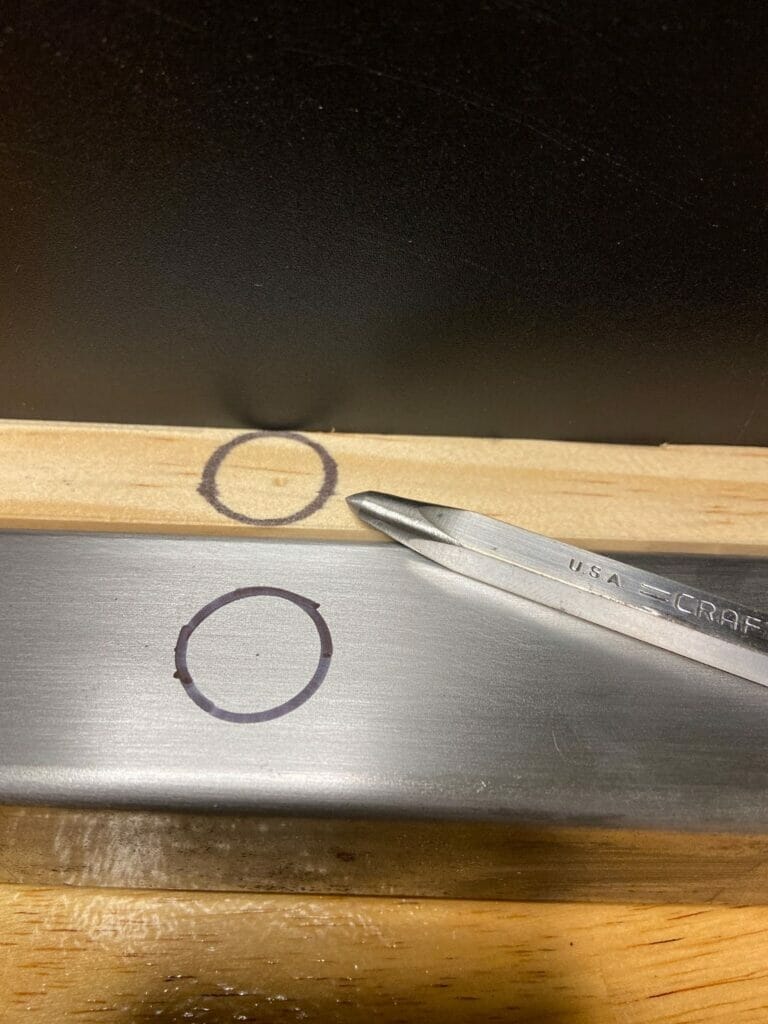
Within the two circles above, the punch was pushed into the materials with the same level of force. Note that the much softer wood is indented, while the harder steel is barely scratched.
Thermal Conductivity
Thermal conductivity is how well a material transfers heat. The higher the value, the faster the material heats up. As an example, if a piece of steel and a piece of aluminum of the same size were placed in a fire for 10 seconds, the aluminum would increase in temperature roughly 3x more than the steel.
This property is particularly important anytime there are temperature sensitive parts that could be damaged by high heat. It is important to keep in mind though, that thermal conductivity is a bit of a double edged sword. While steel takes longer to heat up than aluminum, it also takes longer to cool down.
Melting Point
Melting point is another fairly self explanatory property, this is the temperature that a material transitions from a solid to a liquid form. I.e. For water, the melting point (also known as the freezing point) is 32 degrees F. This is the temperature it will change to a liquid, aka melt, as energy (heat) is added, or to a solid, aka freeze, as energy is removed (cooled).
Practically speaking, this is mostly relevant in high temperature applications where a design might see extreme heat or friction*.
*Note: while not within the scope of this article, some materials, especially tempered materials like 6061-T6 aluminum, will change properties well below their melting temperature. If the temperature gets high enough, it can alter the crystalline structure of the material. This will ruin the temper, and change how that material behaves structurally, usually making it much weaker.
Magnetic
Magnetism is a fairly straight forward property. It is simply the ability of a metal to attract a magnet. Typically magnetic materials contain iron, cobalt, and/or nickel. There are varying degrees of magnetism. For example, one way to determine if a mill bit is made of carbide or high speed steel is to see how magnetic it is since high speed steel is much more magnetic than carbide.
From a practicality standpoint, magnetic metals can be beneficial in materials handling, especially for larger pieces, but they might be a detractor for use in or near electronics.
Does it Rust
Rust is iron oxide. While many materials oxidize, only some of these oxide layers are corrosive. For both aluminum and titanium, their respective oxide layers offer a protective layer from outside elements. For mild steel however, the opposite is true. Iron oxide, aka rust, is a corrosive compound that eventually corrodes through steel, iron, and other ferrous metals*.
From a practicality standpoint, this simply means that if a design is made of a metal that rusts, and it is going to be exposed to water or high humidity, it will need to have a coating of some kind to protect it. Fortunately, we now offer powder coating to protect your designs from the elements!
*Ferrum is the Latin name for iron which is why it is identified as Fe on the periodic table. Ferrous simply means that the material contains iron.
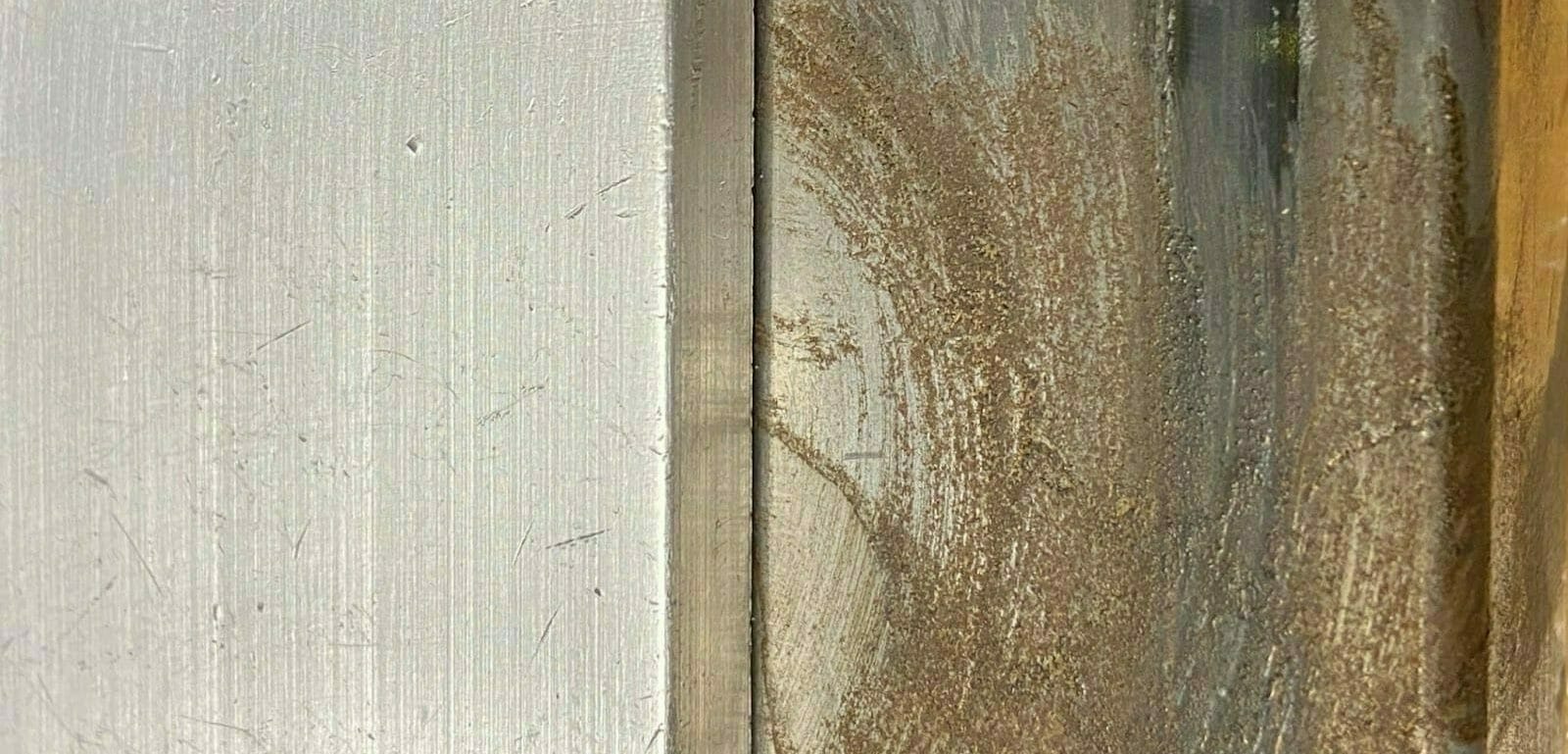
The material on the left, aluminum, creates a protective oxide layer very quickly. While the material on the right, mild steel, rusts over time via a corrosive oxide layer.
Material Composition
Material composition is simply what specific elements a material is made of. For example, 5052 aluminum is 95.8-97.7% pure aluminum, with various other elements added in, making it an aluminum alloy. Alloy simply means it is a mixture of two or more metals. The number “5052” is a specific alloy, which is comparable to a specific recipe that is published by an engineering organization. It designates that certain elements must be present, and in specific ratios to qualify as that particular alloy. These elements will impact how the material behaves. Some aluminum alloys are much stronger than others. For example, 5052 aluminum has an ultimate strength of 34 ksi, while 7075 aluminum has an ultimate strength of 81 ksi. Despite the fact that both materials are at least 87% identical, this last 13% of the composition results in more than double the ultimate strength.
For most practical purposes, material composition won’t impact a design much, unless there is some restriction on use of a particular material, like lead, or there is some reaction with a particular element that is trying to be avoided.
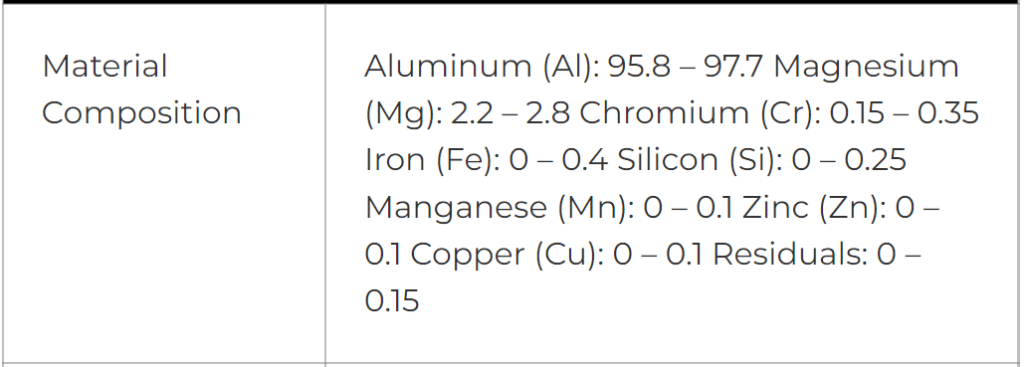
Material properties encompass a large amount of characteristics and behaviors. So much that entire books are written describing material properties. Above is a very brief overview of the basics to convey a top level understanding of what these properties are, and how to effectively utilize them in your designs.
For other blog posts specifically pertaining to materials, check out the materials category on our blog! There we have articles on everything from light and strong titanium, to colorfully anodized aluminum, or even abrasion resistant steel that is quite literally bulletproof.
If you have any questions, feel free to reach out to our support team. When you’re ready, upload your design and get instant pricing today!
If you are new to SendCutSend, here’s a handy step-by-step guide on how to order parts from us: How to Order Parts from SendCutSend (spoiler alert: it’s super simple and intuitive to order from us).