Waterjet cutting is a manufacturing process that uses high-pressure water streams, often with abrasive particles mixed in, to cut through various materials. The water is pressurized to extremely high levels and then forced through a small orifice, creating a narrow stream that can be directed to cut through a variety of materials.
The history of cutting with a waterjet dates back to the 1950s, when researchers began exploring the use of water as a cutting tool. Initially, water was used on its own, but later abrasive particles were added to the stream to increase cutting power. Today, waterjet cutting is used in a variety of industries, including aerospace, automotive, and manufacturing.
The Best Materials for Waterjet Cutting
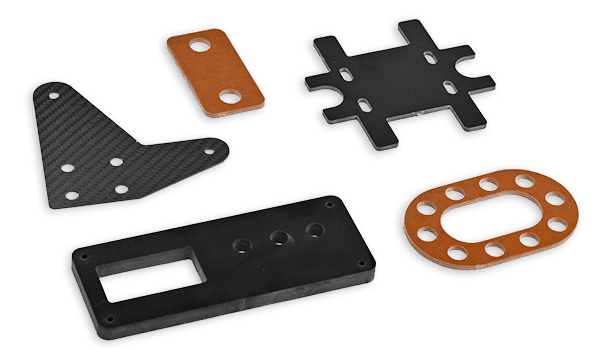
Waterjet cutting is generally more expensive than other cutting methods because of the high cost of the equipment and the specialized training required to operate it. However, the precision and versatility it is capable of often make it the best option for cutting certain materials, such as thick metals or materials that would be damaged by other cutting methods.
A wide range of materials can be cut using a waterjet, including metals, plastics, ceramics, glass, and composites. At SendCutSend we use our waterjet to cut Carbon Fiber, G10 Stainless Steel, and LE Phenolic materials.
Carbon Fiber
Carbon fiber is a composite material made of carbon fibers that are embedded in a matrix material, usually a type of resin. It is a lightweight and strong material that is commonly used in aerospace, automotive, and sporting goods industries. Waterjet cutting is ideal for cutting carbon fiber because it does not produce heat, which could damage the material, and because it can produce precise cuts with minimal delamination (separation of the layers of the composite material).
At the time of writing this article, we stock Carbon Fiber from .040” to .118” thickness.
G10
G10 stainless steel is a type of composite material that is made of layers of fiberglass and resin. It is a durable and heat-resistant material that is commonly used in the aerospace, marine, and electrical industries. Waterjet cutting is ideal for cutting G10 stainless steel because it can produce precise cuts with minimal delamination, and because it can easily cut through the fiberglass layers without damaging the resin.
At the time of writing this article, we stock G10 in 0.63” to .375” thickness.
LE Phenolic
LE Phenolic (low-smoke, low-flame phenolic) is a type of composite material that is made of layers of phenolic resin and paper or fabric. It is a fire-resistant and low-smoke material that is commonly used in the aerospace, marine, and transportation industries. Waterjet cutting is ideal for cutting LE Phenolic because it can produce precise cuts without producing heat or causing the material to delaminate.
At the time of writing this article, we stock LE Phenolic in .125” to .375” thickness.
The Benefits of Waterjet Cutting
In general, waterjet cutting is a good choice for cutting materials that are sensitive to heat, such as composites or plastics, or that have complex geometries. The waterjet can produce precise cuts with minimal distortion or delamination, and can leave smooth edges without burrs or dross. However, as the waterjet operator, it is important to choose the appropriate abrasive material and pressure settings to ensure the best results for each specific material.
No HAZ
Because waterjet cutting does not create a heat-affected zone (HAZ), it is an ideal method for cutting materials that are sensitive to heat or that have complex geometries. HAZ refers to the area of a material that has been affected by heat from a cutting or welding process, and can result in changes to the material’s properties or appearance.
Edge Quality
Waterjet cutting provides super edge quality due to the combination of water speed, pressure, nozzle size, and abrasive flow rate. The high-pressure water stream allows for precise cuts with minimal distortion, while the addition of abrasive particles increases cutting power and reduces burrs or rough edges.
No Burr or Dross
Waterjet cutting also leaves little to no burr or dross, which are unwanted edges or protrusions that can occur during other cutting methods. This makes it ideal for materials that require smooth edges or surfaces.
Waterjet vs Laser Cutting and CNC Routing Services
Compared to fiber laser cutting or CNC routing services, waterjet cutting has several pros and cons. It is ideal for materials that are sensitive to heat, have complex geometries, or require smooth edges or surfaces. However, this cutting method can be more expensive than other methods, and may not be the best option for cutting thin or delicate materials. Fiber laser cutting and CNC routing machines are generally faster and less expensive, but may not provide the same level of precision or versatility as waterjet cutting. Ultimately, the best cutting method depends on the specific material, application, and budget.
SendCutSend Chooses the Best Cutting Operation for You
With several waterjet cutters at our disposal, we can choose the best cutting method for each project based on factors such as material type, thickness, and design.
When you upload your design to the SendCutSend we will determine the best cutting method based on the specific requirements of your project.
With more than 200 materials available, each one of our material pages has in depth information about the best use for the material, thicknesses that we offer, the cutting process and post cut operations that are available for that material. If you know you’re using a material that will be cut on the waterjet, please reference our waterjet cutting guidelines to make sure your file is ready to be cut.