Many makers decide they want to weld their own laser cut parts. This decision can be a daunting one; the upfront costs can be high depending on what equipment you choose, and there’s a definite learning curve, especially if you decide to jump into TIG welding (more on that later).
At the same time, there is no more versatile tool you can add to your design-build “toolbox” than the ability to weld two custom-made pieces together. Not to mention the satisfaction that comes from seeing your idea go from a napkin-sketch all the way to finished product using your own tools and ingenuity. So if you’re just getting started, congratulations!
Here at SendCutSend, we supply the right material for just about any welded part or assembly cut quickly and accurately every time.
This article covers
- Welding Methods: Stick (SMAW) vs. TIG (GTAW) vs. MIG (GMAW)
- Material selection: which metal fits my project goals best?
- Prep/Post: What cleaners, surface finish, or beveling. Post-weld finishing?
- Gauge, strength-to-weight and cost considerations?
Caution: Welding is an inherently dangerous process. Be informed on how to protect yourself from arc flash, weld fumes and electrocution. Play it smart and play it safe every single time you strike an arc.
Different Methods of Welding
There are three common welding methods that each use heat generated by electrical current (the electrode can be the clamp/stick, torch or gun depending on method) and a similar filler metal to make two pieces into one.
In non-technical terms, you could say:
- Stick welding: Hold the filler rod with the clamp and it becomes the electrode. Go to town.
- TIG welding: Hold the filler rod in one hand and the torch (electrode) in the other. Alternate.
- MIG welding: The filler rod (electrode) feeds continuously out of the gun. Super fast.
Here’s a closer look at each of these methods
Stick Welding – Shielded metal arc welding (SMAW)
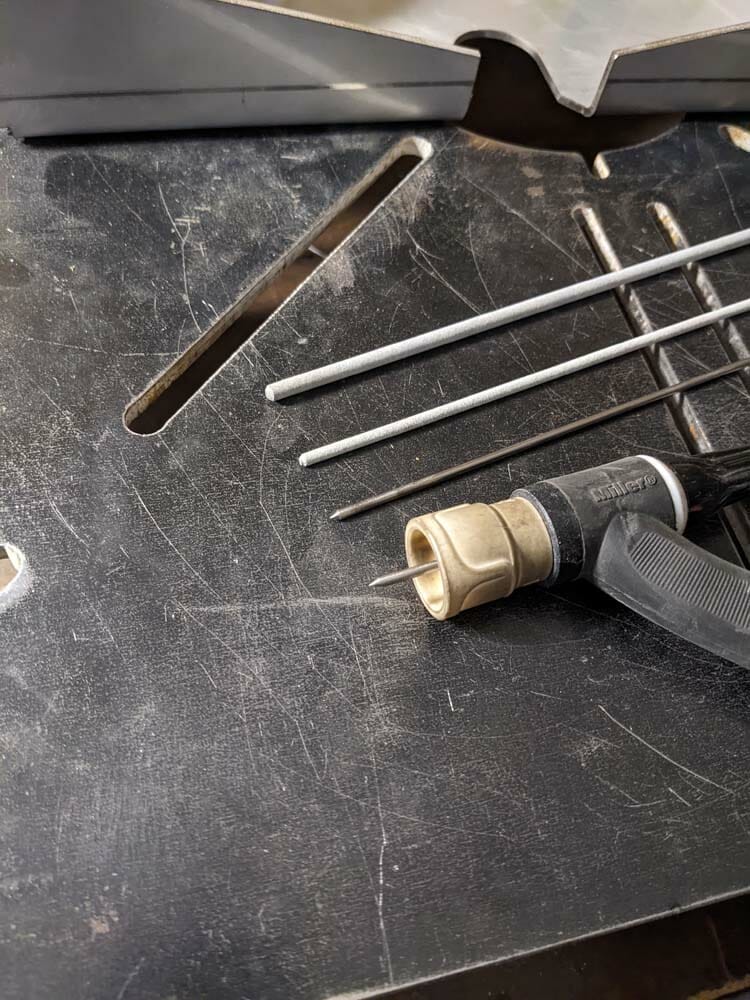
How does stick welding work?
In stick welding, a handheld clamp (often called a Stinger) is used to hold the metal electrode which is consumed in the welding process. To protect the weld pool from the atmosphere (required for any welding method) the electrode is coated with flux, which off-gasses when heated, displacing the air around it. As the weld cools, a slag layer protects the new joint from further oxidation.
Pros of stick welding:
- Inexpensive equipment and consumables (no shielding gas required).
- Quick and dirty welding – great when you need to stick two pieces of metal together with minimal time or ability to prep them properly.
- Easy to change from one material to another by simply changing your electrode.
- Portability. Good results even in the wind and rain. Even underwater (but don’t try that at home!).
Cons of stick welding:
- Harder to control quality, porosity, and consistency.
- Have to clean off significant amounts of slag and often spatter post-weld.
- Generally slower than MIG welding.
- Hard to use on thinner gauge metal.
TIG Welding – Gas Tungsten Arc Welding (GTAW)
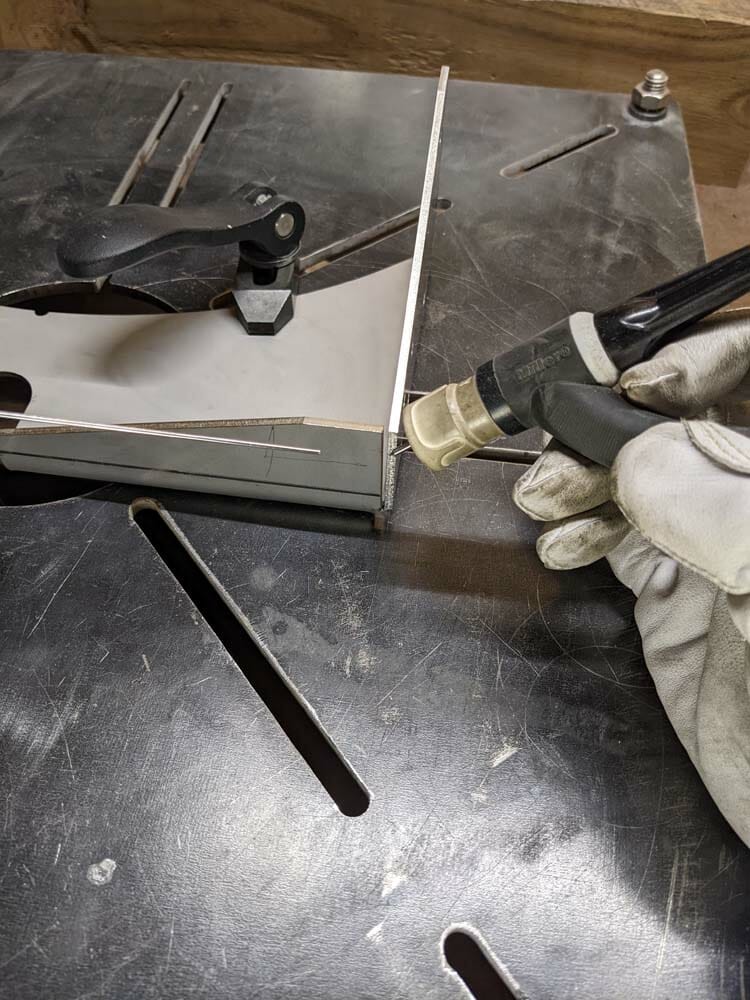
How does TIG welding work?
In TIG welding a torch, which supplies current to the electrode and shielding gas around it to protect the weld pool, is held in the dominant hand. The electrode is made of tungsten, which is often alloyed with small amounts of cerium, thorium or lanthanum oxide to give it desirable characteristics such as fast arc starts, high current capacity, and cool running.
The filler rod is held in the other hand and is typically dipped in and out of the weld pool to form the weld bead. A foot pedal is often used to modulate the current input to the torch. The TIG process can be used to weld most steels (DC current) or aluminum (AC current). Although the learning curve is steeper with TIG than other methods, (how do you get both hands and a foot to coordinate with each other?) it is by far the most versatile and controllable process.
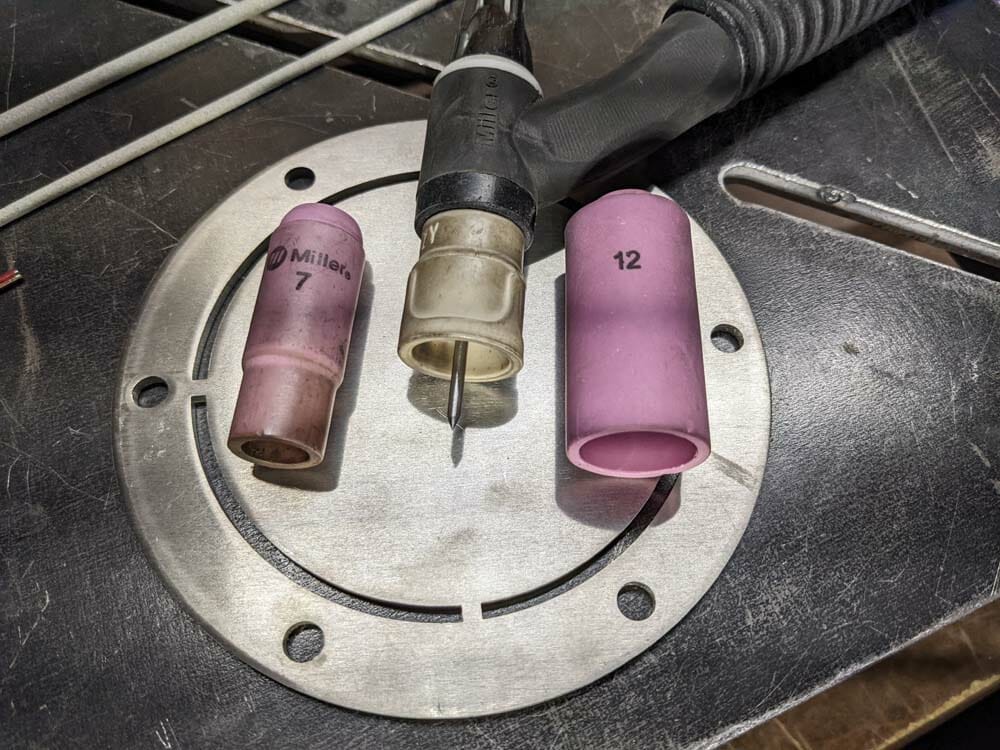
Pros of TIG welding:
- Any material that you can weld can be welded with the right TIG setup.
- Moving from one material to another often requires simply changing the filler rod. Dissimilar metals aren’t a problem.
- Aluminum welding at gauges lighter than about 14ga can ONLY be done with TIG.
- Mechanically much simpler than a MIG gun because the electrode is stationary.
- With things like high frequency start and pulse output, making a beautiful weld is almost effortless after a little practice.
- Cleanest welds possible.
Cons of TIG welding:
- Higher cost consumables. You need shielding gas such as Argon or CO2, depending on the process, and extra electrodes.
- Higher initial cost. Depending on the use case and duty cycle, water cooling may be necessary and this can add thousands to the price.
- Parts must be very clean for best results.
MIG Welding – Gas metal arc welding (GMAW)
How does MIG welding work?
As with TIG welding, shielding gas is fed through a handheld gun, but with MIG welding the wire is fed from a spool in the welder through the tip of the gun. This wire is both the electrode and the filler wire. Typical shielding gas is 75% argon and 25% carbon dioxide (75/25 or C25) which is an all-purpose shielding gas for carbon steel with minimal spatter, nice bead appearance and less burn-through at thin gauges. Because the wire is fed automatically, this method is the fastest and most resistant to vertical and overhead welding positions. It is also quite simple to get the hang of.
Pros of MIG welding:
- One-handed operation.
- With the right electrode, it’s possible to weld on dirty or rusty steel with good results.
- Minimal cleanup post-weld and no leftover electrode or filler rod like Stick or TIG.
- With high-deposition MIG, multiple passes can be avoided while still laying down a lot of metal.
Cons of MIG welding:
- Not good for very thin or very thick material.
- Most complex machines of the three processes mean more time un-jamming your wire.
- Still harder to weld in windy conditions than stick. Although gasless wire can be used.
This is meant to be a very brief comparison of the three methods so you can decide which will work best for your laser cut metal parts. For guidelines and assistance for setting up your welder’s amperage, or which consumables to use, abound online check out Miller’s Weld Settings Calculator.
Once you decide which method(s) fits your use case, you’ll have to pick a metal for your laser cut parts.
What material should you cut?
For a comprehensive list of all our materials and their individual properties, see our Materials Page. For this article, we’re going to look at the heavy-hitters of the fabrication world.
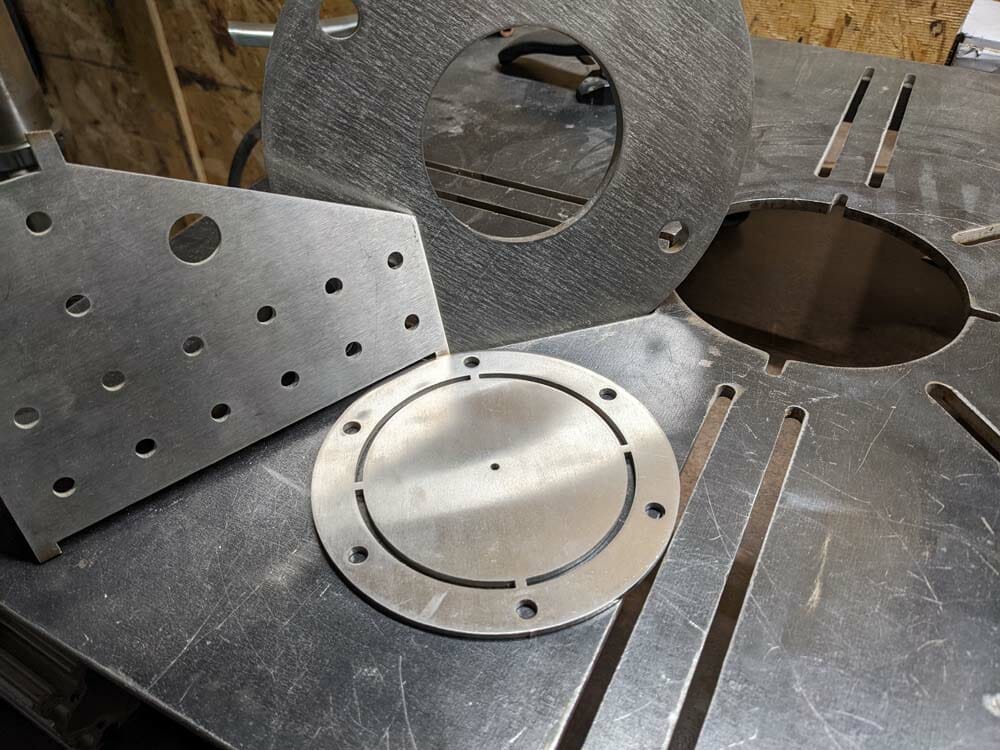
Mild Steel
Mild steel is also known as “low-carbon” steel because of a carbon content that maxes out around 0.33%. While this might not sound like much material, carbon affects the microstructure of the steel and is largely responsible for its durability and toughness.
A high carbon content contributes to weld porosity, britalization and cracking in the heat affected zone (HAZ), and excessive softening further away from the weld. Low-carbon steel avoids all that, maintaining excellent strength and ductility post-welding, and as such, is the material of choice for most fabricating. It is also less likely to warp from the uneven heating of the welding process than a stainless plate welded in the same way.
Along with the most common hot-rolled (HR, HRPO) and abrasion resistant (AR400-500) grades, we carry 4130 Chromoly steel, which adds chromium and molybdenum to the recipe to produce an extremely stress-resistant steel. Use this grade for all your frame (car, bike, even airplane) building needs.
Prepping mild steel for welding:
- Plan to spend some time with a flap disc if you choose HR steel and follow it up with some cleaner to prep the surface for welding.
- The appropriate cleaner depends on the application, but in general, denatured alcohol is a safer alternative to acetone and just fine as prep for welding steel.
- Sandblasting is also a great option for clearing heavy amounts of contamination, rust or paint, although parts you order from us should never need this much prep.
Warning: Never, ever, use brake cleaner as a degreaser to prep parts for welding. From the safety data sheet “Do not use this product near… welding operations, or excessive heat. Vapors may decompose to harmful or fatal corrosive gasses such as hydrogen chloride and possibly phosgene.” This is not a test of the emergency alert system, phosgene is a WW1 choking agent and if it doesn’t kill you, it can impact your health long term.
Post weld tips:
- If you want a uniform surface finish, a wire wheel or fiber disc is a good choice.
- Sandblasting can also be used to achieve an even bare surface post-weld.
- Protect the final product from weather. Paint or powder coating are necessary to prevent destructive amounts of rust.
Stainless Steel
While stainless steel is technically “low-carbon” as well, the secret to its super powers lies in the addition of chromium and nickel, which inhibit oxidation and rust formation.
If you’re looking for a material with excellent weldability, strength comparable to that of mild steel, and complete disregard for harsh environments, look no further.
We offer both 304 stainless steel and 316 stainless steel, which in addition to the chromium and nickel brings about 2.5% molybdenum to the party. This makes 316 the most corrosion resistant and useful for sanitary or medical applications where chlorides are used.
Why not always use stainless? For one thing, it’s more expensive, but it also hardens quite easily so don’t expect to do much cold forming. Machining is also more difficult and it is recommended that tools for stainless be kept separate and very sharp. For these reasons consider having us tap any holes you may need in your stainless parts with our tapping service.
Prepping stainless steel for welding:
- Another benefit of stainless parts cut on our laser is that a simple wipe with alcohol is often the only prep required [confirm that oxide formation from SCS’s laser isn’t a problem].
- Any material 3/16” or thicker should be beveled prior to being welded to ensure full penetration.
- If you plan to TIG stainless to mild steel, make sure to choose an E70S2 or 312 filler rod.
Post weld tips:
- Did you do a good job controlling the heat? Great, you’re done!
- For a uniform finish, hit it with a light abrasive wheel or fiber disc.
Aluminum
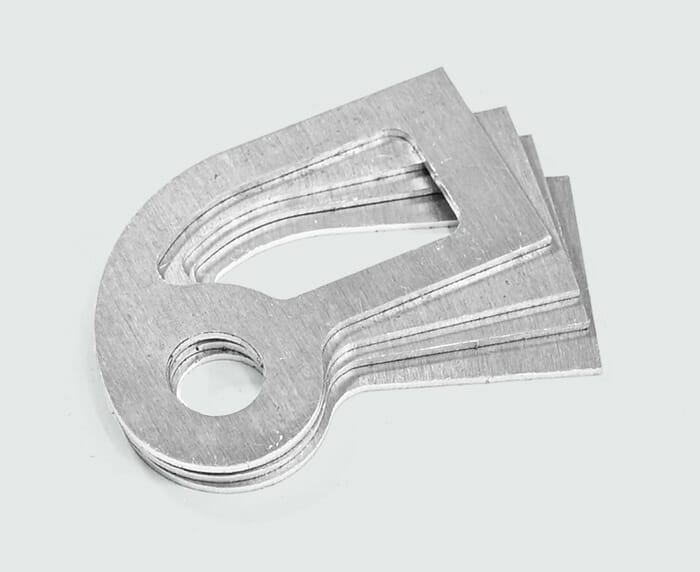
After mild and stainless steels, the most common material for fabrication is likely aluminum. Comparatively speaking, aluminum is a newcomer to the party, only becoming commercially around the turn of the 20th century. That said, due to its outstanding strength-to-weight (aluminum is 2.5 to 3 times less dense than steel) great fatigue strength and general corrosion resistance, it is the go-to material in many industries, from aerospace to robotics to automotive sheet metal.
We offer two grades, 5052 aluminum and 6061 T6 aluminum which can be welded with relative ease. Our other aluminum alloy, 7075 aluminum is great, but because of its chemistry is extremely prone to cracking and stress-corrosion in the HAZ. So stay away from the 7075 unless you have access to friction stir welding equipment. Hint: you don’t!
There are a few caveats that make aluminum welding unique from other materials:
- For TIG, you’ll be using AC (alternating current) rather than DC (direct current), so make sure you purchase a welder that supports both!
- For MIG, consider purchasing a spool gun, where there is a small spool mounted to the gun. This prevents the soft aluminum wire from “birdnesting” in the long trip from the welder to the gun. Also, always push, never pull (drag, backhand).
- If the two pieces are significantly different in thickness, preheat the thicker piece to about 200°F to ensure that it melts at a similar rate as that of the thinner piece.
- For maximum strength and durability from your final 6061 weldment, heat treat for 1 hour at 400°F to remove built up stresses near the weld.
Prepping aluminum for welding:
- The first step is to degrease the metal. Toluene is more effective than Acetone and safer than any chlorinated products.
- Make sure that all moisture is removed from the material’s surface, this means the aluminum should always be allowed to come to equilibrium with the room’s temperature (or even better, preheated so that no moisture can condense).
- Aluminum oxide is present almost immediately after aluminum is cut, so it must be removed as close to the time at which it will be welded as possible. Wire brushing by hand is the best method because it avoids any smearing of the soft aluminum.
Post welding tips:
- Since aluminum oxide forms almost immediately and is super hard (rubies and sapphires are aluminum oxide), you won’t get much corrosion on your bare aluminum.
- However it is susceptible to galvanic corrosion, sulfates and chlorides. So consider painting, anodizing, or our powder coating services.
Whether your welding project calls for the durability and affordability of mild steel, the all-weather elegance and sanitary/washdown properties of stainless steel, or parts cut from featherweight, fatigue-resistant aluminum, here at SendCutSend we have the material you need to make it a win.
For an instant pricing, upload your design today.