Here at SendCutSend, we’ve added waterjet services to our arsenal of machinery to make even more high quality materials available to you, and reduce the cost of some of your projects. Deciding what materials should be waterjet cut was a big part of our process in implementing this service. Our team of experts have picked the materials and designs best suited for waterjet cutting so you can rest assured that we are using the best machining method available for your specific project.
Best Materials for Waterjet Cutting
At this time, we are waterjet cutting all composite materials and thicker metals. This includes:
In general, waterjet cutting is ideal for thick metals and composites. So continue to check back in with our website and sign up for our emailing list to be the first to know when we make other thicknesses and composites available.
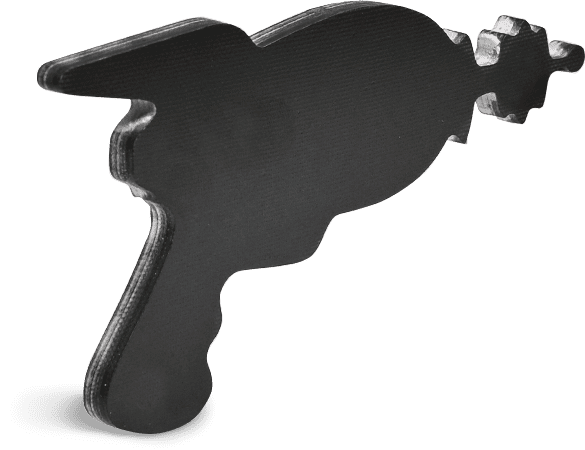
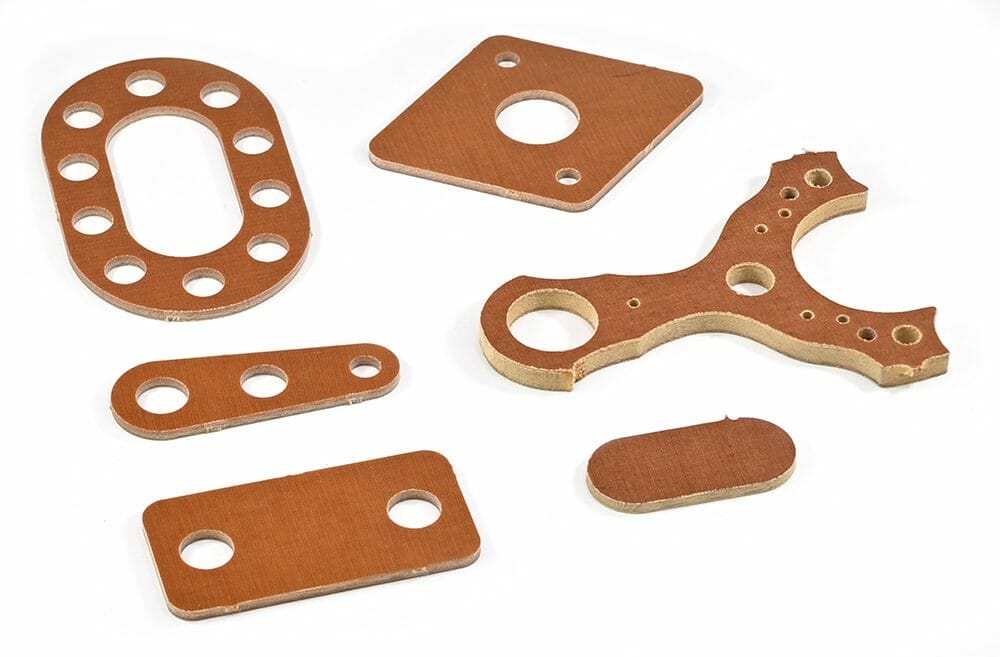
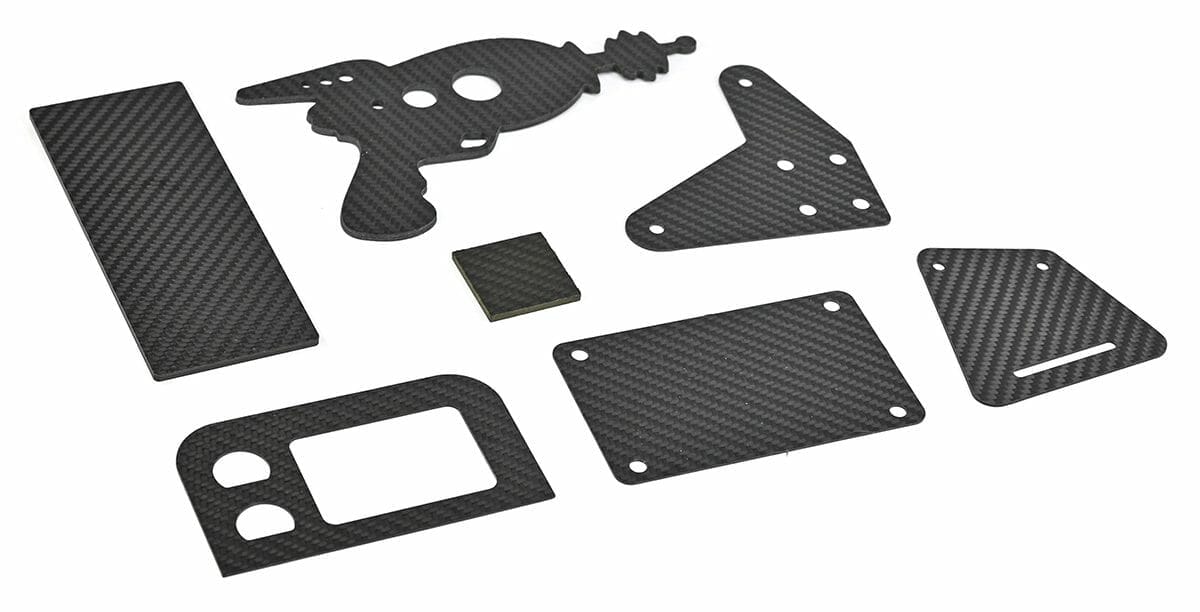
Deciding What Materials to Waterjet Cut
Materials behave differently during the machining process based on whether they’re being cut on the waterjet, fiber laser, or CNC router.
Composites are better cut by waterjet because when they are cut on the CNC router, it creates toxic dust that’s harmful to our operators. Cutting these materials on the waterjet is safer and cleaner for our shop operations.
Thick materials are cut on the waterjet because the fiber laser can’t consistently cut through them without dross buildup or an acceptable edge quality. If we cut thick metals on the waterjet, the edges will be clean, consistent, and free of dross and burr.
Benefits of Waterjet Cutting
Because of the speed and cut quality the waterjet affords, all of our composite parts will see a general decrease in cost. Waterjet is between 2 and 3 times faster than CNC routers at cutting composites, and less time on the machine means the parts cost less to manufacture.
The consistency in waterjet cutting means it’s less likely for an issue to arise during machining that causes your parts to need recut. Since this is the case, your parts will be finished consistently faster.
The edge quality and lack of dross or burr on waterjet cut parts also means that there is less post processing needed to make your parts look great!
Design Can Affect the Choice of Machining Method
Sometimes there are exceptions to the materials we cut on the waterjet versus the laser or router. If your design has a particularly tight radius or square internal corner, we will choose not to cut it by waterjet as the minimum radius for waterjet is 0.030-0.040”.

If there are small holes, especially tapped ones on the part, we will cut it by waterjet for the sake of consistency. With a stream size of 0.032” and a minimum internal geometry size of 0.070” as compared to the router’s minimum bit size of 0.125”, waterjet is significantly better at consistently cutting small geometry than the routers.
Other Waterjet or Laser Cutting Considerations
At this time, we are choosing what materials to cut on the laser, waterjet, or CNC router for you. There are a few things we take into consideration when making this decision:
- The edge quality and lack of dross or burr in waterjet cutting
- Waterjet cutting does not generate HAZ
- Less taper on thick materials in waterjet cutting
- Tight radii and small geometry are more accurate on a fiber laser
- Laser cutting is an overall faster process than waterjet cutting
If your parts are being waterjet cut, consider whether or not you’ll need to have them deburred. Because parts are less likely to need deburred if they’re waterjet cut, you won’t have to make sure they fit within our deburring minimums. And since waterjet cutting takes a bit longer than laser cutting, cutting out the extra 1-2 days of lead time that deburring adds to your order would be beneficial.
There are a lot of tolerances we keep in mind when choosing between waterjet or laser cutting, and both machining processes have their values and drawbacks. We’ve chosen the machining method that’s best suited for your chosen material and design, but if you have any questions about how we came to these conclusions, just reach out to our support team!
Ready, Set, Waterjet!
SendCutSend is constantly pushing the envelope in this industry to make machining more accessible and affordable. That’s ultimately the goal with adding new machining technologies to our own machine shop, and waterjet cutting brings value to the areas that laser cutting and CNC routing lack. While we utilize each machining process for unique applications, putting all these methods together allows us to offer you better lead times, better prices, and higher quality parts.
We can’t wait to waterjet cut all your awesome designs. Check out our waterjet cutting guidelines and get ready to upload your design today!