*This article was last updated on February 24, 2023
Here at SendCutSend, we account for the kerf in every single cut so you never have to worry about it. But it’s still important to understand “What is kerf in laser cutting?”
When a laser cuts through a piece of material, the laser’s own width displaces a little extra material than is specified in the original design. The amount of material that is burned away is known as the kerf in laser cutting.
What is the Laser Kerf Width?
The size of the kerf depends on the laser being used and the material being laser cut. At SendCutSend, we use multiple, high-power (4kW to 12kW) fiber lasers, as well as a fleet of low-power CO2 lasers. Fiber laser kerf ranges from .006″-.040″ (.152mm-1mm) depending on material thickness, and CO2 laser kerf ranges from .010″-.020″ (.254mm-.508mm).
We also use high precision CNC routers, and the router kerf is equal to its tooling (bit) diameter. Typically, .125″ (~3mm) is the smallest bit size we offer for materials that are cut using our CNC routing services, such as UHMW, polycarbonate, and plywood.
The reason that we aren’t specific about exact kerf width for each material is because we compensate for kerf in real time, as we’re cutting. Kerf not only changes in each material, but it changes based on cutting geometry, assist gas, beam power, and a dozen other factors. The point is, if you are using SendCutSend, you don’t need to compensate for kerf in your design.
Why is Laser Cutter Kerf Important?
Before SendCutSend, it was important to know the exact kerf so that designers could compensate for it during the design process. We’ve made that obsolete. Well, mostly obsolete. It’s still important to be aware of kerf in one area: intricate and detailed designs.
Since the laser kerf (or CNC tooling) burns some part of the material away, it can alter the detail of the design you are cutting. If a design has a lot of small geometry, these details can be lost because the laser is cutting more material than your design accounted for. This is why there are some limitations to the detail you can include when laser cutting an object. Designs that have features or cutouts smaller than the kerf width (.008” to .040”, depending on the process and material) will be lost. Keep this in mind when you are thinking through the level of detail you include in a part.
Parts with simple geometry such as industrial parts, panels, and brackets are less likely to experience issues with kerf since they typically lack features smaller than the beam (or tooling) width. Smaller, more intricate pieces like jewelry are more likely to have problems with kerf. This is also one of the reasons why we have a minimum part size.

Which Materials Are Less Likely to Experience Laser Cutter Kerf Issues?
The size of the kerf in laser cutting is related to the material being laser cut. For example, metal can withstand the laser’s heat better than wood, so laser cut metal typically has a smaller kerf (.006” to .015”, depending on the alloy and thickness). In wood and plastics, more of the material is physically burned away since the material is flammable. This results in a larger kerf (.010” to .020”).
When working with thicker wood or plastic that is cut with our CNC routing services, the kerf is equal to the tooling diameter. Here at SendCutSend, our smallest cutting tooling is .125” or about 3mm.
Each material will have a unique kerf even if the manufacturing happens on the same machine. Materials like brass and copper that are cut with a fiber laser will likely have a larger kerf than steel. Because each alloy reacts slightly differently to the laser beam, we have to calibrate our equipment for each new material that we stock in order to develop algorithms to maintain accurate kerf compensation.
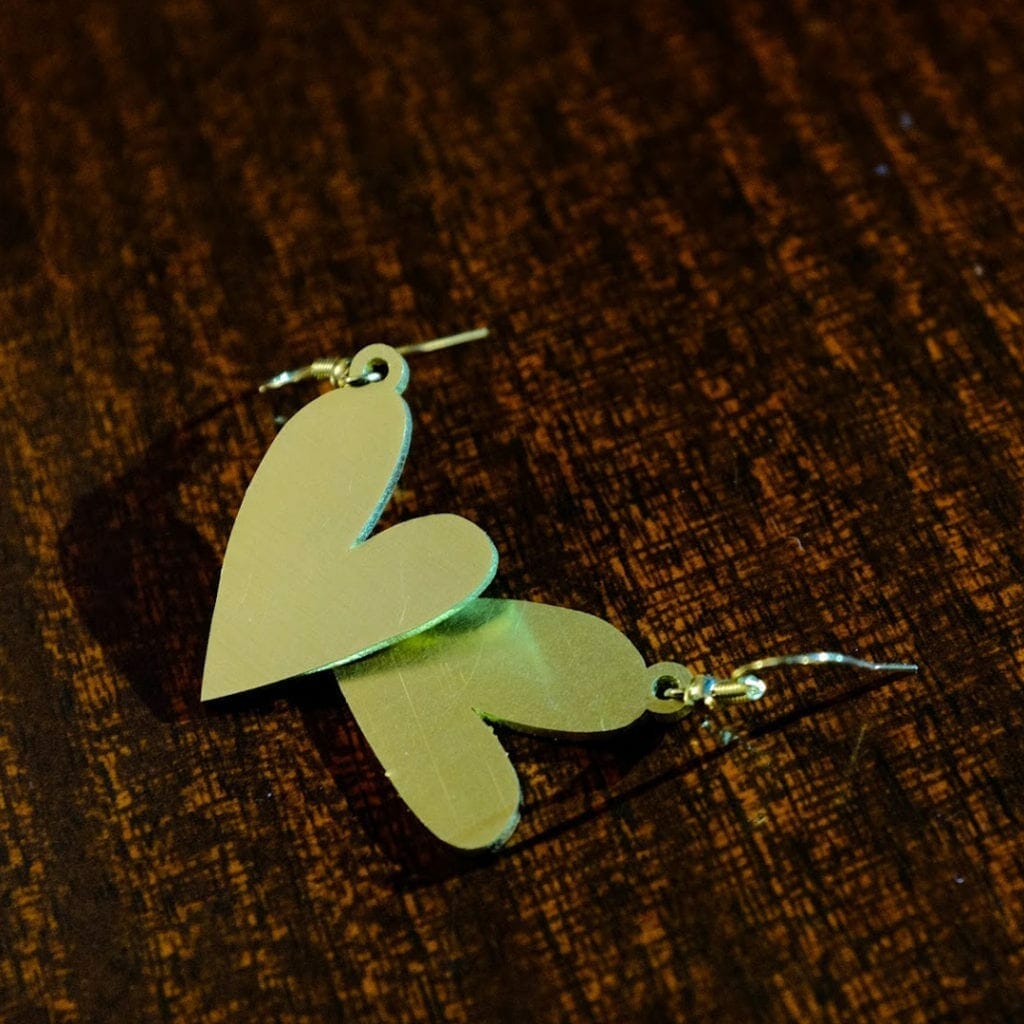
Do I Need to Worry About Compensating for Kerf in Laser Cutting with SendCutSend?
Kerf compensation can happen in a number of ways, though the technical definition is the adjustment of the laser while cutting to minimize the effect kerf has on your laser cut design. On the machine, we offset the centered path of the laser to compensate for the additional material removed by the kerf. The laser will cut wider than the specified line of the part by exactly the width of the kerf in order maintain the integrity of the original part size.
So in short, no you do not need to compensate for kerf in laser cutting! We’ve invested thousands of hours in software and hardware development so that you really don’t have to worry about a thing; we take care of it all! It’s still good to be aware of the kerf in laser cutting and how we at SendCutSend handle it all. Your design is in good hands!

SendCutSend provides low cost laser cutting services across the US. If you’re looking for laser cutting near me consider our online laser cutting services which provide fast turn-arounds and parts to your door in just a few days. If you have any questions about kerf and how it could impact your design feel free to explore our instant pricing tool and contact us.