Understanding the complexities of DFM for sheet metal bending can help designers and operators avoid common issues that arise when transitioning a design from concept to production.
In this post, we discuss essential guidelines to ensure successful bends, minimize errors, and avoid costly collisions.
Sheet Metal Bending: What to Avoid for Better Results Video Guide
Key Concepts of DFM for Bending
In bending, DFM is the process of designing parts to accommodate manufacturing constraints. Because bending is inherently complex, it requires precise tooling, alignment, and clearance. At SendCutSend, DFM starts as soon as a part is uploaded to our system, where both software and human expertise assess feasibility.
Here’s a look at some of the major considerations:
1. Collisions: part vs. machine in DFM for bending
A common challenge in bending involves avoiding collisions. A collision can occur if:
- The part collides with itself during bending.
- The part collides with the machine or tooling.
Long flanges and narrow channels often cause parts to hit the machine’s punch or other tooling, halting the process. In some cases, redesigning parts with adjusted flange lengths or using smaller tooling helps maintain clearance and avoid collisions.
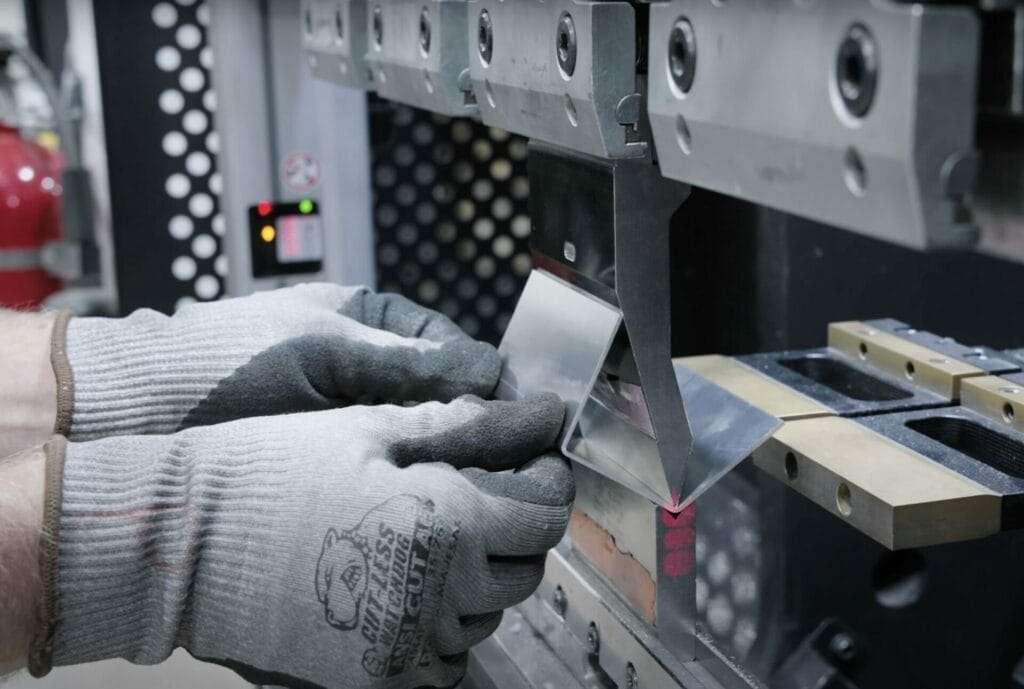
2. Corner clearance and bend relief
Corner clearance is vital to avoid distortion or cracking. When corners lack adequate relief, they resist bending, which can cause fractures. Adding small relief cuts can facilitate a smoother bend and prevent material stress.
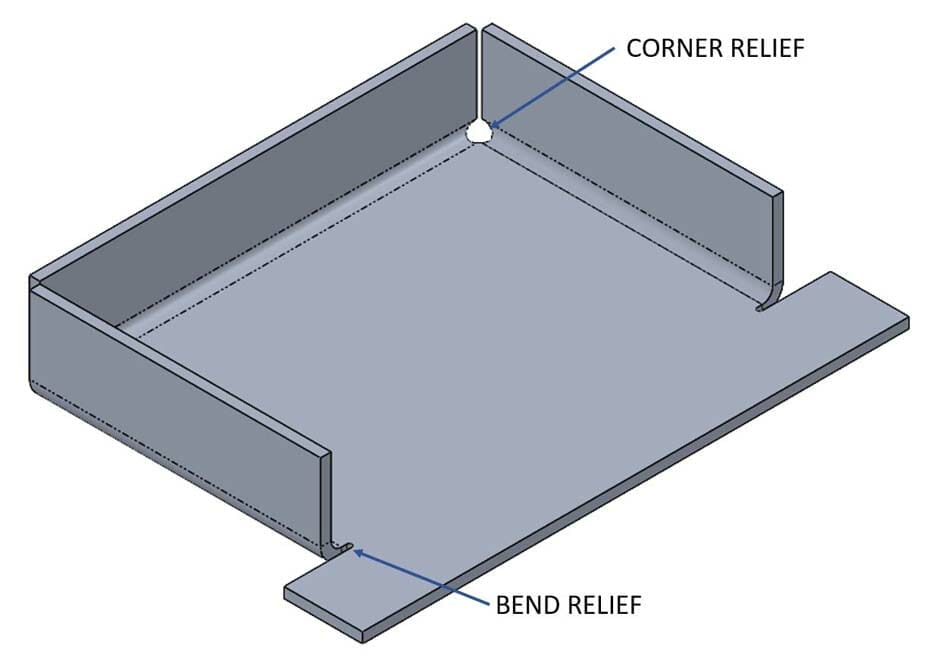
For instance, leaving space around corners and edges gives material room to flex without cracking. Bend relief, or slight cuts at bending points, helps avoid distortion in these high-stress areas.
3. Distortion prevention in DFM for bending
Distortion is a frequent issue when holes or features are positioned too close to the bend area. Without careful planning, holes can deform, making threading or fastening impossible post-bend. You can adjust hole positions in relation to the “die line” to avoid these problems. When designing, avoiding placing holes within the primary bend area will help prevent distortion on your bent parts and ensure the part maintains its intended function.
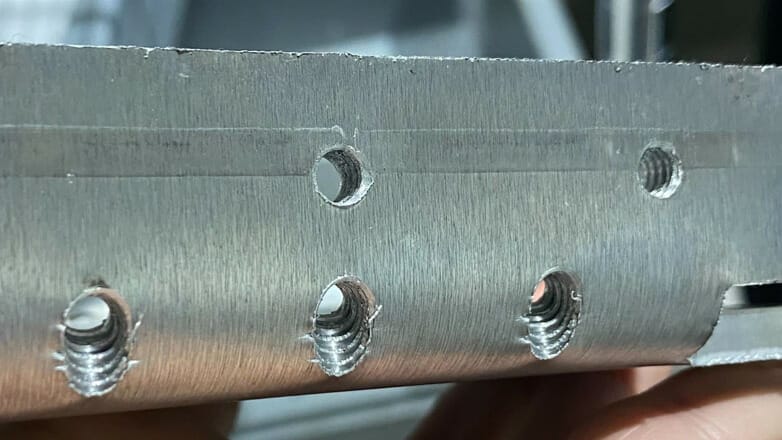
4. Flange and part alignment
Uneven flanges can lead to misaligned parts. To counter this, you can add support features like break-off tabs to ensure flanges bend evenly. Parts with non-parallel lines to the bend point also pose challenges, as they lack an alignment reference. For accurate results, designers should add a parallel edge for support, so the part maintains its intended shape and alignment during bending.
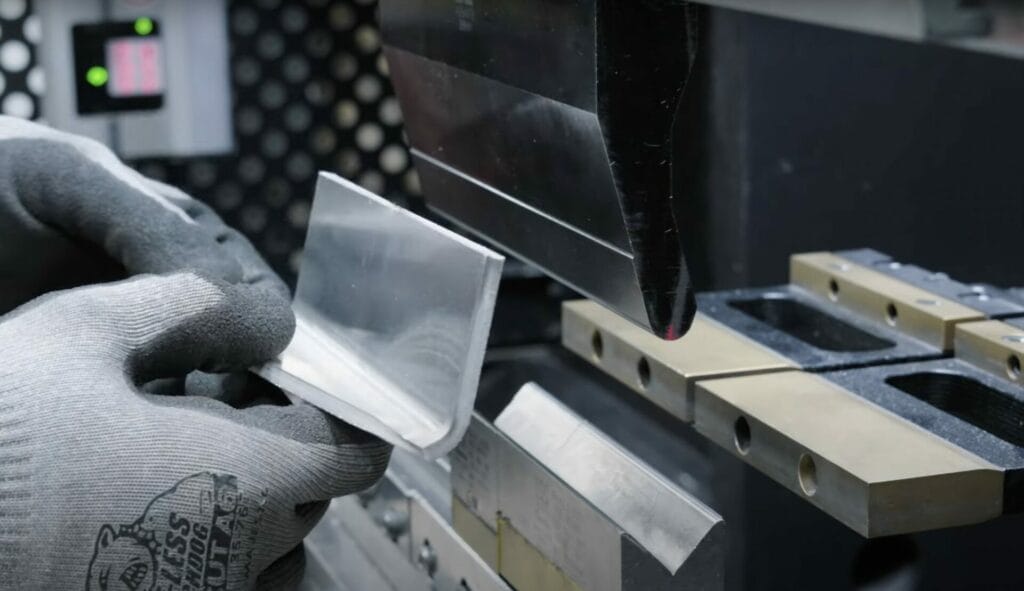
5. Short flanges: Understanding minimum bend requirements
Short flanges can’t span the die and punch, making bending unfeasible. To address this, you can consult SendCutSend’s material-specific guidelines that detail minimum flange lengths, bend radii, and tooling configurations. Keeping these in mind while designing will prevent issues like flange misalignment or tool clashes.
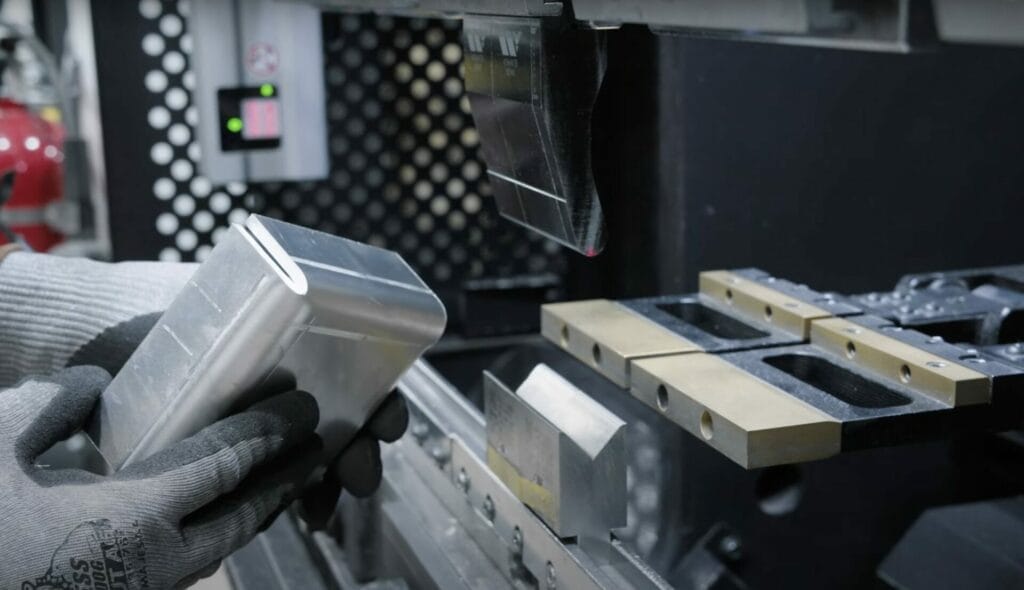
DFM for bending success with SendCutSend
Our automated software gives instant feedback, flagging issues like hole distortion or short flanges. However, with the variability in bending, human review remains essential. Our DFM team provides hands-on insights, evaluating unique cases and advising on design modifications for optimal results.
DFM for Sheet Metal Bending Final Thoughts
Bending in manufacturing requires a fine balance between design innovation and practical application. Following DFM guidelines, adjusting designs based on tooling capabilities, and proactively seeking DFM support ensures that complex bends remain accurate and production-ready.
For more advanced tips or to discuss specific design challenges, contact our Support team or tune in to future episodes of Cutting Corners.