Machining processes have come a long way in recent years, with fiber lasers and state-of-the-art waterjet cutters making sheet metal fabricating a fast and affordable process. However, no matter what machining process is used, parts will usually have some amount of burr, dross, or leftover imperfections immediately after manufacturing. Trying to figure out how to deburr your parts without compromising their tolerances or final look is a challenge in and of itself, so let’s talk about the different sheet metal deburring processes available, what we use here at SendCutSend, and how to best prepare your designs for going through deburring.
What Causes Burr and Why Is Deburring Important?
Burr and dross are imperfections that appear on cut parts chiefly during the machining process. Dross is buildup that occurs when the laser melts the metal and it clumps at the edge of the cut without falling off. Burrs are little pieces of metal that chip and curl up around the edge of the part during cutting. These buildups can cause dangerous edges, parts that are out of spec, and general annoyances during the assembly process, so it’s important to have them removed. Luckily the deburring process is simple and fast, and can easily remove the imperfections.
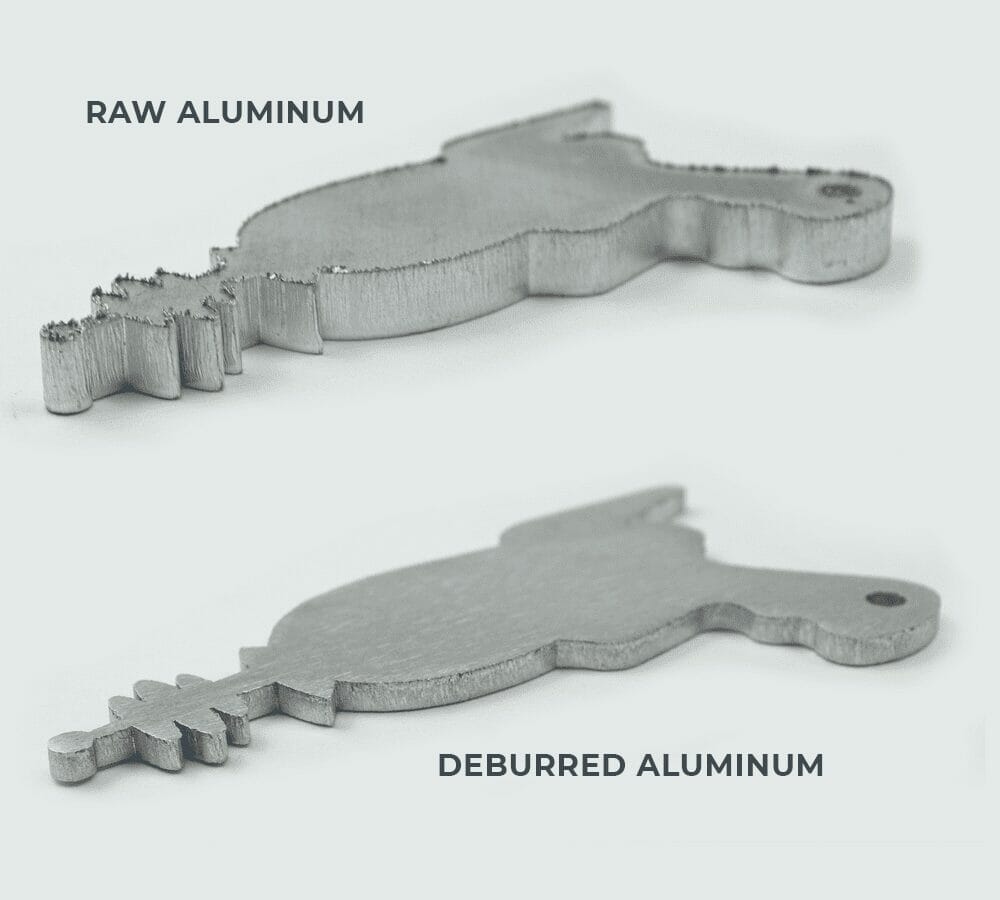
The removal of burr is crucial for safety, aesthetics, and part functionality. The sharp, uneven edges on cut edges with burr can cause injury during assembly or use. Beyond safety concerns, deburring plays a vital role in enhancing the overall aesthetics and usability of products. Burr-free surfaces contribute to easier assembly and reduced friction, ultimately leading to better part performance and end success. In industries where precision and reliability are key, such as aerospace, automotive, and electronics, deburring prevents interference with delicate components and ensures precise fits. Overall, the process of deburring is an important step in the manufacturing chain for most parts, fostering safety, functionality, and quality.
It’s important to note that not all parts will require deburring and not all parts are eligible for deburring with SendCutSend. Just as it is with any of our manufacturing processes, parts have to meet certain minimum and maximum requirements in order to be deburred. We do not deburr non-metal parts here at SendCutSend, although some plastics and composites can still experience burr buildup during the machining process. Another important thing to note is that delicate designs cannot go through most deburring processes as the designs can break away and get lost in the process. If you select deburring for your parts, the design should be robust and the thickness of the metal should not be susceptible to bending or warping. These recommendations are laid out in our deburring guidelines.
How Do Deburring Processes Work?
There are a huge variety of ways to successfully deburr a part. In some cases, you may choose to deburr a part by hand if the part is particularly small and delicate or you’re not looking for precision. In this case, you would use a rotating hand deburring tool found in pretty much every machine shop.
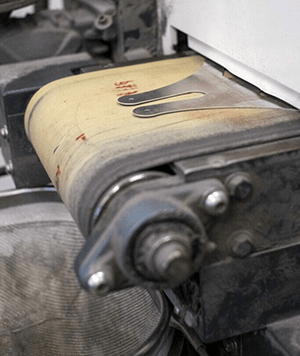
But if your parts are on the larger side and you don’t want to spend time deburring them yourself, using automated deburring processes is the way to go. The most common processes use abrasive heads or belts to “scrub” the part clear of any large pieces of burr as the part moves on a conveyor. Some deburring processes will use abrasive media to blast the edge of the part and remove burr and dross buildup, or tumble the part with the abrasive media to give it a softer edge and finish.
The important thing to know about how deburring processes work is that all deburring processes are relatively gentle. They are designed to remove burr and dross, and nothing else. Deburring will not polish your part or give it a finish, and it will not remove scratches or surface level imperfections. Deburring is meant to do one thing and it does that very well! So if you’re looking for a beautiful finish on your part, we recommend adding one of our finishing processes such as plating or powder coating.
Wet vs. Dry Deburring
Fundamentally, there are two different classes that deburring systems can fall under: wet or dry.
Deburring using a dry process involves the use of an abrasive to remove dross and burr from the sharp edges of a recently laser or waterjet cut part. Dry deburring machines use a variety of abrasive materials including discs, belt heads, and brushes. Different abrasives achieve different finishings depending on their orientation in the machine and the metal they are deburring. Dry deburring is one of the more environmentally friendly deburring processes as it contains no lubricant or added waste apart from the dust created by the removal of the burrs themselves. However, it can also be dangerous due to the increased likelihood of a fire starting from the dry metal shavings and friction created during the deburring process.
When deburring parts using wet systems, the parts are fed through a conveyor belt and sprayed with a lubricant and cooling solution. Wet deburring machines utilize abrasive heads or belts placed above the conveyor. The pressure on the part between the conveyor and the abrasive head holds the part in place while the abrasive head removes burr, light scratches, and performs edge rounding. Wet deburring is much safer for human operators and shop environments as the lubricant keeps dust and shaving levels low, keeping the air clean and free of debris. It can be difficult to dispose of properly, so it’s important that shops maintain and dispose of their deburring waste ethically and use environmentally friendly lubricants.
Benefits of Wet Deburring vs. Dry Deburring
Wet deburring is the deburring process of choice here at SendCutSend for the numerous benefits it provides to parts, machine upkeep, and our machine operators. There are many reasons to choose wet deburring over dry deburring, but some of the most important include:
- Heat Prevention: Liquid coolant in wet deburring systems prevents overheating of metal and debris during processing, avoiding the creation of an explosive environment caused by friction, metal, and dust in dry deburring.
- Metal Compatibility: Wet deburring is essential when working with different metals to prevent potential explosions due to metal combinations heating up, e.g., iron oxide and aluminum oxide forming thermite.
- Prevents Warping: The coolant used in wet deburring prevents parts from warping under intense heat, preserving the original part’s integrity and minimizing heat-related distortion.
- Consistent Finish: Wet deburring ensures a more uniform finish compared to dry deburring by evenly distributing abrasive media’s effects, resulting in a smoother and more precise surface.
- Abrasive Media Longevity: Wet deburring promotes longer life for abrasive media due to lubrication and cooling, reducing the frequency of belt or brush head replacements compared to dry deburring.
- Speed and Efficiency: Wet deburring can be faster than dry deburring in some cases, as it can apply greater pressure on the part without causing warping or introducing heat, resulting in fewer passes and quicker completion.
- Cost Efficiency: Despite higher initial investment, wet deburring’s faster processing and reduced need for replacements make it cost-effective in larger-scale operations.
- Quality and Aesthetics: Wet deburring helps maintain parts’ appearance and cleanliness due to the possibility of using a coolant that protects against corrosion, ensuring well-formed parts.
- Outsourcing Option: Manufacturers can outsource wet deburring, allowing access to its benefits without the need for significant in-house equipment investments.
- Safety Enhancement: Wet deburring’s lubricant application enhances safety by minimizing the amount of dust and debris in the air, protecting operators from breathing in harmful particles and minimizing their skin-to-skin contact with irritants.
Wet deburring has its drawbacks, of course, but there are ways to minimize them. One of the greatest disadvantages to wet deburring over dry deburring is waste disposal because the use of liquid coolant and lubrication creates a “sludge” that has to be dried or packed in drums for disposal. The environmental impact of wet deburring machines can be minimized with eco-friendly lubricant, which can be disposed of via a sewer connection. In addition, many wet deburring machines utilize a “recycling” process wherein the metal debris is filtered out of the lubricant and coolant, and run through the machine for another use. This drastically cuts down on the amount of waste a wet deburring machine produces.
We take the greatest care to make sure our deburring waste is ethically disposed of and safe for our operators, making our shop and consequently your parts safer in the process.
5 Considerations and Design Tips for Deburring
If you want to ensure that your parts will go through the deburring process successfully, there are a few things you can do during the design process. All parts must meet the necessary requirements to go through any of our services and processes, and deburring is no exception.
Here are 5 considerations and design tips for deburring:
- Material Thickness: Ensure a minimum material thickness of at least .050″ to make the part eligible for deburring.
- Geometry Consideration: Keep in mind that intricate, fragile, or highly detailed geometries might not be suitable for deburring.
- Material Compatibility: Note that deburring is not available for mild or high carbon steel products, including mild steel, HR, AR500, 4130, 1095, and similar materials. If you need your part to be steel and want it to be deburred, we suggest stainless steel 304 or 316.
- Small Parts: For small parts, adhere to the minimum part size requirement for linear deburring, which you can confirm by material and thickness on our processing part size limits page.
- Large Parts: If dealing with larger parts, consider the maximum overall flat part size for linear deburring. Make sure your part dimensions do not exceed this limit by checking our processing size page or the deburring service guidelines.
If you would like more information on our specific deburring process and how to make sure your parts are ready for deburring, be sure to watch our video guide on our wet deburring process.
Removing Imperfections and Burr Left From the Cutting Process
No matter the process used, deburring can directly benefit your parts and final products. Removing dross and burr ensures a safer, cleaner edge for handling, as well as tighter tolerances and better press-fits. This means that no matter who is using your parts, whether it’s for yourself or a customer, the end result will be easier to assemble and more satisfactory.
If you’re interested in learning more about deburring, check out SendCutSend and our state of the art deburring processes. With additional services including laser and waterjet cutting, CNC routing, powder coating, anodizing, plating, hardware, bending, and tapping, SendCutSend is a one-stop-shop for all your machining and fabricating needs.
Still have questions about sheet metal deburring? Reach out to our support team anytime!