Aluminum alloys are durable, lightweight and corrosion resistant, making them a natural choice for your laser cut projects, but why all the different grades? What can I do with 5052 that can’t be done with 6061, or when should I spend for 7075, and what benefits do I get over the lower grades?
This article will give you a quick intro to our three most popular aluminum alloys, help you choose the right one for your application, and give some insight on how each service we offer will perform. So whether you’re building a fighting robot, yard art, a hobby airplane or any other laser cut part you can dream up, you get the right alloy every time. Let’s dig in!
Introduction to 5052 H32 Aluminum Sheet Metal
The aluminum for the Common Man, with a great balance of durability and affordability, 5052 H32 is easily one of our most popular materials. The addition of magnesium and chromium to the pure aluminum give it superior strength and enhance corrosion resistance, while the H32 temper means that it is ductile enough to be cold worked (we’re looking at you, bending) without cracking. Here’s some more information on this alloy and how you can use 5052 aluminum in your projects. We offer 5052 H32 in 10 thicknesses ranging from 0.040” up to 0.500”.
Introduction to 6061 T6 Aluminum Sheet Metal
The kid with great balance, 6061 is often used in structural components because of its superior strength-to-weight but is still relaxed enough to be cold workable and weldable. This alloy includes a little magnesium and silicon, and the T6 grade means it is heat treated and artificially aged, increasing both tensile and fatigue strength. We’ve written a deep dive into more uses and properties for 6061 aluminum. We offer 6061 T6 in eight thicknesses ranging from 0.040” up to 0.500”.
Introduction to 7075 T6 Aluminum Sheet Metal
When you need the best in strength and toughness, call 7075 T6 aluminum. Significant amounts of Zinc, Magnesium and Copper mean this alloy exhibits durability closer to a Titanium alloy than pure aluminum. Like the 6061 we offer, 7075 T6 is thermally treated in solution, then aged, to maximize hardness and strength. We offer 7075 T6 in 0.125”, 0.190” and 0.250” thicknesses.
Aluminum Properties: 5052 vs 6061 vs 7075
Now that you’re familiar with what aluminum alloys you have to work with, let’s get into how they compare to one another with some real-world criteria. For the TL;DR take a look at this excellent aluminum grade infographic.
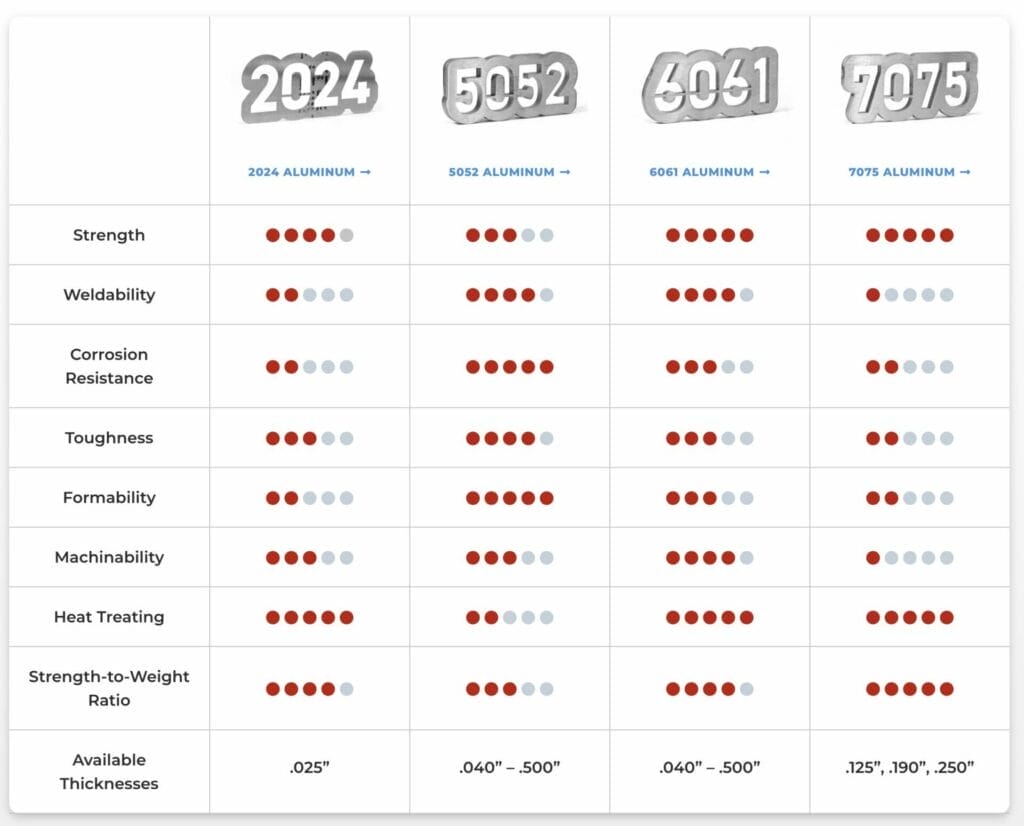
Aluminum Strength of 5052 vs 6061 vs 7075:
Not a measure of who will win the arm wrestling contest; “strength” is a critical property that quantifies the ability of a material to resist an applied load without failure or plastic deformation.
- 5052 aluminum has the lowest strength among the three grades, with a tensile strength of around 220 MPa.
- 6061 aluminum offers moderate strength, with a tensile strength of around 310 MPa.
- 7075 aluminum is the strongest of the three, with a tensile strength of around 572 MPa.
Weldability Differences Between 5052, 6061, and 7075 Aluminum:
When heated, will two pieces of the material stick together at a seam with as much strength as the base metal? See, the strength of a material really does come in handy!
- 5052 has excellent weldability, making it suitable for applications requiring welded joints.
- 6061 has good weldability, but it may require preheating and post-weld heat treatment for optimal results.
- 7075 has fair weldability, and it is generally not recommended for welding due to its susceptibility to cracking.
Corrosion Resistance Differences Between 5052, 6061, and 7075 Aluminum :
All three grades of aluminum exhibit excellent resistance to the effects of air, water and many chemicals.
- 5052 is particularly resistant to saltwater corrosion, making it suitable for marine applications.
- 6061 is also corrosion-resistant and is widely used in architectural and structural applications.
- 7075 is resistant to corrosion in various environments, including exposure to chemicals and harsh weather conditions.
Toughness:
We talking about the bully at the playground? Not quite; toughness measures a material’s ability to absorb energy and resist fracture on impact. Toughness is distinct from strength, which refers to a material’s ability to resist an applied load without deforming or breaking.
- 5052 has high toughness because of its finer grain structure
- 6061 has moderate toughness, as usual it balances ductility and strength
- 7075 has the lowest toughness among the three grades, due to its comparatively high strength and stiffness.
Formability and Sheet Metal Bending Options for 5052 vs 6061 vs 7075:
The ease with which a material can be shaped without cracking or breaking, this is related to toughness, but really a subset of ductility. Basically, can I bend this material without it cracking?
- 5052 has excellent formability, making it ideal for applications requiring bending, shaping, or drawing.
- 6061 has good formability but may require more effort than 5052 aluminum
- 7075 aluminum has poor formability and may require specialized forming techniques.
Machinability:
All three grades of aluminum have good machinability, meaning they can be easily shaped using various techniques like drilling, turning, and milling without exotic tooling.
- 5052 aluminum has the best machinability due to its soft temper.
- 6061 aluminum and 7075 aluminum have slightly lower machinability due to their higher strength, but are typically still machinable with standard high speed steel tooling, due to their comparatively low hardness.
Heat Treating:
Even aluminum feels better after a little time relaxing in a warm place.
- 5052 cannot be heat-treated to further enhance its strength, but is still stabilized after work hardening using a heat-treat.
- 6061 can be heat-treated to achieve higher strength and hardness through the T6 temper (which is what we offer).
- 7075 aluminum can also be heat-treated to achieve various tempers, including our T6, which provides a balance of high strength that still maintains some toughness.
Strength-to-Weight Ratio of 5052 vs 6061 vs 7075:
If you know the strength and the density, you have this number.
- 5052 has the lowest strength-to-weight ratio of the three
- 6061 falls right in the middle again
- 7075 has the highest strength-to-weight ratio, with an ultimate tensile strength of 81 ksi and a density of 176 pounds per cubic foot, it’s ratio is better than that of grade 2 Titanium.
SendCutSend Services Available for Aluminum Sheet Metal
All of the aluminum alloys we offer are cut on our world-class fiber lasers which means the smallest kerf and highest accuracy possible. All but the thinnest grades of 5052 and 6061 are automatically deburred (unless you say otherwise) at no extra charge, which ensures the end product has a consistent, professional, finish.
Most of our other services are also available, but let’s looks at some of the finer points of each:
Anodizing
Think of it as a protective case for your aluminum part: Anodizing aluminum creates a protective oxide layer on the surface which is hard, durable, and even more resistant to corrosion than the raw aluminum. Plus, it looks pretty fantastic in one of SendCutSend’s anodizing color choices of red, gold, blue, black and clear.
- 5052 anodizes well, but the appearance can be slightly more blotchy than 6061
- 6061 yields the best results of the three. Expect consistent, even, coloration.
- 7075 due to the high zinc content and tendency to form a porous oxide layer, it’s more challenging to anodize this alloy well. Visually, this translates to odd coloration on the edges and inconsistencies throughout.
Tapping and Countersinking
These services are offered on all grades with sufficient thickness. To check on eligibility for a specific service, scroll down to the Material Details on the Materials page for each alloy. Since we have set up tooling specifically for each aluminum grade, you can expect great results from SendCutSend countersinks and taps, but be aware of these general guidelines:
- 5052 challenging to tap because of its relative softness, tapping can cause galling if it’s not done properly and with lubrication
- 6061 is the best alloy when it comes to tapping, with consistent results easily attainable.
- 7075 taps well, but because it’s harder and more brittle, not as well as 6061.
Powder Coating Service for Aluminum Sheet Metal
Not your average rattle can paint job, powder coating is a dry finishing process that creates a durable coating able to withstand scratches, abrasion, and weathering. It is also resistant to many chemicals and solvents.
We offer powder coating in several colors and finishes on all three alloys with great results.
Hardware
We have it on good authority that press-fit fasteners are better than a Swiss army knife when it comes to versatility. Whether you need a nut, stud, or standoff, all three grades of aluminum can be ordered with fasteners.
- 5052 Because it’s ductile, or can handle a lot of plastic deformation before failing, this is the best aluminum grade for a consistent press fit of the fastener.
- 6061 still happy with fasteners, but requires a little more force and care
- 7075 its T6 temper, and the high ratio of alloying elements mean 7075 doesn’t hold/clench the hardware as well as the other grades.
Tumbling
Perfect for parts as small as 0.5” x 1.5”, tumbling aluminum parts knocks off burrs and sharp edges, while evening out the look and smoothness of the top and bottom surfaces. Check out our Guidelines for Tumbling for more info.
Design Services
Have a killer part design, but it’s been sitting on the back burner because you don’t have the software (or the time) to convert it to digital and upload to our app? We have a service for that! Let our team convert your paper dimension drawing, or scan the physical template, and we’ll send you a link to order in whatever material works best for your application.
Applications for 5052, 6061 and 7075 Sheet Metals
5052 H32 Aluminum Sheet Metal Applications
Known for its excellent corrosion resistance and formability. It is commonly used in marine applications, such as boat hulls, fittings, and piping. Although it doesn’t have the high strength of 6061 or 7075, because of excellent weldability, it’s often found in aircraft components such as fuel tanks and cowlings. On the hobbyist end of the spectrum, that corrosion resistance means it can be used outdoors, even in salt water conditions, with minimal surface protection.
6061 T6 Aluminum Sheet Metal Applications
Also formable and weldable, but that heat treatment gives it 32% higher ultimate strength than 5052, so you’ll find 6061 in more strength-critical applications such as bridges, aircraft frames, and machinery. If you’re looking for the goldilocks ratio of workability and strength for your parts, look no further than 6061.
7075 T6 Aluminum Sheet Metal Applications
Best when you need strength that can compete with steel or titanium at a fraction of the weight. 7075 is common in aerospace applications, high end vehicle and bicycle frames, and sporting equipment. Consumer electronics like laptops and phones often use 7075 in the chassis and heat sink components where low weight and high strength/thermal conductivity are important.
Wrapping Up Aluminum Alloys
Armed with this comparison info, and all the value-added services available for any one of these aluminum alloys, we hope you have everything you need to upload your next part file to our app and get started with that next build! If you have any specific questions, you can always contact our amazing support team any time.
FAQs for SendCutSend Aluminum Alloys
Why can’t you bend 6061 and 7075 sheet metals?
Although 6061 is cold-workable, we don’t currently bend it because it requires special tooling with larger internal bend radius requirements and can be tricky at larger die ratios.
Alloy 7075, particularly in the T6 heat treatment, was designed for maximum hardness, rather than workability, so it’s almost never a good idea to bend it at anything approaching a typical sheet metal bend radius.
What are the quick-takeaway strengths of each material?
5052 is best for all-around, affordable fabrication, welding and corrosion resistance.
6061 is very strong and is a great option when bending isn’t required but welding is.
7075 is not really weldable, so it is great for individual components that require high strength.