If you’re looking for an aluminum laser cutting service, we cut four different types of aluminum: 2024 T3 aluminum, 5052 H32 aluminum, 7075 T6 aluminum and 6061 T6 aluminum. However, the best all around option is our 6061 T6 aluminum which is much stronger than our 5052 H32, while being more corrosion resistant than 7075 T6, and it’s also the most electrically conductive aluminum grade we offer.
This article will introduce you to its properties, a few of its many applications, its strengths, and whether 6061 is the best choice for your next aluminum laser cutting project.
What is 6061 T6 Aluminum?
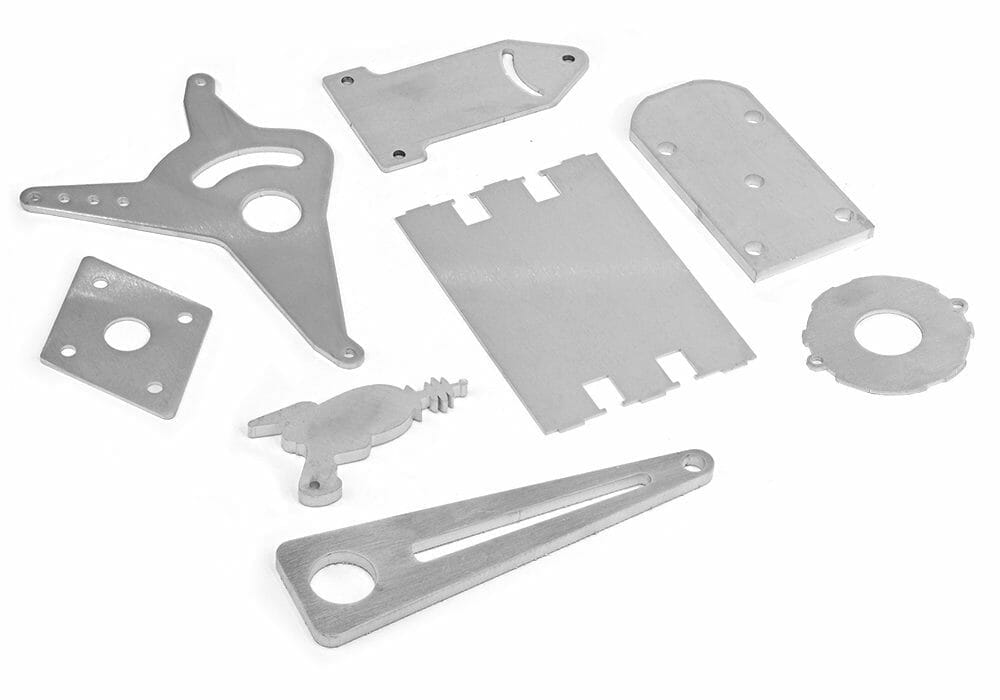
6061 T6 is one of the most common grades of aluminum used in the market today with good reason: its T6 temper nearly quadruples the typical yield strength compared to annealed (O temper) 6061. Being a heat-treatable alloy, it is also significantly stronger than something like 5052, our other weldable aluminum grade.
Unlike some super-high strength/hardness aluminum alloys such as our 7075 grade, 6061 is at the same time less brittle, meaning it maintains much better formability and machining characteristics.
Due to its strength, 6061 is often found in structural applications such as high performance frames, stairs, and ladders (think, fire truck ladder). 6061 also has best-in-class corrosion resistance, as this attribute typically decreases as hardness and heat treatment become more extreme, which allows it to be used in marine environments where its extra strength is called for over using 5052 aluminum.
Specifications
Being part of the 6xxx series means that 6061 aluminum’s primary alloying elements are magnesium (1.0%) and silicon (0.6%), while the balance is made up by Iron (Fe), Copper (Cu), Chromium (Cr), Zinc (Zn), Manganese (Mn), and Titanium (Ti) with trace residuals.
It is the “T6” designation that really contributes to this alloy’s mechanical properties. The “T” means that 6061 T6 undergoes a solution heat treatment in which it is thermally treated, then artificially aged. To accomplish this, as-rolled 6061 is raised to 350°F for eight hours, then subjected to a controlled air cooling. This greatly increases its tensile and fatigue strengths. Even though 6061 is a great choice for aluminum laser cutting services, it isn’t the best candidate for bending applications, as at this temper it is susceptible to cracking under plastic deformation. If you plan on adding bending to your laser cut parts, we recommend 5052 aluminum.
Finally, with 60%+ of the conductivity of copper, 6061 has the best electrical conductivity of any of our aluminum alloys. This means that 6061 T6 is a solid candidate for electrical power transmission, as long as flexibility (think, aluminum electrical cable) is not necessary. In those cases where flexibility is important in the electrical conductor series 1xxx and 8xxx alloys are typically employed.
Appearance
Unless you’re a seasoned machinist used to working with different aluminum grades, it will be hard to tell our various aluminum alloys apart. In general, 5052 has a slightly smoother appearance than 6061, but once your parts are deburred, they all take on a spiffy brushed appearance.

If you prefer, you can opt out of deburring if you plan to polish the parts later. Note that bend and hardware insertion marks will be visible in the final part, since these services happen after deburring the flat sheet.
SendCutSend’s 6061 T6 Aluminum Laser Cutting Service
SendCutSend’s fiber lasers have a dimensional tolerance of +/-0.005” or better, and are our cutting tool of choice for any compatible material, including all thicknesses of 6061 T6. Fiber lasers also have a kerf that typically comes in under 0.01” wide, meaning that even in a ½” plate, it’s possible to cut holes as small as 0.170” diameter without burn-through in the surrounding material.
Much more information on minimum and maximum part size, bridge size, hole-to-edge size, slot tolerances, etc. can be found listed by material thickness on our 6061 Material Page.
What SendCutSend Services are Available for 6061 T6 Aluminum
6061 T6 is currently offered in 8 different thicknesses from 0.040” up to ½” plate. In addition, we offer other useful services including:
- Deburring: Available, and automatically applied to all thicknesses 0.063” and up. Opt out if you’d rather not have the brushed appearance but know that there may be a burr on the underside of the part.
- Countersinking: All thicknesses ⅛” and up can take a countersink.
- Tapping: Material with a thickness of 0.063” and up can be tapped.
- Hardware Insertion: Whether it’s a stud, and nut or a standoff, hardware insertion of some kind is available for nearly every thickness of 6061.
- Anodizing: Available in various bright colors, anodizing looks great and adds another protective barrier in addition to the native aluminum oxide, both from the elements and wear.
- Powder Coating: Powder coating adds a strong, colorful (or black), smooth (or textured) finish. It’s great for applications where maximum durability is the goal.
Check out our Minimum/Maximum Part Sizing Guidelines to confirm the flat part size limitations for all our services in each material and thickness.
Strengths
Strength to Weight Ratio
While other high-temper aluminum alloys also possess this attribute, 6061 is kind of in a “sweet spot” when it comes to balancing things. Thanks to its heat-treatability it is significantly stronger than non-heat treatable alloys such as 5052, which has a yield strength of 26 ksi vs. 6061’s 39 ksi for instance. Because of this, a thinner piece of 6061 can typically be used in the same application, yielding a weight (and often cost) savings.
Machinability and Malleability
In this category, 6061 also finds itself in the “goldilocks” category. While it isn’t as malleable as 5052, that works in its favor for operations like milling or turning because 6061’s metal chips come off more cleanly on the cutter. On the other end of the spectrum, when compared to a super hard alloy like our 7075 T6, 6061 wins the machining comparison because of its lower hardness, making it faster to mill with less likelihood of tool breakage.
Corrosion Resistance
6061 possesses excellent corrosion resistance, particularly for a higher-temper alloy, due to its relatively low copper content (0.15 – 0.4%). This means that without any additional protective barrier, it can be used for marine components, vehicle frames, and other exterior structural components.
Electrical/Thermal Conductivity
Although at 60% the conductivity, it doesn’t initially seem obvious why 6061 would often be used rather than a copper alloy, 6061 is significantly less expensive, more corrosion resistant, and less than a third the weight of copper. Choose 6061 for things like aluminum laser cutting services for busbars.
Because it’s also thermally conductive, 6061 makes great heat sink material either as a dedicated thermal block, or as an electrical sub-panel for high-power electrical components.
Weldability
Arguably the best choice for high-performance aluminum weldments, 6061 is easily welded using either a MIG or TIG setup. Like other aluminum alloys, 6061 requires careful surface prep just prior to welding, and good control of environmental and shielding gas humidity. For parts that will be heat-treated after welding, use a 4043 filler rod, which has a higher silicon content and generally flows a little better. If anodizing is in the picture, stick with something like a 5356 filler rod, which will anodize properly, producing a silver color naturally.
Weaknesses
Heat Tolerance
Aluminum just can’t take the heat, and 6061 is no exception, with a melting point even lower than that of 5052 (around 1080°F in this case). Since you can hot work 6061 starting at around 500°F, care must be taken with parts made from it anywhere approaching that temperature. This is one of the primary reasons Titanium is chosen over aluminum oftentimes in temperature-critical applications; it’s hard to argue with its 3000°F melting temp.
Bending
Although 6061 is by no means brittle, its heat treatment to a T6 temper makes it less ductile than most bending applications prefer, requiring a bend radius of 3-4x the material thickness for ¼” plate vs. just ½-1-½x the material thickness for our 5052 H32 grade. Because of this we don’t offer bending for 6061.
6061 T6 Aluminum Laser Cutting Service Common Uses
Because it balances the strength of 7075 aluminum with the malleability of 5052 aluminum, we like to think of 6061 aluminum as our middle of the road aluminum alloy, but far from being a compromise, it’s more of a great balance. That’s why so many industries choose 6061 T6 whether the final product is a high-performance fly fishing reel, or the tubing on an aluminum race bike.
Because it’s also extremely vibration and corrosion resistant, automotive components including chassis parts, sheet metal, and engine components are also good applications for 6061.
Not just for structural applications, with aluminum seeing heavy use is the electrical generation and transmission industries, including in capacitor windings, heat sinks, semiconductors and transformer enclosures for over 50 years, it is a proven “reliable material” for any electrical project you might think to tackle using aluminum laser cutting services from SendCutSend whether that’s a set of custom busbars, an aluminum sheet heater, a custom 6061 enclosure sub-panel, or about anything else you can dream up from a flat sheet of 6061 T6 Aluminum.