Heat Wave. Deep Heat. Heat of the Night. While heat might be a good thing to sing about in a rock and roll song, it’s something to be avoided in most metalworking operations, especially sheet metal laser cutting. That’s because, as with many things in life, too much of it can be a bad thing.
Heat leads to HAZ, an acronym for heat-affected zone. A metallurgist will explain in mind-numbing detail that HAZ is an area of metal that has experienced degradation of its internal microstructure after being exposed to high heat. This causes surface discoloration, as seen in the pretty rainbow pattern found in many welded or plasma-cut workpieces. It also weakens the metal, which can lead to cracking.
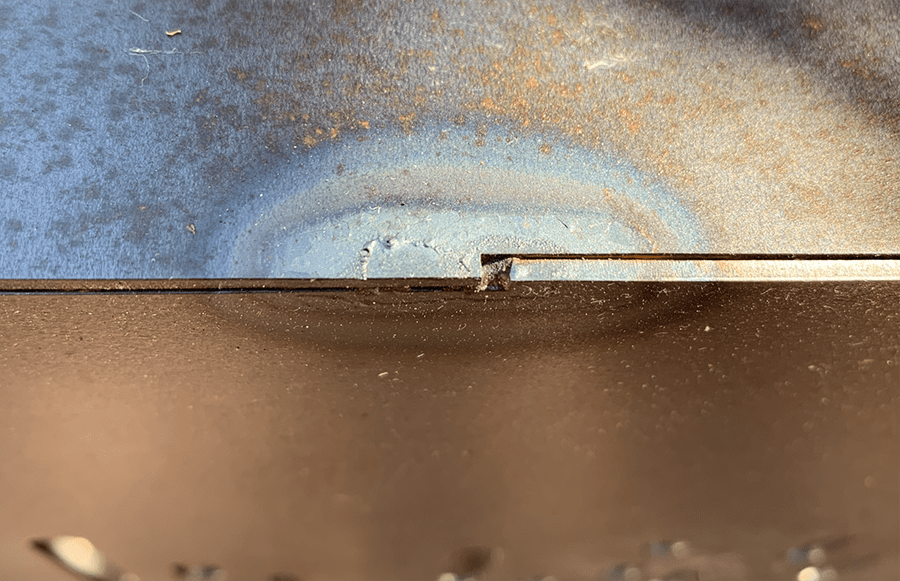
It’s for this reason that an aircraft engineer will tell you it must be avoided at all costs, as HAZ in turbine blades has been linked to engine failures during flight. HAZ’s negatives aren’t limited to flight-critical components, however. HAZ produces local hardening in some metals. It makes them more difficult to weld or bend, as well as more brittle (through a process known as hydrogen embrittlement) and less corrosion resistant.
The Downside of HAZ in Sheet Metal Laser Cutting
Solution annealing can help. This is the process of heating a metal to a specific temperature and holding it there long enough for the crystalline structure within to reorient itself, although this is not always practical nor affordable, especially on larger workpieces. The bottom line? HAZ should be minimized on any mechanical or structural components whenever possible.
So how do you do this? For starters, HAZ most often occurs during welding, although, as already mentioned, plasma and especially oxy-fuel cutting are also culprits. Simply put, the higher the temperature and the slower the speed, the greater the amount of HAZ. This is why laser cutting is the least HAZ-inducing of all thermal cutting processes. More on this in a moment.
If HAZ is entirely unacceptable, shearing is an option, albeit for square and rectangular shapes in thin-gage metals. Punching and nibbling work as well, although here again, the geometry and material thickness is limited. Waterjet cutting is an excellent choice, especially on very thick materials. Fortunately, when you upload your designs to SendCutSend we choose the best cutting method for your project based on material, thickness, and design.
Beaming up
This brings us back to lasers and waterjets. Lasers cut quickly and cleanly. They use a relatively small beam diameter that minimizes the amount of heat transferred to the adjoining areas. Of all the thermal cutting processes—plasma, oxy-fuel, and laser—it’s the latter that creates the least amount of HAZ, while also being the most accurate and, in many cases, the most cost-effective.
Waterjet cutting is the method of choice for difficult-to-process materials. Although we love laser cutting, waterjet is the best way to cut composite materials, eliminating delamination, rough edges, and HAZ. When your parts are waterjet cut there’s virtually no HAZ (heat-affected zone).
How the parts are laser cut also plays a role in part quality. Look for a laser cutting service that uses high-purity nitrogen for the cleanest, most oxidation free surface possible. Just note that thicker materials may require the use of oxygen as an assist gas, which might mean some edge prep with a wire brush or chemical cleaner before painting, welding, or plating.
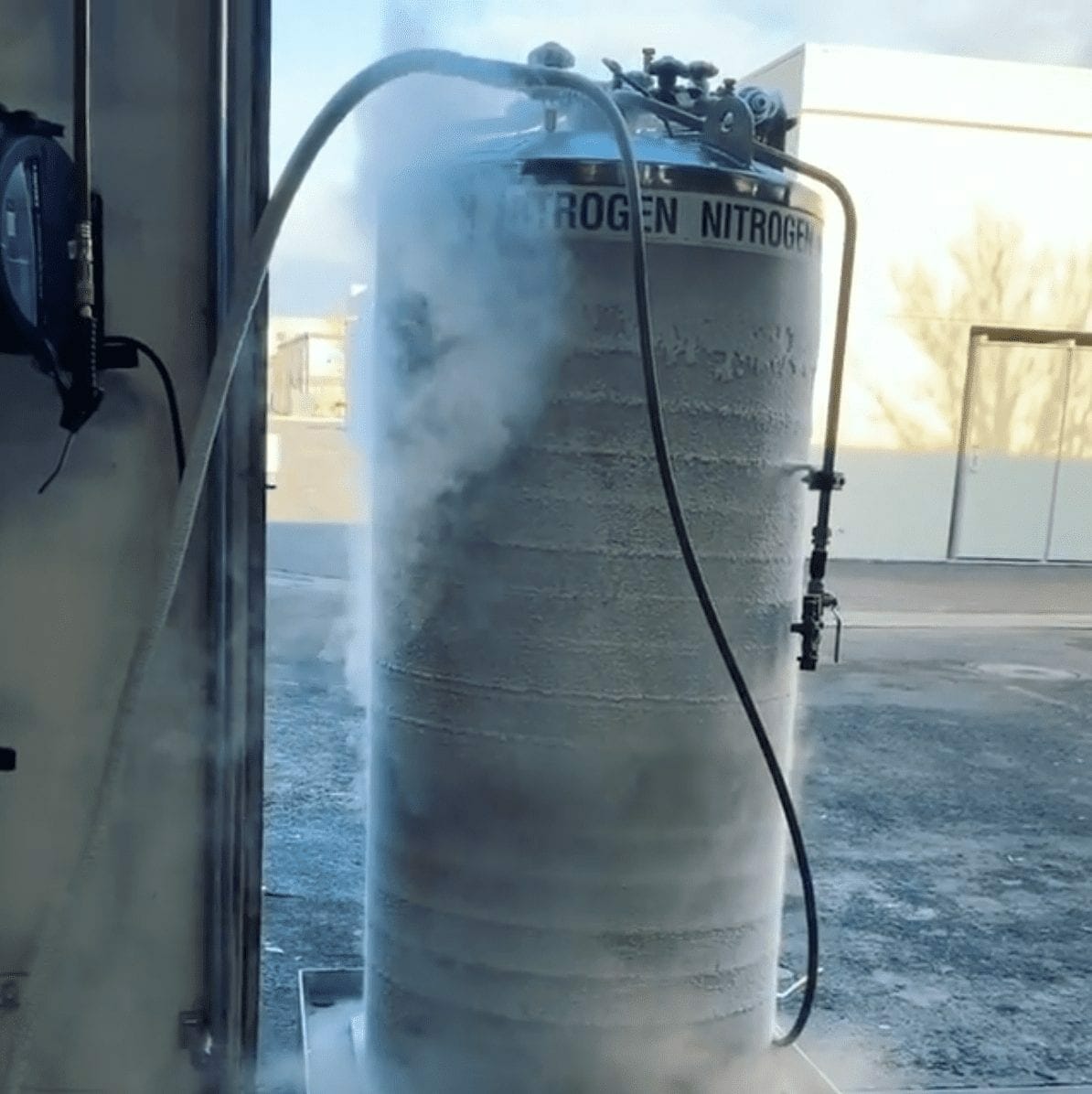
Easily Avoid HAZ In Your Custom Laser Cut Parts
At SendCutSend, we use industrial lasers and waterjet services to slice and dice carbon steel, stainless steel, aluminum, copper and brass, titanium…the list goes on. Depending on the metal, thicknesses up to 1/2″ are available and you can confirm the maximum overall part sizes here: Minimum and Maximum Part Sizes by Material. Our projects range from signage to precision machine components, as well as parts that will later be welded, bent, formed, or assembled. And if you need powder coating, anodizing, plating or other types of finishing, we can help there, too.
Getting started with SendCutSend is easy and takes just a few minutes. If you need assistance feel free to reach out to our support team.