Stainless steel is a useful and durable metal that allow it to blend the strength of carbon steels with the corrosion resistance of aluminum. Depending on the alloy, stainless steel can have extremely high strength and/or hardness values. One downside to stainless steel is that it tends to be more difficult to machine than mild steel or aluminum. If the project is being outsourced to experts like SendCutSend, it won’t be a problem. However, for those who prefer DIY, it will pose some headaches as well as some broken tools along the learning curve.
One option that alleviates many difficulties with regard to not only machining, but also assembly and durability, is PEM hardware. These inserts are permanently attached to sheet metal parts, eliminating the need to tap them directly. In this article, the benefits of PEM hardware will be discussed, along with the benefits of both types of PEM hardware that SendCutSend offers: zinc coated mild steel and stainless steel PEM hardware.
What is PEM hardware?
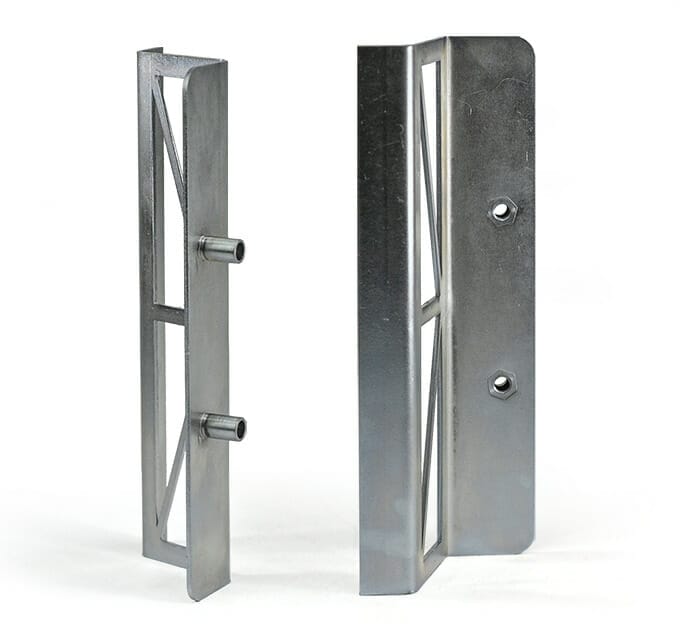
PEM hardware is hardware that is permanently installed into sheet metal components using a self-clinching technology. This hardware removes the need for one or more loose fasteners, simplifies the assembly process, and can allow fasteners to be used when access is difficult or otherwise impossible. PEM nuts, studs, and standoffs are pressed into the sheet metal, forcing the sheet metal to cold flow into the circular retaining feature of the hardware.This hardware is available as a service to be installed by SendCutSend into your parts.
At SendCutSend we offer two styles of PEM hardware: zinc coated mild steel and stainless steel. Each has its pros and cons that will be explored in greater detail below. With these two PEM hardware materials, hardware can be installed in eight of our most commonly utilized materials such as mild steel, 6061 aluminum, and 304 stainless steel. PEM hardware is offered in both English and Metric sizes, with nuts, studs, and standoffs being the standard types.
Why PEM Fasteners
We love PEM fasteners because they install permanently, reduce the amount of tools, and are able to be applied to thinner and lighter materials. To quantify “thinner and lighter materials”, they can be installed in metal as thin as 0.008”, which is about the thickness of two pieces of paper. With PEM fasteners, there is no need to use a tool on the PEM hardware side of the bolted joint, as it is permanently installed, thus eliminating the need to have tool access and simplifying the assembly process. With fewer assembly tools, the assembly process is faster, cheaper, and easier. Additionally, the PEM fasteners significantly increase the strength of a bolted joint in sheet metal. The PEM hardware introduces more threads than if the sheet metal were tapped directly, and for softer materials like aluminum, the harder material of the PEM hardware increases durability of the threads.
When to use PEM Hardware
While PEM hardware is a fantastic tool to keep in a designer’s bag, it isn’t always warranted, here are a few times when using PEM hardware is especially useful.
- Accessibility concerns
- If accessing the fastener and/or maintaining tool access to tighten the fastener is a concern.
- Assembly labor cost driving
- If assembly labor is more expensive than manufacturing costs
- Ease of assembly driving
- If the ease of assembly is a deciding factor (such as end user assembled products)
- Durability required
- If additional durability is required beyond that attainable by just sheet metal parts
- Thin sheet metal that needs tapped holes
- If thin sheet metal is being utilized, but a tapped hole is required
What happens to stainless steel when you put hardware in it?
A larger hole is required to install hardware than to tap directly into the metal. This larger hole actually results in a stronger connection as the forces imparted onto the sheet metal part are distributed around a larger area than just the threads. The larger distribution results in a much higher tearout capacity with hardware vs tapping. With PEM hardware, the backface of the sheet metal is undeformed by the installation, so there is no bulging to contend with. Additionally, since the hardware being installed is in a simple hole, there is little risk of work hardening, which can sometimes be a problem with threaded stainless steel parts.
Pros and Cons of Zinc Coated Mild Steel PEM Hardware
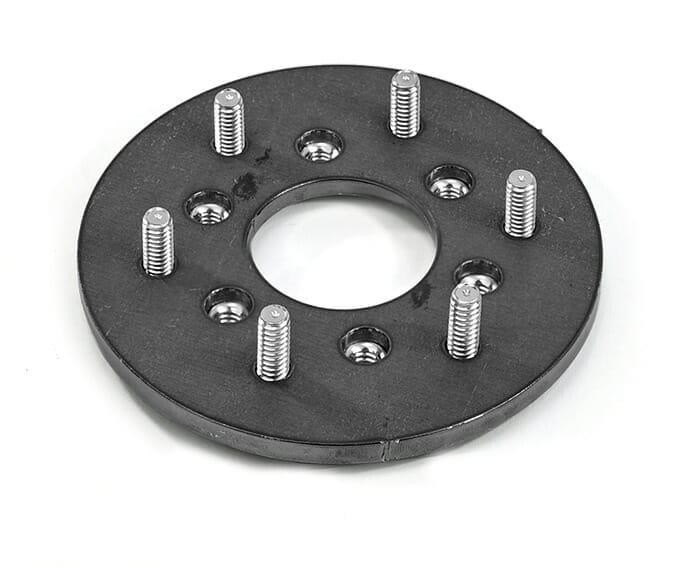
Zinc coated mild steel is a great general purpose option for PEM hardware. It can be used on most of the materials where hardware insertion is an option. The cost per fastener is lower for the mild steel options. Due to the zinc plating, the hardware has a good level of corrosion resistance. Finally, the zinc coating adds a degree of lubrication to the hardware, preventing galling from occurring. The main downside to mild steel PEM hardware is the incompatibility with stainless steel sheet metal parts.
Pros and Cons of Stainless Steel PEM Hardware
Stainless steel PEM hardware is typically used for more specialized applications. It is required when inserting hardware into stainless steel parts. The chemical and corrosion resistance of stainless steel hardware is much higher than that of zinc plated. Stainless steel also has hygienic properties making it more appropriate for food and/or medical industry uses. Additionally, stainless steel is able to withstand higher temperatures than zinc plated hardware.
There are two main drawbacks to stainless hardware, expense and galling risks. Stainless steel is inherently more expensive, so naturally the PEM hardware made of stainless will be more expensive than the equivalent of mild steel. Galling becomes a concern when stainless steel fasteners are used with stainless steel PEM hardware. This risk can be minimized with a thread coating on the fasteners to prevent the sticking that causes galling. Keep in mind for torque sensitive applications that coated threads do not torque in a consistent manner, and the addition of lubricant can more than double the applied torque.
Conclusion
PEM hardware is a fantastic tool to keep in any designer’s belt to solve some very challenging design problems. These useful inserts allow for both simpler and stronger assemblies and can eliminate the need for tool access on half of a bolted joint. For general purpose applications, zinc coated mild steel hardware is the more economical choice. However for food, medical, or other specialty applications, stainless steel PEM hardware might be a better option.
If you have any questions, feel free to reach out to us at support@sendcutsend.com. If you’re curious how else we can help, check out this brief article: What SendCutSend can do for you. When you’re ready, upload your design and get instant pricing today!
If you are new to SendCutSend, here’s a handy step-by-step guide on how to order parts from us: How to Order Parts from SendCutSend (spoiler alert: it’s super simple and intuitive to order from us)
FAQs
- What does PEM/PEM Fasteners mean?
- PEM is an abbreviation of Penn Engineering & Manufacturing Corp. These fasteners are permanently installed nuts, studs, and standoffs for use in sheet metal applications.
- Can PEM hardware be installed in any material?
- Currently SendCutSend offers PEM hardware installation in certain alloys of aluminum, steel, and stainless steel. See our services guide for Hardware for more information.
- Does PEM hardware need to be tightened?
- Due to the self-clinching nature of PEM hardware, it never needs to be adjusted or tightened.