We often get asked the question; can laser cut material be flexible?
The simple answer is yes, but it’s complicated.
Generally speaking, laser cutting is used to create 2D metal designs. However, these 2D designs can be turned into 3D designs by bending types of metals that are considered flexible.
As an example, a simple sign could be bent into an arc to make it stand up, or a design could be bent into a circle to turn a flat plane into a ring.
The complexity comes into the equation when you are choosing the type of metal you need for your creation. Some metals are lightweight and flexible while others are heavy and durable. In the end, whether or not you need a malleable metal for your project will come down to your design and its desired use.
In some cases, flexibility can be detrimental. If you design a sign that will be hung outside, it may bend during high winds or other destructive weather when your choice of metal is too flexible. In this case, you’d be looking for a strong metal that isn’t prone to breakages, such as titanium or steel. Using flexible metals like brass or copper wouldn’t be appropriate in this situation.
To delve further into the topic of flexible metals and laser cutting, here’s what you need to know.
What Are Some Examples of Flexible Metals?
Once a flexible metal part is cut, it can be bent, or otherwise shaped, to create a design that has some depth.
There are types of metal that are specifically designed to be flexible, most often alloys. Aluminum alone is very flexible, and different types of aluminum and steel are going to be strong and versatile. If you want a flexible metal part, you need to choose the right metal to use, as well as the right thickness.
For example, the thicker the material, the less flexible it will be – generally speaking. If you want your material to be thick, it will compromise some of the flexibility, but the material will also be stronger as a whole.
Some of the flexible metals we offer include:
- Standard aluminum. Our standard aluminum is light, won’t rust, and will easily bend. We also have a stronger version of this aluminum, our Aerospace aluminum, for applications in which hardness is preferred.
- Brass. Brass is highly malleable and easy to bend. It’s an attractive metal, which can be used as a centerpiece, feature, and signage. Brass takes a variety of finishes very well, including mirrored or frosted finishes.
- Copper. While heavy and dense, copper is still fairly malleable and therefore flexible. Copper also has the benefit of being antimicrobial, conductive, and rust-free. It’s often used for things such as jewelry for this reason.
We recommend asking about materials that are flexible enough for your needs, depending on the end product you’re interested in. As well, you will need to consider the finishing options available and the amount of detail the metal can hold, before you make your selection.
Do Flexible Metals Affect the Accuracy of the Laser?
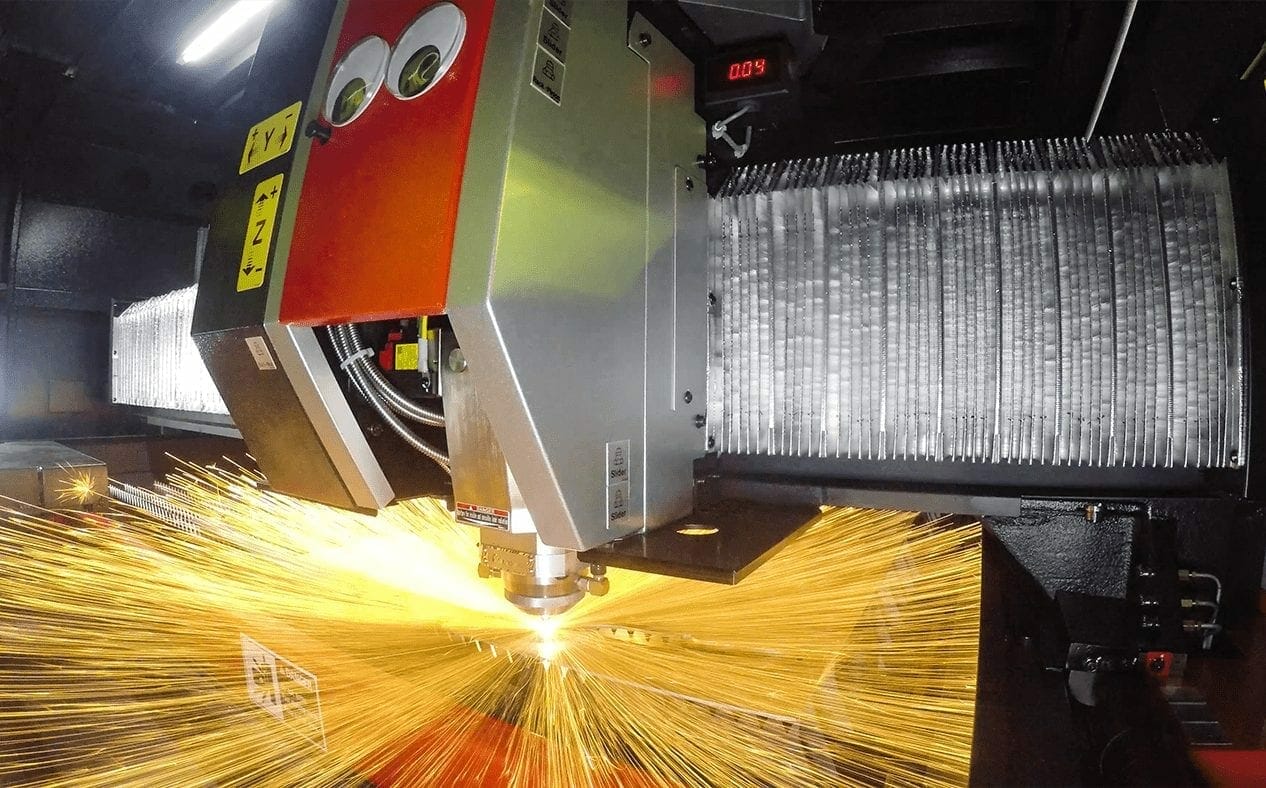
Since the laser itself imparts very little movement, the flexibility of the metal doesn’t control whether the laser is able to cut it. The laser head will move smoothly across the surface of even a flexible metal, cutting the metal cleanly without bending it. As long as a material will not readily bend or fold while inside the laser cutting machine, and the material isn’t prone to combustion, the laser should be able to cut it accurately. There could, however, be laser marks on the edges of the cut.
The most important thing when it comes to the accuracy of laser cutting is the material thickness. Lasers only cut to a certain depth, or the material itself can be damaged. Hence, the detail of the cut will be determined predominantly by the thickness of the material.
While flexibility won’t have a large impact on the accuracy of the cut itself, it can affect the finishing process. Aggressive polishing techniques are more difficult with flexible parts, though a chemical finish will not be impacted by flexibility. You need to take these things into account when designing and choosing the material.
When Should You Avoid Flexible Metals?
Something you will need to consider when choosing a metal is whether or not you plan to bend or weld the object after cutting.
When it comes to bending objects into an arc, you want flexibility with the metal you choose. However, if you want to create something at a 90-degree angle, the other option is to cut two parts and weld them together. A welded item can be made out of stronger, thinner materials.
Here are some of the better materials for welding:
- Aerospace aluminum. This is the best aluminum for welding. It will be stronger than standard aluminum, but otherwise has many of the same properties, such as being lightweight.
- Cold-rolled carbon steel. This material is commercial quality steel that’s strong and easy to finish. It’s also available in a number of different thicknesses.
- Hot rolled carbon steel. If you want a material that’s easy to work, this carbon steel is ideal. It’s virtually indestructible, easy to machine, and easy to drill.
- Stainless steel. A classic, stainless steel welds well and is strong and durable. It’s also resistant to corrosion and available in three finishes: regular, mirrored, and grained.
- Titanium. One of the strongest and most versatile materials, titanium has the advantage of being both extremely strong and also light.
The above materials would be used for welding rather than bending, so they would not be considered flexible. However, you may decide that welding a more durable material together is better suited to your design than bending a flexible one. In this case, consider these options.
Interested in creating products, prototypes, or parts with bends and joins? Get in touch with our support team to discuss the most appropriate metal for custom laser cutting.