Warping in laser cutting can lead to unwanted distortions in your parts, affecting functionality and aesthetics. This article delves into the causes of warping, such as mechanical and thermal stresses, and the removal of internal stresses during the cutting process. It also explores how different materials, like metals, plywood, MDF, and plastics, react to these stresses. Additionally, we discuss practical tips for preventing warping, both before and after cutting, and offer solutions for dealing with warped parts to ensure the best results for your projects.
What is Warping?
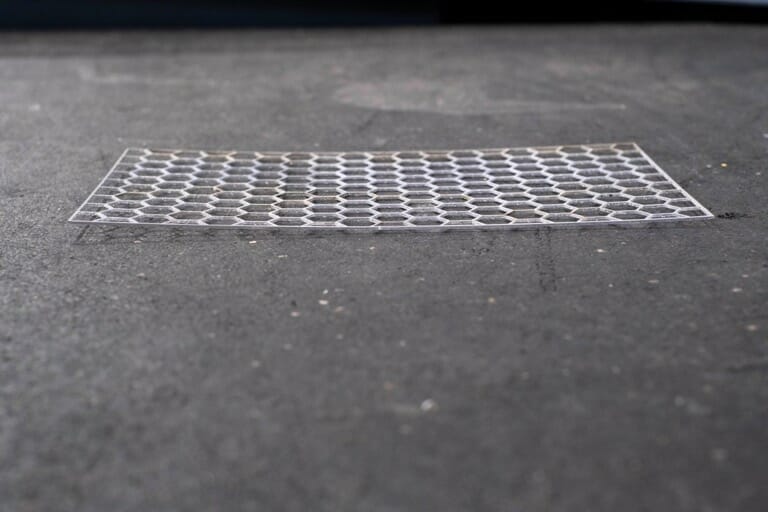
Warping is the unwanted bending or misshapening of your parts. Whether you intend your parts to be flat, square, curved, round, etc., if it bends or twists unintentionally, that’s warping. Unintentional/undesirable warping is what we’re going to focus on in this article.
What Causes Laser Cut Parts to Warp?
There are multiple reasons a laser cut part could warp, but fundamentally it happens because internal stresses inside the part become unbalanced. Most materials hold whatever shape they’re in (whether that’s flat or bent) because of the way they’re stressed. Introduce an imbalance and the part shape will change until it reaches an equilibrium or balance. Imbalance can be caused by increasing or decreasing stresses in the part unevenly. Or it can be caused by removing partial sections of stressed material.
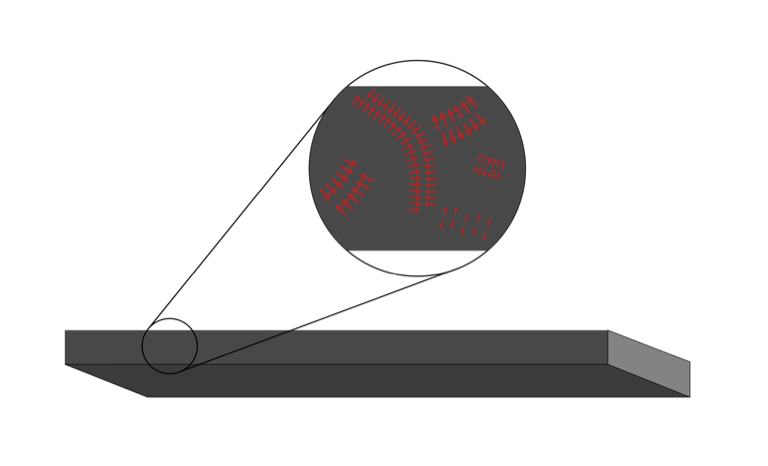
If that sounds confusing, think about intentionally creating a bend in a piece of sheet metal. It works exactly the same way. The flat part is held flat because internal stresses are all evenly applying tension and compression to hold it flat. To create a permanent bend in a part, you move the material enough to induce additional stress inside the part. The part then springs back to a position where the internal stresses are again balanced. Since you introduced new stresses, the new equilibrium shape isn’t flat, it’s bent. This is also why creating a 90 degree bend in a material nearly always requires you to push the material slightly past 90 degrees and let it spring back to the desired angle. The mechanism is the same for warping, the difference is whether the change in shape is intentional or not.
Let’s look at some more specific examples.
Mechanical Stress
Just like we discussed above, mechanical stresses can cause a part to warp. Tightening a pattern of bolts unevenly can cause parts to warp. If you’ve ever torqued the lug nuts on a car wheel, you know that you need to torque them evenly, otherwise you can warp the wheel. This type of warping can be either permanent, meaning when the forces are removed the part stays misshapen. Or the wapring can be temporary, when the forces are removed, the part goes back to its original shape. The difference between permanent and temporary is whether or not the forces have caused enough stress to exceed the material yield strength. Check out our materials page for a specific material yield strength.
Denesting is a good example of how laser cut parts can be warped from mechanical stresses. Denesting is when parts are removed from the plate after they’ve been cut by the laser (or by any other method). If the material is extremely thin and the details very fine, it can be a challenge to get the parts free of the surrounding material without distorting them slightly. We take care with all parts, but sometimes parts are delicate enough that a small amount of distortion can’t be avoided.
For certain shapes, sizes and processes, tabs are used to retain the cut part to the surrounding material after it’s cut. Tabs are small bridges of material left uncut between the part shape and the plate it’s cut from. This prevents the parts from shifting once they’re free. After the part is cut using the laser, these tabs can be cut or broken manually and the part pulled away. The tab needs to be strong enough to hold material in place until the cut is finished, but no stronger. Delicate pieces run a higher risk of warping when the tabs are broken.
Thermal Stress
Changes in temperature can cause warping. Typically, materials will expand when heated and contract when cooled. If a material is heated or cooled unevenly, it can cause that expansion/contraction to happen unevenly which can cause the part to warp. For many materials, metals usually, you can look up the coefficient of thermal expansion as a property of the material. Having two dissimilar materials (steel and aluminum for example) secured together then heated or cooled, will cause the materials to expand/contract at different rates. This can cause warping, even if the parts are heated evenly.

Thin materials are especially prone to warping from changes in temperature. Welding can quickly warp a part since parts are joined at extremely high temperatures, then shrink while cooling back down to ambient temps. You may have seen the effect of thermally induced warping if you’ve ever left a large flat panel in the sun. It heats up on one side more than the other and the panel warps. Similarly, you may have seen a flat baking sheet warp as the oven temperature increases. Even though the oven heats fairly evenly (though they often don’t), sometimes the shape of the part means it expands differently on one side vs the other.
Removing Internal Stress
Warping caused by the removal of internal stresses is the most common type of warping seen in laser cutting. You may think thermal stresses are a concern, but laser cutting happens so quickly and is so localized, it has very little impact on the part thermally. Instead, parts can warp when large areas of material are removed from flat sheets. The higher the percentage of material removed, the more likely the balance of internal stresses are to be affected, causing warping. In general, removing around 50% of the material starts to increase the likelihood it will warp.

This isn’t only true with laser cutting, but can apply to waterjet cutting, routed parts, milled parts, plasma cut…; virtually any method for removing material has some risk of causing warping. The more material removed the higher the risk, but risk is also higher the more internal stresses inside the part.

Sources of Internal Stress
To better understand where internal stresses come from on new, flat sheets of material, we need to look at how materials are manufactured and transported. In general, most metals are cast from a liquid form and pushed through a set of dies and rollers to flatten them down to whatever thickness material is being made at the time. In order to be able to ship the large sheets of material efficiently, they get rolled up like a cinnamon roll or a burrito.
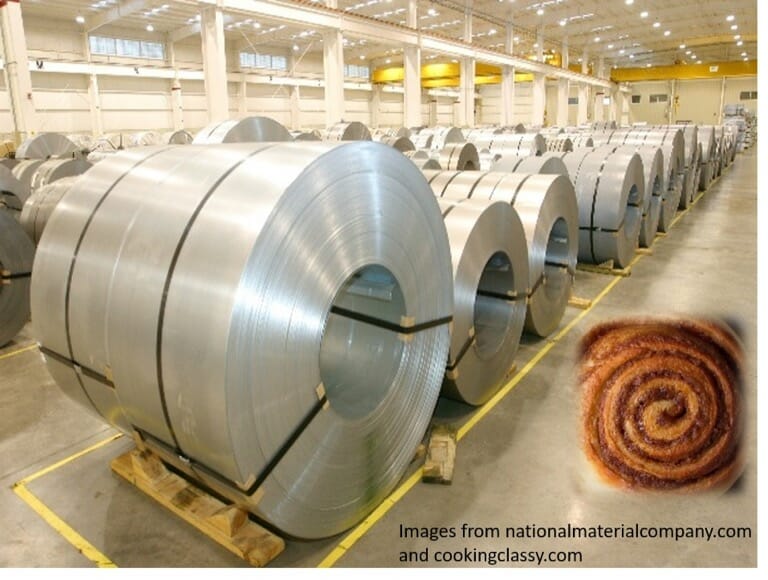
You may have even seen these big rolls being hauled down the highway on the back of a truck. Since most materials are sold to the final customer as flat sheets, the rolls need to be flattened back out before being cut to regular stock sheet shapes. So, casting the material creates thermal stresses as it cools. Squeezing the material to thickness creates mechanical stresses to keep it at that thickness. Both the act of rolling up the metal cinnamon roll and then flattening it back out add all sorts of internal stresses into the part.
That nice flat piece of metal, now ready for laser cutting, is loaded with all sorts of internal stresses, but they’re balanced in such a way that it holds its shape. If those stresses change enough to cause an unbalance, the part is going to be pushed or pulled in some unpredictable way potentially causing a warp.
That’s metals. What about other materials like plywood and MDF? The sources of internal stresses on plywood and MDF aren’t really the same, but internal stresses are still there. Both plywood and MDF are made by gluing together natural materials. Very rarely are natural materials nice and straight and even. Because both are basically wood, they’re porous and very susceptible to moisture. Where steel will start to rust when exposed to moisture, wood will absorb the moisture and swell. Often just a change in humidity between the humid air in summer and the dryer air in winter can be enough to cause unsealed wood to warp. This is especially true when parts are exposed to moisture unevenly. If you’ve ever picked through a pile of crooked 2x4s to find a relatively straight one, you’ve seen how wood can warp.
Plywood is typically assembled with the layer grain direction alternating. That’s why plywood can often be more stable than more natural forms of wood (like 2x4s). MDF is essentially sawdust packed tightly and glued together. That makes it very uniform and very stable, but also gives it a ton of tiny exposed surfaces that can suck up moisture.
What about plastics like UHMW, ABS, HDPE, etc.? Plastics are made up of long polymer chains all intertwined and locked together. That interlocking makes plastics pretty strong, but also creates similar internal stresses that we’ve been discussing.
There’s one last type of material we want to discuss here, composites. First, what is a composite? A composite material is simply multiple materials stuck together. Carbon fiber and G10 are composites of carbon fiber strands or other types of cloth weaved together in some pattern suspended in a hardened resin. ACM (Aluminum Composite Material) is a plastic core sandwiched between two aluminum skins. Composites can often benefit from the best aspects of the different materials that make them up. But because they are made up of differing materials, they can sometimes carry similar internal stresses and suffer from different rates of thermal expansion.
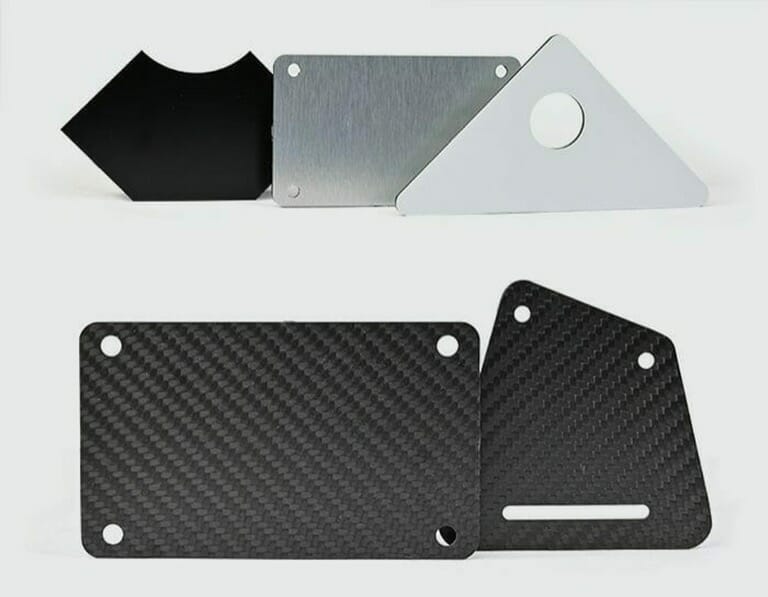
Tips on Preventing Warping
Ok, so we know a handful of reasons why parts can warp. What can we do to prevent warping? Sometimes, there’s nothing you can do, and warping just happens, but there are a few things we can do to reduce the chances of warping.
Before Laser Cutting
When it comes to laser cutting flat panels, the more material being removed over a certain area, the more likely warping is to occur. Grill-like mesh shapes or long, thin shapes are most likely to warp as the material is removed. As mentioned above, removing more than about 50% of the area starts to increase the odds that the part will warp. If you can remove less area, that will help, but sometimes your design needs to remove more material.
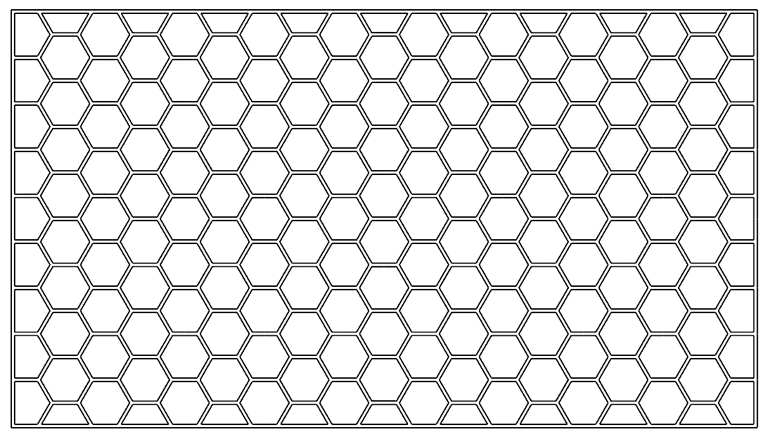
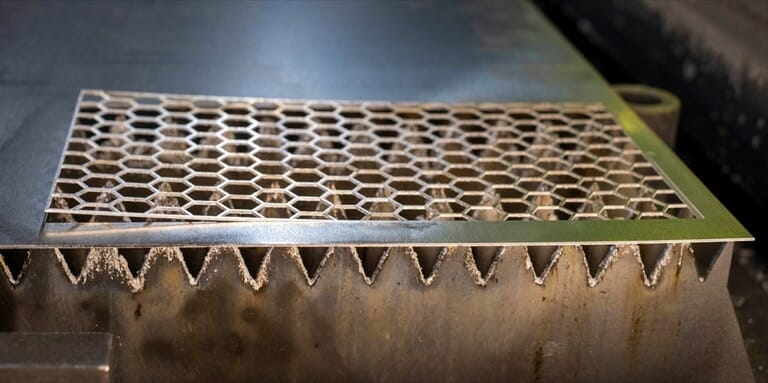
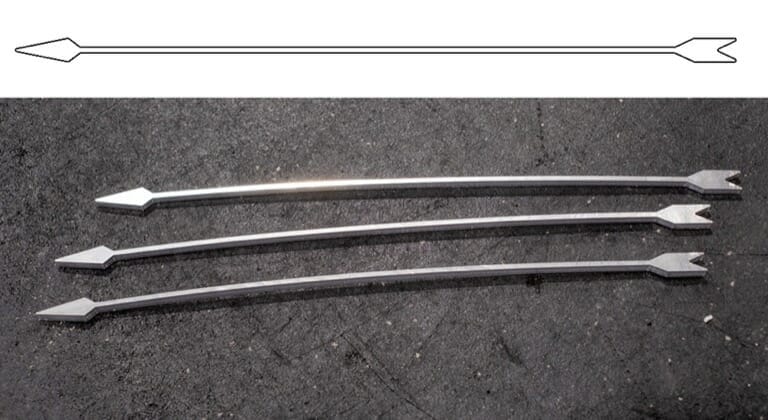
We manually review each design before it’s cut, to check for things like how likely it is to warp. If we think your part has a high risk of warping, we may reach out to you before laser cutting to discuss some options. Sometimes the exact same part can be cut multiple times and not warp the first time, but warp significantly the second time. In fact, it took us multiple attempts to get parts to warp just to take some photographs for this article. Since it can be difficult to know exactly what the state of internal stresses in a sheet of material are, sometimes you just don’t know if a part is going to warp or not.
If you’re cutting out a large percentage of area from a sheet, you might consider how wide your bridge material is. Sometimes a wider perimeter or wider bridges or webbing material can be enough to hold the parts flat as they’re cut. Again, this isn’t a guarantee your parts will or won’t warp, but it can improve the odds. When using bridging shapes to connect isolated geometry, a good target is around 2x the material thickness. The more connections you have the better, and it’s possible to get away with thinner sections.

Sometimes just switching materials may help to reduce the chances of warping. Stainless is a little more likely to warp than steel and aluminum. Composite materials are typically very good at resisting warping and can provide plenty of strength at light weights.
After Laser Cutting
What about parts that are already cut? If you’re going to be welding on your parts, you can try to heat the part evenly. If you can weld evenly on both sides, that can help balance out the thermal shrinkage and reduce warping. If you have multiple welds, you can try to minimize the amount of heat you put into the part, either by letting it cool between welds or skipping around the part as you weld so heat isn’t focused as much in one small area.
Designing your parts to be stiffer can be a great way to reduce chances of warping. A flat sheet will be much more sensitive to warping than a sheet that has a bent flange or a rib, or dimple die in it. Take a look at our article on material thickness for some more ways to increase the stiffness of your parts.
If your parts are going to be exposed to temperature changes, having consistent thicknesses or evenly exposed areas can help parts to heat up and cool down more evenly.
If your designs are made from wood parts, completely sealing the parts can help reduce the absorption of moisture. Having parts evenly exposed to the air can also help them absorb moisture more uniformly.
What if Your Parts Warp?
Having a part that’s warped doesn’t always mean the part is unusable. Depending on the application of the part, it may still be functional. Sometimes a warped part can be simply bent back into the desired shape.
Parts that get assembled together may naturally bend back into the correct shape as they are adjoined to other pieces. Sheet metal assemblies in particular can often handle small amounts of warp that vanish as the parts get assembled. The stamped sheet metal pieces in a modern car body often work this way. By themselves the parts aren’t perfect, but once assembled together, the structure is held rigidly into the desired shape. Not all parts or assemblies work that way though, so you may need to look at other ways to reduce warping.
If your parts warp significantly during laser cutting, there’s a chance the laser head will hit the side of the part and damage the part, the laser or both. The laser head is pretty close to the material, so it doesn’t take much warping for this to be a concern. We do our best to catch parts like this before damage can occur. If your parts do end up warping when they’re cut, we’ll likely reach out to you to discuss your options.
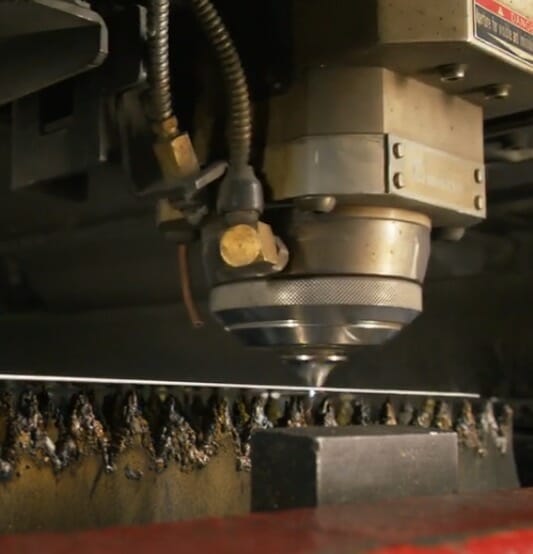
Another note, often warped parts can’t be deburred because of the way our deburring equipment runs over the surface of the material.
The Best Way to Prevent Warping in Laser Cut Parts
Warping in laser cutting is usually undesirable, but does not necessarily mean a ruined part. The reason parts warp is due to an imbalance of internal stresses, either through introducing new stresses, mechanically or thermally, or by removing a portion of existing internal stresses.
It can be nearly impossible to know for sure if a part will warp or not, but there are some things we’ve discussed here that are good indicators. We’ve also discussed some things you can do to reduce the chances of warping.
Oftentimes a warped part can be fixed, or even used as is. We’ll do our best to let you know if parts in your order are likely to warp before they’re cut. If they do warp during laser cutting, we’ll reach out to you to discuss what can be done.
Hopefully this gives you a little more insight into why laser cut parts warp and what you can do about it as you’re designing your next project.