After dimensional accuracy, edge quality and surface finish on your SendCutSent™ parts may well be the most important considerations: whether that’s because you plan to use the parts unfinished and want to know what to expect, or need them to perform well in a secondary operation, like welding.
In this guide, we’ll summarize our cutting processes, cover eight factors affecting edge quality, and surface finish, and give specific examples for some of our most popular materials.
We’ll also share a few handy tips and tricks to help you achieve great edge quality and surface finish no matter the application.
Table of Contents
- Defining edge quality and surface finishing terms
- Laser Cutting
- CNC Routing
- Waterjet Cutting
- Factors that affect edge quality
Define Your Terms
In the wide world of laser cutting, there are a number of terms used to describe edge and surface finishes. Knowing these terms, and why they’re important, helps inform our material selection. Some of the most common terms are:
- Dross is a layer of oxidized metal that forms on the edge of a laser cut part. It is caused by the heat of the laser beam reacting with the atmosphere and assist gasses, and can be removed with an abrasive pad, file or grinding wheel. Note that our deburring process only contacts the top and bottom face of the material, so it will not fully remove edge dross.
- Burrs are small pieces of metal that are torn from the edge of a laser cut part, typically showing up where the laser blows through the bottom face of the part. They are removed during our deburring and tumbling process.
- The HAZ (heat affected zone) is the area of the material directly affected by the heat of the laser beam. Although it can be discolored in this area, we take care to ensure our laser settings don’t weaken the material.
- The kerf is the width of the cut made by the laser beam, waterjet, or CNC. See the specifics on kerf width, kerf compensation, and more on the Design Guidelines page for each process linked above.
- Scratch: A blemish in the surface of the cut material, typically from loading and handling. These are removed in the deburring process, but post-operations like bending, tapping, and countersinking, can mar the brushed finish from the deburring process.
- Gouge: If scratches had a boss level… Not what you want to see on your laser cut parts. Our QC team usually catches and remakes parts with deep gouges that can be easily felt and that don’t get fixed by the deburring process, but if your part comes gouged, take a pic and let us know–we’ll remake it straightaway.
With some terminology under our belt, let’s look at our cutting processes. Starting, of course, with the biggest, fastest, most powerful cutting process in the American West: Lasers!
Laser Cutting
When someone starts talking about a laser’s power, speed, and the focus, it gets complex fast, but we know a thing or two about laser cutting at this point, and all these variables (and more, so many more) are fine-tuned for each material, to produce very clean edges with minimal dross, HAZ or burrs.
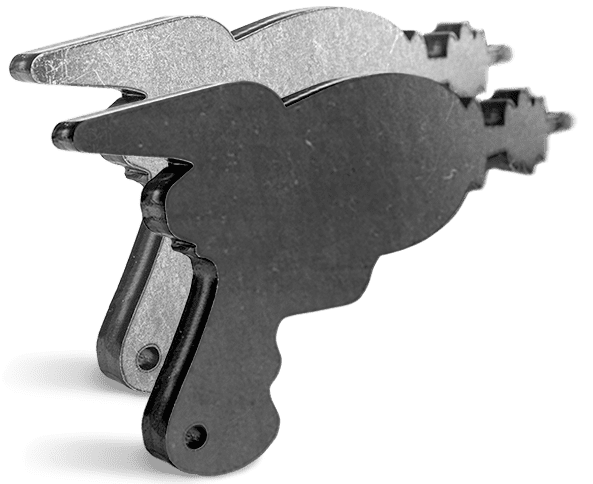

How does it work?
- Laser Generation: A laser source, either CO2 or fiber lasers, generates a concentrated beam of light.
- Laser Delivery: Mirrors and lenses guide and focus the beam onto the metal workpiece. This process is done in the cutting head, which is controlled to a specific speed and power delivery.
- Cutting: The focused laser beam heats the metal intensely, causing it to melt, vaporize, or be expelled by an assist gas jet such as oxygen or nitrogen.
Benefits of Laser Cutting
- Precision: Creates intricate and complex shapes with tight tolerances: +/- 0.005” in most materials.
- Clean Cuts: Produces minimal heat-affected zone, preserving material properties and often eliminating the need for post-processing.
- Fast and Efficient: High cutting speeds, making it suitable for high-volume production.
CNC Routing
Most of the plastics and composites we offer are cut on our CNC machines. Yes, all our cutting equipment is technically Computer Numerically Controlled (CNC), but in this case, we’re referring to just our automated routers.

How does it work?
- Control: With all three cutting processes, software controls how the individual parts are mapped to ensure the most efficient use of material and shortest cut paths.
- Cutting: Instead of lenses and mirrors, a powerful motor is housed in the spindle, which turns the cutting tool–a router bit.
- Kerf: Since a physical bit is doing the cutting, rather than a high-power beam of light, or stream of water, the minimum kerf is going to be the diameter of that tool, which in our case is 0.125”.
Benefits of CNC cutting
- Amazing accuracy: at +/- 0.005” in most materials.
- Kerf compensation: Like all our other cutting methods you also get kerf compensation, just remember that minimum part geometry and feature resolution are a bit bigger because of that tooling diameter.
- No HAZ: because we keep our tooling sharp and mind our speed and feed, you don’t have to worry about burnt parts.
- No chipout: Unlike a circular saw, the motion of a CNC router cutting tool doesn’t chip out the bottom face of the material, so no more masking tape or frustrating splinters in SCS plywood parts.
For more on CNC Cutting, take a look at this deep dive into the Process and Uses.
Waterjet Cutting
Waterjet cutting is a versatile and cold-cutting process, meaning it can’t cause heat-related damage to the material, and although it used to be rather slow and inaccurate, our top-notch equipment is anything but.
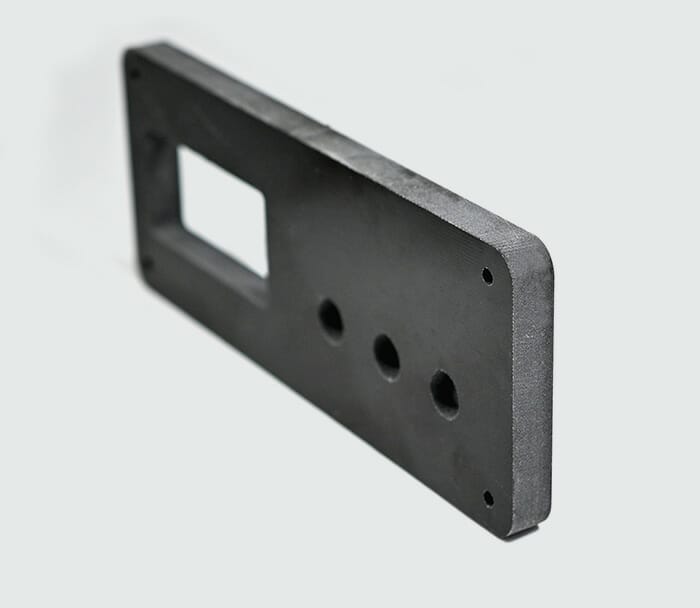
How does it work?
- High pressure pump: First, a pump pressurizes water to extremely high levels, typically exceeding 60,000 psi (4,140 bar).
- Nozzle: The pressurized water is then directed through a tiny jeweled nozzle, which concentrates the stream and accelerates it to supersonic speeds (up to 2.5 times the speed of sound).
- Cutting: This high-pressure, high-velocity waterjet can then cuts through the material by eroding the surface. An abrasive material like garnet is typically added to the water stream, enhancing its cutting power.
Benefits of Waterjet Cutting
- What can it Cut? Virtually any material, regardless of its shape or thickness.
- Precision: Cuts with extreme accuracy and minimal kerf width, reducing material waste.
- Cold cutting: No heat-affected zone, maintaining the material’s integrity and properties.
- Clean process: Minimal dust or fumes generated, making it environmentally friendly.
- No tool wear: Abrasive particles do the cutting, eliminating tool wear and tear.
If you need, say, a carbon fiber switch panel for your race car, look no further than our Waterjet Cutting service.
8 Factors that affect edge quality and surface finishes
While we can promise that the parts you upload will have fantastic edge and surface finishes, what exactly that means can be broken down in a lot of different ways: Here are eight factors you can consider, with example materials.
1. Material Type
Metals, plastics, composites, and woods each have unique characteristics affecting edge quality: some just don’t cut well at all with lasers (say, the melty mess the edge of a plastic part would be if we cut it on the laser).
We select one of our three cutting services, (laser, waterjet or CNC), so that regardless of your material choice, we use the cutting method that delivers the best finish.
Surface finish also varies pretty widely by type: our acrylic is cut with a protective paper backing in place so that what you get is a scratch-free part, but how about, say carbon steels, which are easily our highest volume material:
HR Steel:
- Edge quality: Laser cutting delivers great edge quality in hot rolled steels.
- Surface Finish: mill scale (oxide left from the steel manufacturer), must be ground off to weld, or paint. You can do this yourself, or use our deburring service on most parts and save yourself a bunch of time.
- Watch out for: Light scratches from loading in the machines, and witness marks on secondary processes.
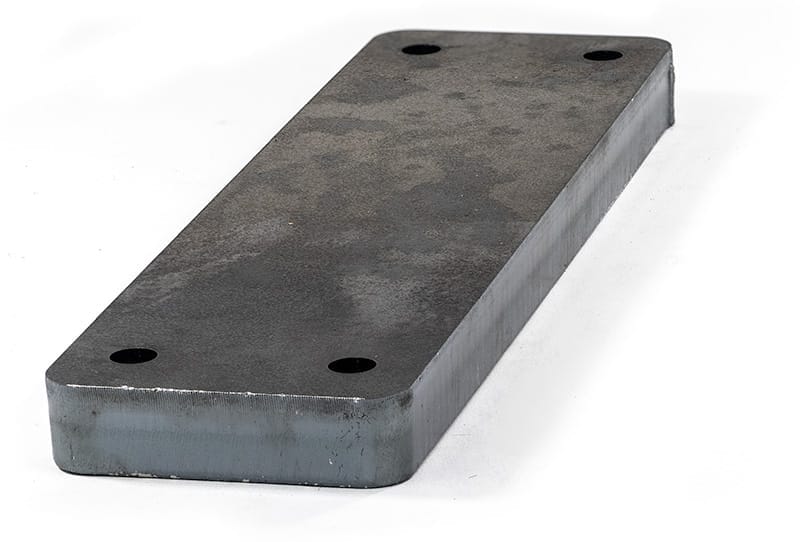
2. Material Thickness
At SendCutSend, we try to offer the thickness you need for your project, rather than forcing you to pick whichever is “close”. That means, though, that on a popular material like 5052 Aluminum, we currently offer ten thicknesses from 0.40” to 0.500”.
Thicker materials often require adjustments in cutting parameters for optimal edge quality, and generally, thinner materials will have a cleaner edge right off the laser, but are more sensitive to changes in cutting conditions.
5052 Aluminum:
- Edge quality: Parts about 0.25” and thicker have a coarse finish comparable to waterjet cut parts. Some dross/sawtooth edge will occur, but it’s all removed in deburring.
- Surface finish: Aluminum naturally develops an oxide layer, making it very resistant to corrosion in a normal work environment, so expect clean parts with an appealing brushed finish if you choose our deburring service.
- Watch out for: Aluminum is soft for a metal, so remember that it scratches easily and picks up oils easily.
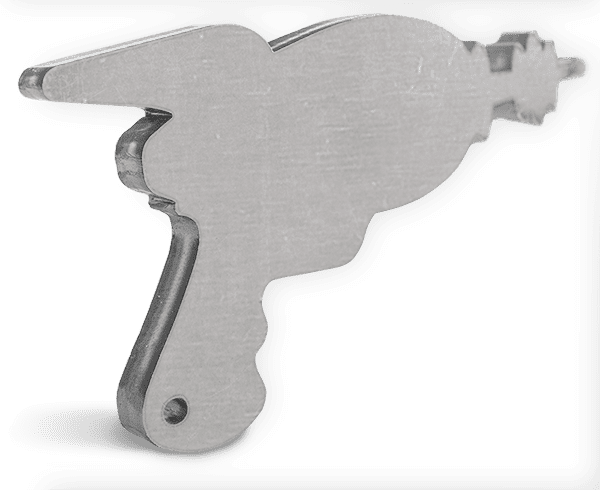
3. Material Composition
The composition of the material, especially in the case of composites, can affect laser cutting.
Consider any layers or additives that may influence the cutting process. For Carbon fiber, G-10 and Phenolic, we use our waterjet equipment, which delivers super smooth edges through the varying layers of these materials. No need to worry about fraying, burning, or even sloppy features: our waterjet tolerance is a tight +/- 0.009”.
4. Reflectivity
While the highly reflective surface of some materials, like aluminum or brass can pose challenges for laser cutting, our industry leading equipment allows us to make quick work of them.
Copper & Brass:
Edge Quality: We use oxygen assist gas to cut these two soft metals leaving a great looking edge.
Surface finish: Because they aren’t very hard (for metals) and relatively smooth, they have very delicate surfaces. If you’re spending to have copper or brass parts cut, you likely plan to spend some time making them look 100%.

5. Thermal Conductivity
Materials with high thermal conductivity dissipate heat rapidly during cutting.
While this can affect the edge quality, especially in terms of thermal distortion and burr formation, we’ve already covered brass and aluminum, which are among the highest conductivity materials available. Limiting the laser power and maintaining a high rate of speed mean our edges and HAZ at the surface are kept to a minimum.
6. Tolerance Requirements
Consider the required level of precision and edge quality for your specific application.
Some materials inherently offer better tolerances, and depending on the cutting method, the tolerance may change.
MDF:
Tolerance: For our laser cut MDF (0.125” and 0.250”) the tolerance is a tight +/-0.009”, but for the thicker offerings they’re cut on the CNC router, giving them an even tighter +/-0.005”.
Edge Quality: Laser cut parts have a dark edge and looks really sharp, due to the CO2 laser burning the edge. CNC parts have a smooth burn-free surface.

7. Surface Finish Requirements
If a smooth surface finish is crucial, and a “brushed” finish isn’t what you’re looking for, select materials that are less prone to rough edges or burrs.
Some materials require less post-processing to achieve the desired finish: It’s easier to bring a soft metal like aluminum or brass to a bright finish than something like grade 5 titanium.
Other materials, like our AR steels, have a rough finish which is integral to the part’s durability. Sometimes rugged is beautiful.
8. Melting Point
This was touched on before, but the material’s melting point influences the cutting process.
Most materials with lower melting points are prone to melting rather than cleanly cutting. There are notable exceptions, such as our acrylic panels, which are cut using our CO2 laser rather than a CNC router.
Taking care of edge quality for you
This article includes a lot of information which only just ahem scratches the surface on most of these topics.
To sum up, although it takes time to dial in all the factors for a new material, but by the time you order, we’ve cut hundreds or even thousands of parts in that specific material and thickness, so you can be confident that the finished product will be fantastic.
Could you order a Laser, CNC router or Waterjet system, make these adjustments yourself, and get great results? Absolutely, but take a look at our article about the True Cost of Owning a Laser, before adding that thing to your cart. Here at SendCutSend we can do what we do starting at just $39, with per piece costs around $0.50 because of huge volumes and clever software–give it a try by uploading your next part today.