Our requirements for minimum geometry are listed as specifications on each individual material page in our Material Catalog.
Learn how to confirm material specifications!
For laser cut materials, make sure all of the holes, slots, and cutouts in your part meet the minimum requirements for the material and thickness chosen. Learn how to confirm design requirements for any material!
For waterjet cut materials, the minimum hole or slot size we can cut is generally 0.070″ or greater depending on the material thickness. This is due to the size of the waterjet stream.
For CNC routed materials, the minimum hole or slot size we can cut is 0.125″. This is due to the 0.125″ tooling used with our router.
We want to make sure your parts come out perfectly, so we provide all the resources necessary for you to help us make that happen. Our service design guidelines, max/min material charts, and material specifications will provide all the minimum geometry information needed before you upload your design to our website for a quote!
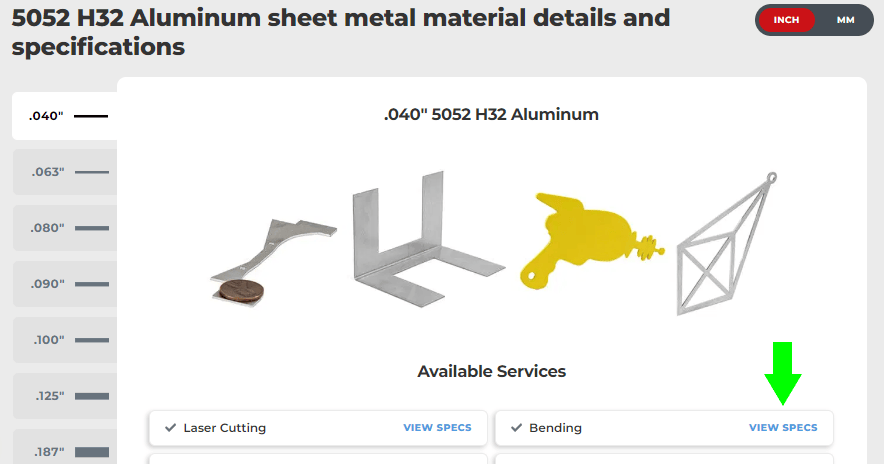
Select the material thickness needed to view specifications for each service offered.