Our requirements for joggle bends depend on the material and bend angles. “Joggle” bends refer to two bends that are close together and bent in opposite directions.

Sheet metal joggle bends
Joggle bend requirements in sheet metal will depend on how obtuse or acute the bend angles are. You can find all specifications referenced below on each individual material page. Learn how to find material bending specs.
One or more bends is between 5°-90°
If one or more joggle bends is between 5-90 degrees and neither bend exceeds 90 degrees, the bend lines must be at least the Minimum joggle bend line to bend line @90° max flange apart, measured from bend line to bend line.
One of the joggle flanges must not exceed Maximum joggle Bend line to bend line @90° max flange.

One bend is between 5°-90° and the other is between 91°-130°
If one flange on a joggle is between 5°-90° and the other is between 91°-130° (i.e. one flange is acute), the minimum distance between the flanges will be determined by the die size used for the material thickness.
.472″ Die: min 0.7″ between flanges
.630″ Die: min 0.9″ between flanges
.984″ Die: min 1.2″ between flanges
You can confirm the die width used for each material thickness we bend in the material specifications.
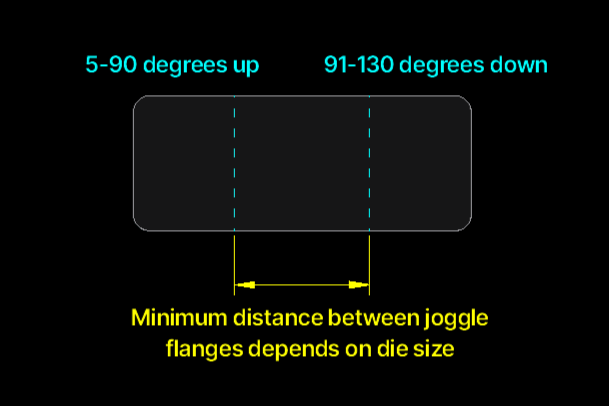
One or more bends is between 91°- 130°
Acute joggles (one or more bends is 91 degrees or greater) are produced on a case-by-case basis. If our team has concerns about manufacturability, we’ll contact you right away!
Polycarbonate “joggle” bends
Parallel bends in opposite directions can be bent in polycarbonate as long as the flanges are at least 3.00” apart if measuring from the center or apex of each bend, and one of the flanges is no longer than 5.00”.
Please note, we only bend polycarbonate between 45° – 90°.
Learn more about polycarbonate bending limits.
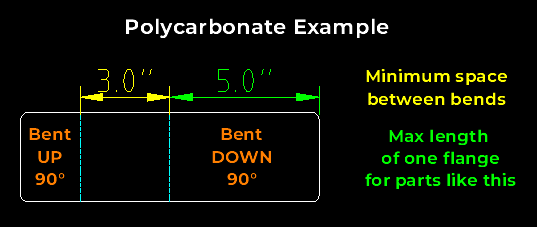
All set to offset!
Joggle bends come with additional considerations, so we’ve provided specs to cover most bending design scenarios. If you run into trouble with a joggle part just ask our Support team for help. Once your file is ready, upload it to our website for an instant quote!