Bending polycarbonate comes with a different set of considerations than forming sheet metal. Learn about critical limits and design requirements for plastic bending to ensure your parts are processed successfully!
Critical limitations when bending polycarbonate
- Maximum of 3 bends per part
- Polycarbonate parts with more than 3 bends require a custom quote
- Max angle 90 degrees, min angle 45 degrees
- 3:1 base to flange required for u-channel bends
- No joggles; parallel bends in opposite directions can be bent in polycarbonate as long as the flanges are at least 3″ apart if measuring from the center or apex of each bend, and one of the flanges is no longer than 5″
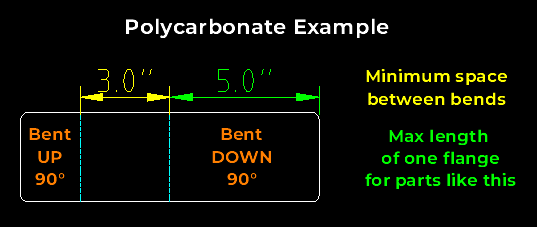
- To avoid cracking, polycarbonate parts must have
- at least the minimum bend relief required
- rectangular bend reliefs only

General considerations for polycarbonate bending
- Polycarbonate has larger bend angle tolerances than sheet metal; confirm tolerances by bend length in the polycarbonate specifications
- In order to form polycarbonate, flanges must be overbent to achieve the desired angle due to the springback of the material
- This means that some designs that can be formed in sheet metal may not be feasible in plastic
- See below: material bent to 120-130 degrees in order to achieve 90 degree bend
- Since polycarbonate parts must be overbent to achieve the desired angle, ensure that adjacent or corner flanges have sufficient clearance to avoid collision
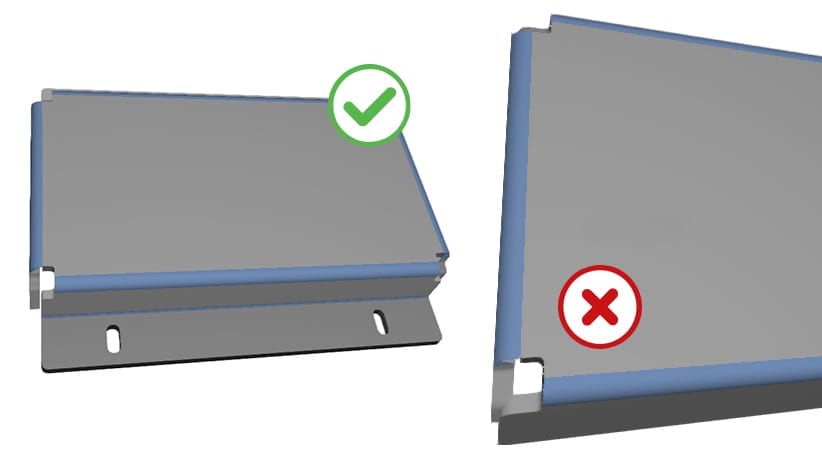
- Polycarbonate parts may have minor surface edge cracks depending on the material thickness and flange angle
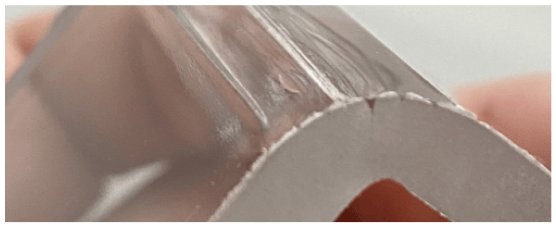
- If holes are within the die lines, they will distort
- Witness marks may not be visible the way they are on bent sheet metal parts, however we cannot guarantee that they won’t be present
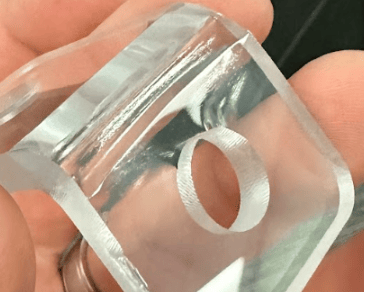
- We bend and ship polycarbonate parts with its protective film on
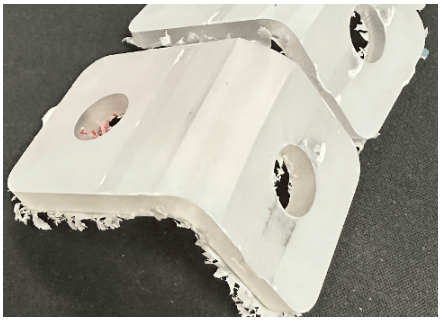
- Polycarbonate parts will have noticeable cracking in stressed areas if adequate relief is not provided for each bend
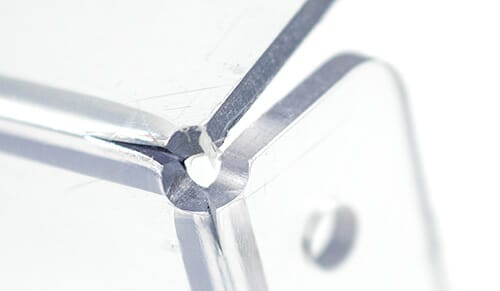
Plastic bending made clear!
Forming plastic comes with certain limitations due to the nature of the material. Use the list we’ve provided here and our bending guidelines to ensure your polycarbonate parts are set up for success before uploading your design file to our website for an instant quote!