Our bending and forming service requirements are detailed in our Bending Guidelines. Here’s a checklist of bending considerations to review before uploading your part files!
Tip: all bending specifications for each material thickness can be found in our Material Catalog.
Critical bending requirements
Ensure your part meets our critical bending requirements for best results with your parts!
Upload a file format we accept with bends included
Upload either a 2D .dxf, .dwg, .ai, or .eps format vector file or a 3D .step or .stp format file with your part design.
For 2D files, bend locations should be indicated with a dashed line for .dxf and .dwg files and a solid line in a separate color for .ai or .eps files. After you upload your file, you’ll be able to add bending services and set angle and direction definitions for each bend line.
For 3D .step or .stp format files, you don’t need to worry about bend lines. Make sure the design meets our 3D File Guidelines, though!
If you’re working in a 3D CAD design software you can model your part, set your bend definitions, export your .step file, and upload it for an instant quote. Double check the bend definitions after uploading to ensure they’re correct!
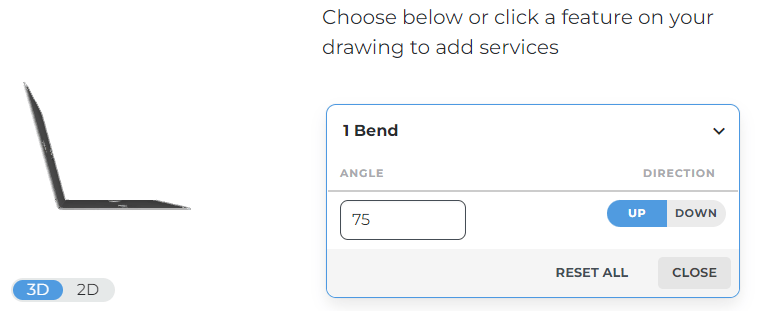
Material options, overall flat part size limits (pre-bend), and maximum bend length
Confirm which material thicknesses are eligible for bending, the minimum and maximum overall flat (pre-bend) part sizes allowed, and the maximum possible bend length in our Processing Size Chart.
Material thickness eligibility, overall flat part size limits, and maximum bend length specifications are also listed in our Material Catalog.
Reference SendCutSend’s bend radius for the material
Each material we bend has an effective inside bend radius that is set per material thickness. We do not offer custom bend radii at this time.
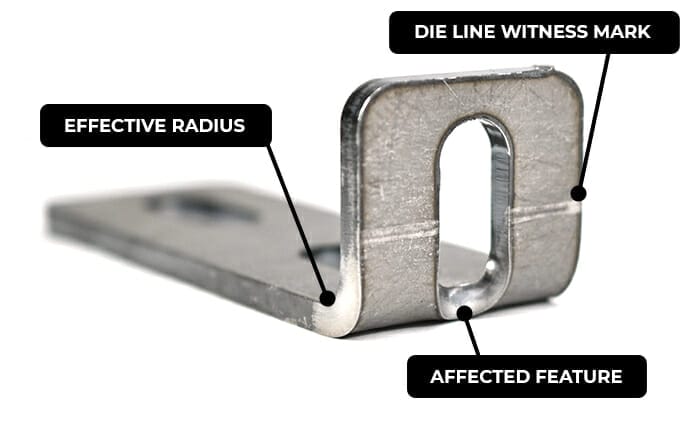
Confirm SendCutSend’s bend radius and other specifications for each material thickness in our handy bend specification table or in our Material Catalog.
Please note; bend radius may not always correlate with material thickness in a linear fashion.
- Using Autodesk Fusion or SolidWorks? Download our gauge tables to easily apply the latest specs!
Use SendCutSend’s bend deduction calculator
If you’re designing in a 2D CAD program or sketching your part, use our Bending Calculator to ensure the flat dimensions you design result in the formed dimensions you need.
If you’re designing in a 3D CAD software like Autodesk Fusion or SolidWorks, create sheet metal rules that match SendCutSend’s bending specifications for material thickness, bend radius, and K factor.
Solidworks users can download our custom bend tables to specify exact bend allowances, bend deductions, bend radii, and K-factors so your file is tailored to our manufacturing processes.
Autodesk Fusion users can import SendCutSend sheet metal rules by following our gauge table guide.
Meet the minimum flange length
Each material thickness has a minimum flange length requirement that you can confirm in the material specifications. Learn more about flange requirements and how to measure flanges.
Check bend angle requirements
Each material thickness has a minimum and maximum possible bend angle that we can form.
The maximum bend angle we can form ranges from 90-130 degrees depending on the material thickness. Confirm the bend angle capabilities for the material you need in our catalog.
Additional bending guidelines
While all of our bending requirements are important, the guidelines below can be more or less relevant depending on your unique design and material choice.
- Avoid part deformation
- If bends aren’t well supported or cut features are too close to bend locations, distortion can occur and impact the success of your part. Learn how to avoid deformation in our Bending Deformation Guidelines.
- Bend reliefs are highly recommended if adjacent bends meet at a corner. Learn about our bend relief requirements.
- Meet our channel bending guidelines
- Our channel bending limits depend on whether you’re bending sheet metal or plastic. Learn about our channel bending capabilities.
- Meet our joggle, window, and recessed bend guidelines
- These types of bends have specific limits. Learn about our joggle bend, window bend, and recessed bend requirements in our dedicated writeups!
- For odd or irregular flange shapes, add an edge that is parallel to the bend
- To bend flanges, we need a flat edge on your part that is parallel to the bend location. Learn how to add break-off tabs to odd flanges.
- Polycarbonate parts have additional considerations
- Bending plastic comes with a few more limitations than sheet metal. Learn what to keep in mind when designing polycarbonate parts with bending services!
Check it, send it, bend it!
Use this bending checklist as a review tool before uploading your part files for an instant quote! Take a look at the complete bending guidelines for all considerations, and reach out to our Support team anytime if you have questions!